
Catalog excerpts
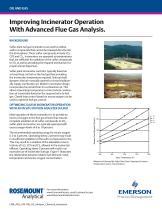
Improving Incinerator Operation With Advanced Flue Gas Analysis. BACKGROUND Sulfur plant tail gas incinerators are used to oxidize sulfur compounds that cannot be released directly into the atmosphere. These sulfur compounds include H2S, COS and CS2. Incinerators are operated at temperatures that are sufficient for oxidation of the sulfur compounds to SO2 as well as providing the required mechanism for proper plume dispersion. Sulfur plant incinerator control is typically based on a closed loop control on the fuel gas flow providing the incinerator temperature required. Natural draft dampers that are manually opened or closed traditionally supply combustion air. Modern incinerator design incorporates forced draft air for combustion air. This allows closed loop temperature control where combustion air is provided based on the required ratio to fuel gas. Closed loop control based on excess oxygen can be used to optimize fuel gas control. OPTIMIZING SULFUR INCINERATOR OPERATION WITH AN IN SITU OXYGEN ANALYZER SULFUR The recommended operating range for excess oxygen is 2 to 5 percent. Operating below 2 percent may result in insufficient oxidation of the sulfur compounds to SO2. This may result in a violation of the allowable concentrations of H2S, COS and CS2 allowed in the incinerator effluent. Operating above 5 percent will result in an excessive use of incinerator fuel gas. Figure 1 illustrates the relationship between relative fuel demand, stack temperature and excess oxygen concentration. • Relative Fuel Demand (Percent) Ideal operation of these incinerators is to provide an excess of oxygen in the flue gas stream that ensures complete oxidation of all sulfur compounds to SO2. Sulfur plant incinerators are typically operated with excess oxygen levels of 6 to 10 percent. Relative Fuel Demand for Sulfur Plant Stack Operated at Various Temperatures and O2 Concentrations For more information www.EmersonProcess.com/CustomerSuccess www.RosemountAnalytical.com
Open the catalog to page 1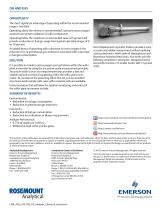
OIL AND GAS OPPORTUNITY The most significant advantage of operating within the recommended range is two-fold: Operating above the minimum recommended 2 percent excess oxygen would ensure proper oxidation of sulfur compounds. Operating below the maximum recommended value of 5 percent will provide a reduction in fuel gas usage from typical operating ranges of 6 to 10 percent. An added bonus of operating with a decrease in excess oxygen is the reduction CO2 (a greenhouse gas) emissions associated with a decrease in fuel gas consumption. SOLUTION It is possible to monitor excess oxygen...
Open the catalog to page 2All Emerson Automation Solutions - ROSEMOUNT catalogs and technical brochures
-
VPS 53 Vapor Pressure Sensor
2 Pages
-
EasyHeat™ XD Cable Kits
2 Pages
-
FRL Accessories
14 Pages
-
TankRadar Pro
32 Pages
-
Rosemount™ 2140 Level Detector
22 Pages
-
Roxar subsea PIG
2 Pages
-
Roxar subsea Sand monitor
2 Pages
-
Roxar subsea CM10K
2 Pages
-
Roxar PTPT15K
2 Pages
-
Rosemount TankRadar OFC
2 Pages
-
SW-300
4 Pages
-
DL8000
12 Pages
-
DeltaV Analyze
8 Pages
-
AMS Machine Works
4 Pages
-
DeltaV Executive Portal
7 Pages
-
1500XA Gas Chromatograph
8 Pages
-
Rosemount 975UR
4 Pages
-
Rosemount 975HR
4 Pages
-
Rosemount 975UF
4 Pages
-
Rosemount 975MR
4 Pages
-
CT5400 Process Gas Analyzer
4 Pages
-
CT2211 Leak Detection System
4 Pages
-
Desalination of Seawater
2 Pages
-
700XA Process Gas Chromatograph
12 Pages
-
SafeGuard Alarm Controller
2 Pages
-
Safety Monitoring
6 Pages
-
AMS Suite
16 Pages
-
Drinking Water Sht 2V2
2 Pages
-
Line Card
2 Pages
-
Drinking Water Industry
16 Pages
-
Explosion Proof Video Camera
2 Pages
-
Net Safety UV Flame Detector
4 Pages
Archived catalogs
-
UV/IRS Flame Detector
4 Pages
-
UVS Flame Detector
4 Pages