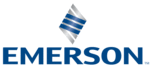

Catalog excerpts
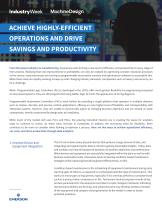
ACHIEVE HIGHLY-EFFICIENT OPERATIONS AND DRIVE SAVINGS AND PRODUCTIVITY From the power industry to manufacturing, businesses want to bring a new level of efficiency and productivity to every stage of their process. Realizing that real improvements to profitability can only be realized by optimizing complex industrial processes at the source, many businesses are turning to programmable automation controls and optimization software to accomplish this. While these tools are rapidly evolving to keep up with changing industry demands, complexities such as latency and security can be a challenge. While Programmable Logic Controllers (PLCs), developed in the 1970s, offer much greater flexibility for programming compared to relay-based systems, they are still programmed using ladder-logic to mimic the appearance of wiring diagrams. Programmable Automation Controllers (PACs) went further by providing a single platform that operates in multiple domains such as motion, discrete, and process control applications, offering an even higher level of flexibility and interoperability with enterprise systems. However, they are unable to dynamically adjust to changing business objectives and are viewed as static components, heavily constrained by design spec at installation. While much of the market still uses PLCs and PACs, the growing industrial Internet era is creating the space for analytics tools to continue to evolve. As these tools increase in complexity to address the increasing need for flexibility, there continues to be more to consider when looking to optimize a process. Here are five ways to achieve operational efficiency, cut costs, and drive productivity through data analytics: 1. mprove Device and I Equipment Integration The IoT era involves many physical devices that produce a large amount of data, and integrating and organizing this data is critical to gaining meaningful insights. Today, data and analytics can help tie equipment operation to business objectives and performance. When devices and equipment are successfully integrated within the plant as well as with business automation tools, it becomes easier to develop condition-based maintenance strategies while improving Overall Equipment Effectiveness, or OEE. Condition-based maintenance is the scheduling of equipment maintenance during early warning signs of failures, as opposed to a scheduled/calendar type of maintenance. This works on many types of equipment, especially if it is one that performs a consistent task such as a pump, motor, compressor, or fan. Technicians look at long-term trends of key process parameters for the equipment and learn to spot changes in behavior indicating mechanical problems are forming, and advanced users may develop statistical models of the equipment and compare existing behavior to the model in order to locate potential problems.
Open the catalog to page 1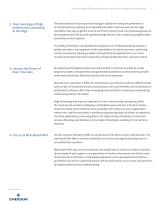
Achieve Highly-Efficient Operations and Drive Savings and Productivity 2. ake advantage of highT performance computing at the Edge The latest advances in processor technology is rapidly increasing the performance of industrial devices, leading to an expanded and often multi-purpose role for edge controllers. One way to get the most of out of the inherent multi-core processing power of the new generation of outcome-optimizing edge devices is by virtualizing programmable automation control systems. The ability of hardware virtualization techniques to run multiple operating systems in tandem...
Open the catalog to page 2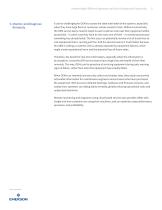
Achieve Highly-Efficient Operations and Drive Savings and Productivity 5. onitor and Diagnose M Remotely It can be challenging for OEMs to assess the state and health of the systems, especially when they have large fleets or numerous remote assets to track. Without connectivity, the OEM service teams need to travel to each customer who uses their equipment either proactively – in which case they have to visit every one of them – or reactionary because something has already failed. The first case can potentially involve a lot of travel time to visit equipment that is running just fine. And...
Open the catalog to page 3All Emerson catalogs and technical brochures
-
Industrial Power Supplies
12 Pages
-
RXi Industrial Displays
7 Pages
-
PACMotion VFD
8 Pages
-
PACSystems RX3i I/O
8 Pages
-
VersaPoint I/O
4 Pages
-
CS803 and CS823
2 Pages
-
PACMotion VFD
5 Pages
-
VersaMax MicroMotion
4 Pages
-
PACSystems RX3i CPL410
4 Pages