
Catalog excerpts
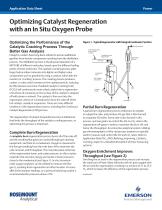
Application Data Sheet Optimizing Catalyst Regeneration with an In Situ Oxygen Probe Optimizing the Performance of the Catalytic Cracking Process Through Better Gas Analysis Catalytic crackers have long been utilized to extract additional gasoline from heavier components resulting from the distillation process. The distillation process is the physical separation of a MIXTURE of different molecules, based upon the different boiling points of these molecules. The catalytic cracking process splits larger hydrocarbon molecules into lighter and higher value components such as gasoline by using a catalyst, which aids the reaction or "cracking" process. The cracking process produces carbon, or coke, which remains on the catalyst particle, reducing its effectiveness over time. Fluidized Catalytic Cracking Units (FCCU) will continuously route coked catalyst into a regenerator unit where oil remaining on the surface of the catalyst is stripped off with steam or solvent. The catalyst is then sent into the regenerator, where air is introduced to burn the coke off of the hot catalyst, usually in suspension. There are many different variations in the regeneration process, including the Continuous Catalyst Regenerator (CCR) process. The regeneration of catalyst frequently becomes a bottleneck that limits the throughput of the catalytic cracking process, so optimizing this process is important. Complete Burn Regeneration A complete burn regeneration process burns all of the coke off, and the resulting flue gases are routed through gas-cleaning equipment, and then to a smokestack. Oxygen is measured in the flue gas resulting from the coke burn-off to maximize the coke removal, and throughput. This may take place at the top of the regeneration tower, and under pressure, or after a turboexpander that recovers energy and results in lower pressures closer to the smokestack (see Figure 1). In-situ zirconiumoxide oxygen analyzers can be utilized to measure the flue gas O2 resulting from regeneration in either location. Pressure affects the analyzer readings, so a pressure balancing system is recommended for pressures above 2 PSI. Figure 1 - Typical Regenerator with Integral Combustor Section To Fractionation O2 Probe Mounted in Duct Work or Stack Combustor-style Regenerator Open Riser System Combustor Riser Hot-Catalyst Circulation Catalyst Cooler Lift Media Partial Burn Regeneration A partial burn regeneration process endeavors to volatize, or outgas the coke, and produce CO gas that is then burned in a separate CO boiler. Some coke is also burned in this process, and one goal is to control the CO-to-CO2 ratio in the regeneration off-gases in order to maximize the burn-off, and hence the throughput. An extractive analytical system utilizing gas chromatographs or Infra-red process analyzers is typically used to measure and control the CO and CO2 ratios. Refer to Application Note PGC_ANO_Refining_Improving_Catalytic_ Cracking_Vapor for a detailed description of these measuring systems. Oxygen Enrichment Improves Throughput (see Figure 2) Enriching the air used in the regeneration process can increase the coke burn-off rate. Many refineries will mix pure oxygen with the air used for regeneration, resulting in a mixture of 21 to 25 % O2, which increases the efficiency of the regeneration process. continued...
Open the catalog to page 1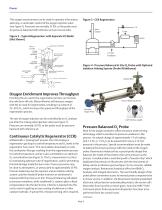
This oxygen measurement can be used for operator information, alarming, or automatic control of the oxygen injection valve (see Figure1). Pressures are normally 35 PSI, so the probe must be pressure-balanced with reference air (see reverse side). Spent Catalyst Figure 2 - Typical Regenerator with Separate CO Boiler (Not Shown) Plenum Chamber 2 Stage Cyclone Separators Dip Leg Spent Catalyst from Reactor Fluidized Catalyst Bed Air Grid Liquid Oxygen Tank Vaporization Uunit Figure 4 - Pressure Balanced in Situ O2 Probe with Optional Isolation Valving System (Probe Withdrawn) Spent Catalyst...
Open the catalog to page 2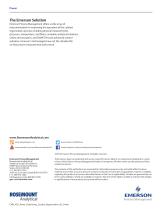
The Emerson Solution Emerson Process Management offers a wide array of instrumentation for improving the operation of the catalyst regeneration process including physical measurements (pressure, temperature, and flow), complete analytical solutions, valves and actuation, and SMART Process advanced control solutions. Emerson’s technologies have set the standard for on-line process measurement and control. www.RosemountAnalytical.com www.analyticexpert.com ©2013 Emerson Process Management. All rights reserved. Emerson Process Management Rosemount Analytical Inc. Analytical Center of...
Open the catalog to page 3All Emerson Automation Solutions - ROSEMOUNT catalogs and technical brochures
-
VPS 53 Vapor Pressure Sensor
2 Pages
-
EasyHeat™ XD Cable Kits
2 Pages
-
FRL Accessories
14 Pages
-
TankRadar Pro
32 Pages
-
Rosemount™ 2140 Level Detector
22 Pages
-
Roxar subsea PIG
2 Pages
-
Roxar subsea Sand monitor
2 Pages
-
Roxar subsea CM10K
2 Pages
-
Roxar PTPT15K
2 Pages
-
Rosemount TankRadar OFC
2 Pages
-
SW-300
4 Pages
-
DL8000
12 Pages
-
DeltaV Analyze
8 Pages
-
AMS Machine Works
4 Pages
-
DeltaV Executive Portal
7 Pages
-
1500XA Gas Chromatograph
8 Pages
-
Rosemount 975UR
4 Pages
-
Rosemount 975HR
4 Pages
-
Rosemount 975UF
4 Pages
-
Rosemount 975MR
4 Pages
-
CT5400 Process Gas Analyzer
4 Pages
-
CT2211 Leak Detection System
4 Pages
-
Desalination of Seawater
2 Pages
-
700XA Process Gas Chromatograph
12 Pages
-
SafeGuard Alarm Controller
2 Pages
-
Safety Monitoring
6 Pages
-
AMS Suite
16 Pages
-
Drinking Water Sht 2V2
2 Pages
-
Line Card
2 Pages
-
Drinking Water Industry
16 Pages
-
Explosion Proof Video Camera
2 Pages
-
Net Safety UV Flame Detector
4 Pages
Archived catalogs
-
UV/IRS Flame Detector
4 Pages
-
UVS Flame Detector
4 Pages