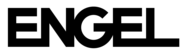
Catalog excerpts
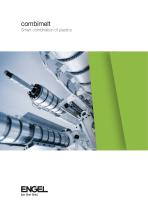
Smart combination of plastics
Open the catalog to page 1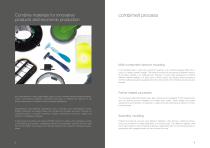
Combine materials for innovative products and economic production combimelt process M ulti-component injection moulding In the simplest case – multi-colour injection moulding – the combined plastics differ only in colour, to create a specific design. This method involves the processing of different colours, of the same material, in an individual part. However, it is also often necessary to combine different material qualities in a given part. In these cases, the plastics should possess a common adhesive quality to guarantee that the components of the finished part are securely bonded. F...
Open the catalog to page 2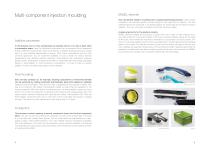
Multi-component injection moulding ENGEL skinmelt Two-component injection moulding with a special plasticising process: Unlike classic coinjection, the skinmelt process involves fusing the two melts prior to injection. The skin material reaches the cavity first. It is pressed against the cavity walls by the injected second material – the core. The result is sandwich parts with premium quality. Additive processes In this process, two or more components are injected next to or on top of each other in successive steps. Here the individual components form a permanent bond (sequential linking of...
Open the catalog to page 3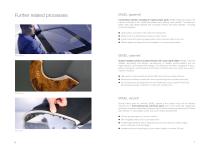
Further related processes ENGEL glazemelt Combination injection moulding for large-surface parts: ENGEL glazemelt enables the injection moulding of flat, crystal-clear plastic parts, offering many benefits. This glazing is lighter, offers total design flexibility and combines perfectly with other materials – including functional integration. Large-surface, low-stress multi-component optical parts Machine with low clamping force thanks to stack moulds A great method for producing large-surface multi-component parts of any kind Flexible design and optimal functional integration in the...
Open the catalog to page 4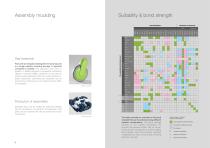
Assembly moulding Suitability & bond strength Seal assembly Parts with an integrated sealing element are produced in a single injection moulding process. A rigid-soft composite is created. One application area is the integration of sealing elements by sequential combination injection moulding. ENGEL combimelt can be used to produce sealing elements both from cured and thermoplastic elastomers. Optimised part properties can be achieved by combining up to 6 components with different properties. Production of assemblies Moveable joints can be created by selecting materials that do not adhere...
Open the catalog to page 5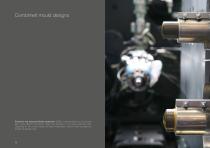
Combimelt mould designs Economic and resource-friendly production: ENGEL combimelt allows you to produce parts using different components, safely and efficiently, in one single production step. Depending on the product design and type of application, various mould concepts can provide the desired result.
Open the catalog to page 6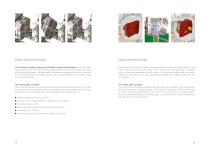
Rotary table technology Index plate technology The universal, efficient solution for all ENGEL combimelt processes: rotary table technology allows you to meet the most diverse requirements of combination injection moulding with precision and speed. The rotary table is integrated as a fixed module of the moving platen of the ENGEL injection moulding machine. You have the flexibility to use multiple moulds on one production cell. Great flexibility in the product design: The index plate technology is the perfect solution if you want to add components to both sides of the moulded part. The...
Open the catalog to page 7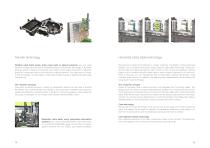
Transfer technology Horizontal rotary table technology Whether small batch series, bulky insert parts or special solutions: you can easily transfer moulded parts during the combimelt process using transfer technology. Automation gives you plenty of options: for example, if you want to insert bulky components or efficiently produce 4-component parts on two injection moulding machines. You might want to consider this technology if a rotary table or index plate solution requires a disproportionately large clamping unit. Manufacture moulded parts efficiently on smaller machines. The ENGEL combi...
