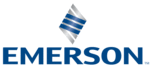

Catalog excerpts
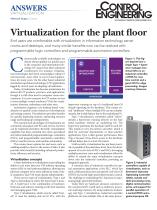
VIRTUALIZATION Vibhoosh Gupta, Emerson ELECTRONICALLY REPRINTED FROM DECEMBER 2019 Virtualization for the plant floor End users are comfortable with virtualization in information technology server rooms and desktops, and many similar benefits now can be realized with programmable logic controllers and programmable automation controllers. ommercially available technologies are almost always applied at a quicker pace in the consumer and information technology (IT) space than their industrial counterparts. For instance, virtualization technologies have been commonplace within IT environments, most often in server-based applications, for many years. On the other hand, industrial automation operations technology (OT) applications lagged by several years in adopting virtualization. Today, virtualization has become mainstream for almost all OT products, practices, and applications, though it is still often used in computer-room environments. It is now common for OT system servers to host multiple virtual machines (VMs) for visualization, historian, redundancy and other uses. Automation engineers use desktop-based virtualization to quickly create instances of development and testing systems. Virtualization provides benefits for quickly deploying systems, optimizing resource usage and backing up configurations. The concepts and advantages of virtualization are commonly associated with PCs and servers, but they can be employed elsewhere. Recently, virtualization capability has been extended into more specialized and robust industrial programmable logic controllers (PLCs) and programmable automation controllers (PACs) used for process and machine automation. This creates more options for end users, such as enabling analytics closer to the source of data. It also provides other benefits including enhanced productivity, efficiency and security. Virtualization concepts A basic definition of virtualization is providing the ability to run more than one VM software operating system (OS) on one hardware platform, allowing one physical computer to be more utilized as many virtual computers. Each VM must operate independently. There are two types of virtualization, Type 1 and Type 2, depending on where the hypervisor is located. A hypervisor is the combination of hardware, firmware, and software running on the host machine and managing guest VMs. Type 2 virtualization, which may be called “hosted,” is used for desktop and server PCs, with the Figure 1: This figure depicts how a single Type 1 hypervisor manages two virtual OSs on an industrial controller, a RTOS for realtime control and a guest OS for edge processing. Images courtesy: Emerson hypervisor running on top of a traditional host OS already operating on the hardware. This creates virtual “sandboxes” where multiple OSs can run simultaneously, but it adds latency due to the underlying OS. Type 1 virtualization, sometimes called “native,” utilizes a hypervisor running directly on the bare metal hardware without an underlying OS. The hypervisor partitions the hardware itself to each OS. This results in very low latency and jitter, which is ideal for real-time deterministic or time-sensitive applications. Type 1 offers greater performance than Type 2 because it has direct access to the hardware without delays due to a host OS system. Until recently, virtualization has not been practical or possible at the plant floor level. Now, the development of a new class of PLCs and PACs leveraging multiple processor cores and virtualization offers the ability to extend the same virtualization concepts down into the industrial controller, providing an integrated approach. A common class of industrial controller for typical automation applications is the PLC, which has used a dedicated processor and specific real-time OS (RTOS) to provide high-speed deterministic control. The challenge to virtualizing PLC functions is maintaining high-speed determinism. Today there are hardware advances common to the commercial PC world such as multicore processors and large memory. By using multicore technology and Type 1 virtualization, industrial controller platforms can run multiple OSs on the same proces- Figure 2: Industrial controllers capable of virtualization, such as Emerson’s Outcome Optimizing Controller (OOC), include multiple processing cores, digital communication ports, and support for parallel operation of a control RTOS and a general-
Open the catalog to page 1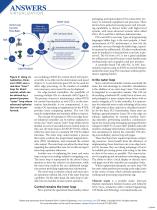
Figure 3: Using virtualization, Emerson’s OOC uses a real-time “inner” loop for direct control, which can be advised by a general purpose “outer” loop where advanced optimization can be performed. sor, including a RTOS for control which will experience little to no effect on the determinism and speed (Figure 1). A second Linux guest OS can be used for other edge processing. As the number of available cores increases, even more OSs can be deployed. For edge-located controllers, the possibility of running multiple OSs is a dramatic shift (Figure 2). The primary concern is maintaining a robust...
Open the catalog to page 2All Emerson catalogs and technical brochures
-
Industrial Power Supplies
12 Pages
-
RXi Industrial Displays
7 Pages
-
PACMotion VFD
8 Pages
-
PACSystems RX3i I/O
8 Pages
-
VersaPoint I/O
4 Pages
-
CS803 and CS823
2 Pages
-
PACMotion VFD
5 Pages
-
VersaMax MicroMotion
4 Pages
-
PACSystems RX3i CPL410
4 Pages