
Catalog excerpts
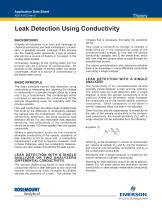
Application Data Sheet Leak Detection Using Conductivity BACKGROUND Virtually all industries from food and beverage to chemical processing use heat exchangers, condensers, or jacketed vessels. Leakage of the process into the cooling water represents a loss of product and can be a source of fouling or corrosion in the cooling water system. Conversely, leakage of the cooling water into the process can be a source of contamination. An example is the leakage of cooling water into steam condensate, which is a source of contamination in the steam-water circuit. BASIC PRINCIPLE The basic principle behind leak detection using conductivity is measuring and alarming the change in conductivity in a sample brought about by a leak into it by a contaminant.The contaminant either increases or decreases the conductivity of the sample depending upon its solubility with the process solution. How well conductivity can detect leaks is determined first of all by the difference in conductivity between the sample and the contaminant. The greater the conductivity difference, the more sensitive leak detection will be. For any reasonable leak detection sensitivity, the conductivity of the contaminant should be at least 100 times greater than the sample conductivity. Where a specification exists for the maximum allowable conductivity of the sample, sensitivity of leak detection is not an issue and a conductivity measurement is all that is required. However, even in these instances, using two conductivity measurements can often isolate and identify the leak source. LEAK DETECTION WITH A SINGLE ANALYZER OR TWO ANALYZERS (DIFFERENTIAL CONDUCTIVITY). The second determining factor in how effective conductivity will be in leak detection is how much the sample conductivity must increase to reliably indicate the presence of a leak. The smaller the increase that is necessary, the better the sensitivity will be. How large a conductivity change is needed is determined by 1) the conductivity range of the uncontaminated sample; 2) how fast the sample conductivity changes; and 3) the transit time, which tells how long the sample takes to pass through the potential leak source. The above considerations also determine whether there is an advantage in using differential conductivity over using a single analyzer. LEAK DETECTION WITH A SINGLE ANALYZER The conductivity of an uncontaminated sample normally varies between a high and low extreme. The worst case for leak detection with a single analyzer is when the sample conductivity is at its minimum. A leak can be present, which increases the conductivity up to the normal sample maximum conductivity. Since conductivity is not above a normal, expected value, the leak is not detected. Given this fact and the dependence of sensitivity on the ratio of the sample conductivity to the contaminant conductivity, the overall sensitivity (Ss) with a single analyzer can be estimated from the following: Equation (1) SS = where SS is the sensitivity in volume of contaminant per volume of sample; KH and KL are the maximum and minimum normal sample conductivity; and KC is the contaminant conductivity. Sensitivity with a single analyzer is limited by the normal variations in sample conductivity. Alarming for leak detection should be set at approximately 5% full scale above the maximum normal conductivity or other reliably measurable conductivity increase.
Open the catalog to page 1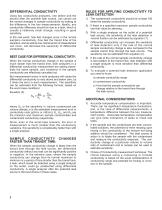
DIFFERENTIAL CONDUCTIVITY Using two conductivity analyzers, one before and the second after the possible leak source, can cancel out the normal changes in sample conductivity by looking at the difference in the two measurements. Ideally, any conductivity difference should be due to a leak, which is usually a relatively small change, resulting in good sensitivity. In the real world, how fast changes occur in the normal sample’s conductivity, how fast the transit time of the sample is, and as well as how normal errors of measurement can occur, will decrease the sensitivity of differential...
Open the catalog to page 2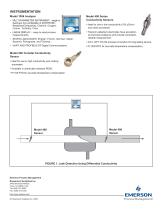
INSTRUMENTATION Model 1056 Analyzer • MULTI-PARAMETER INSTRUMENT – single or dual input. Any combination of pH/ORP/ISE, Resistivity/Conductivity, Chlorine, Oxygen, Ozone, Turbidity, Flow. • LARGE DISPLAY – easy-to-read process measurements. • SEVEN LANGUAGES: English, French, German, Italian, Spanish, Portuguese, and Chinese. • HART AND PROFIBUS DP Digital Communications. Model 400 Series Conductivity Sensors • Ideal for use in low conductivity (100 µS/cm) and clean processes • Titanium palladium electrodes have exceptional chemical resistance and provide consistent, reliable measurement. •...
Open the catalog to page 3All Emerson Automation Solutions - ROSEMOUNT catalogs and technical brochures
-
VPS 53 Vapor Pressure Sensor
2 Pages
-
EasyHeat™ XD Cable Kits
2 Pages
-
FRL Accessories
14 Pages
-
TankRadar Pro
32 Pages
-
Rosemount™ 2140 Level Detector
22 Pages
-
Roxar subsea PIG
2 Pages
-
Roxar subsea Sand monitor
2 Pages
-
Roxar subsea CM10K
2 Pages
-
Roxar PTPT15K
2 Pages
-
Rosemount TankRadar OFC
2 Pages
-
SW-300
4 Pages
-
DL8000
12 Pages
-
DeltaV Analyze
8 Pages
-
AMS Machine Works
4 Pages
-
DeltaV Executive Portal
7 Pages
-
1500XA Gas Chromatograph
8 Pages
-
Rosemount 975UR
4 Pages
-
Rosemount 975HR
4 Pages
-
Rosemount 975UF
4 Pages
-
Rosemount 975MR
4 Pages
-
CT5400 Process Gas Analyzer
4 Pages
-
CT2211 Leak Detection System
4 Pages
-
Desalination of Seawater
2 Pages
-
700XA Process Gas Chromatograph
12 Pages
-
SafeGuard Alarm Controller
2 Pages
-
Safety Monitoring
6 Pages
-
AMS Suite
16 Pages
-
Drinking Water Sht 2V2
2 Pages
-
Line Card
2 Pages
-
Drinking Water Industry
16 Pages
-
Explosion Proof Video Camera
2 Pages
-
Net Safety UV Flame Detector
4 Pages
Archived catalogs
-
UV/IRS Flame Detector
4 Pages
-
UVS Flame Detector
4 Pages