Open the catalog to page 8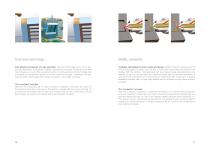
Core-back technology ENGEL coinjection Cost-effective production of small quantities: core-back technology allows you to produce moulded parts, using several materials, easy and economically. Though the cycle time may increase as a result of the sequential injection moulding process, this technology does not require any manipulation devices during the combimelt process. Furthermore, the relatively compact mould design often makes it possible to use smaller machines. Intelligent optimisation of costs, quality and design: ENGEL coinjection allows you to not only produce parts at a lower cost,...
Open the catalog to page 9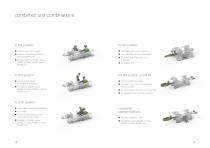
in H/L position ■ Ideal for larger shot weights ■ Flexible, horizontal adjustability for mould parting line ■ Can be retrofit on ENGEL victory, ENGEL e-victory, ENGEL e-motion ENGEL duo in H/H position ■ Particularly shoot nozzle distance ■ Two units with horizontal adjustability' ■ For rotary table units up to 2.5 m in diameter ■ For ENGEL duo in H/V position ■ Space-saving variant for smaller shot weights ■ Available for ENGEL victory, ENGEL e-victory, ENGEL e-motion ENGEL duo in H/M position combi M ■ Unit on a stationary platen ■ "Movable” unit on the moving mould mounting platen ■ For...
Open the catalog to page 10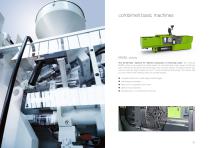
ENGEL victory The tie-bar-less machine for efficient production of technical parts: the universal ENGEL victory is your perfect modular system for manufacturing a wide range of technical parts. With its proven tie-bar-less technology, this compact injection moulding machine can even be used for large moulds common to multi-component technology. This means that you only invest in the clamping force you actually require. ■ Universal machine for a wide variety of technologies ■ Low energy consumption ■ More room for automation and mould ■ Optimal mould protection ■ Clamping force - from 600 kN...
Open the catalog to page 11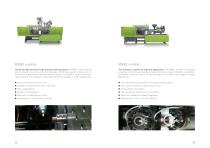
ENGEL e-victory The tie-bar-less machine for high-precision technical parts: the ENGEL e-victory delivers premium quality to meet the strictest of standards. With its servo-electric injection unit, tie-bar-less mould area and low-emission drive technology, the ENGEL e-victory is the smart, clean choice for the production of precision technical mouldings or small medical parts. ■ Precise, servo-electric injection unit ■ Suitable for moulds with and without core-pulls ■ High energy efficiency ■ Excellent mould protection ■ More room for automation and mould ■ Clamping force - from 800 kN to...
Open the catalog to page 12All ENGEL AUSTRIA GmbH catalogs and technical brochures
-
press | release
4 Pages
-
ENGEL services
9 Pages
-
Plasticising unit
15 Pages
-
Composite Technologies
13 Pages
-
automotive
19 Pages
-
Amorphous Metal Moulding
5 Pages
-
smart service
11 Pages
-
smart machine
15 Pages
-
Automation
41 Pages
-
engel AUTOMATIUON
15 Pages
-
ENGEL INSERT
15 Pages
-
Trining
11 Pages
-
protect
3 Pages
-
iQ weight control
2 Pages
-
Engel Flomo
16 Pages
-
Scope of products
29 Pages
-
CC300
7 Pages
-
e-motion 30 TL
8 Pages
-
ENGEL plus
2 Pages
-
ENGEL e-cap
3 Pages
-
ENGEL e-mac
11 Pages
-
ENGEL elast
11 Pages
-
ENGEL insert PRO
7 Pages
-
ENGEL combimelt
5 Pages
-
Customized Soft-Touch
3 Pages
-
Engel EXJECTION®
4 Pages
-
ENGEL e-factory
4 Pages
Archived catalogs
-
e-motion TL
9 Pages
-
ENGEL e-victory
17 Pages
-
ENGEL e-motion
17 Pages
-
ENGEL duo
19 Pages
-
ENGEL victory
15 Pages
-
ENGEL Control
8 Pages
-
ENGEL VIPER
13 Pages
-
speed injection moulding machine
10 Pages