
Catalog excerpts
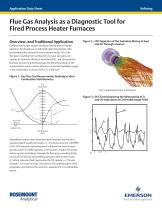
Application Data Sheet Flue Gas Analysis as a Diagnostic Tool for Fired Process Heater Furnaces Overview, and Traditional Application Combustion flue gas analysis has been used by process heater operators for decades as a method of optimizing fuel/air ratio. By measuring the amount of excess oxygen and/or CO in the flue gases resulting from combustion, furnace operators can operate at optimum efficiency and lowest NOx, and also generate the least amount of greenhouse gas.The theoretical ideal, or the stoichiometric point is where all fuel is reacted with available oxygen in the combustion air and no fuel or O2 is left over. Figure 2 - CFD Depiction of the Turbulent Mixing of Fuel and Air Through a Burner Figure 1 - Key Flue Gas Measurements Relating to Ideal Combustion Stoichiometry % of Stack Gases The "combustion process" is the burner. Figure 3 - DCS Trend Depicting the Relationship of O2 and CO Indications at CO Breakthrough Point Air-to-Fuel Mixture Rich (Deficient Air) Stoichiometric Point Operating furnaces never attain this ideal, however, and the best operating point usually will result in 1–3 % excess air and 0–200 PPM of CO. This optimum operating point is different for every furnace and also varies for differing loads, or firing rates. A higher firing rate induces greater turbulence through the burner(s), providing better mixing of fuel and air, and enabling operation with a lower excess O2 before unburned fuel (represented by CO) appears, or “breaks through”. For most furnaces, this point of CO breakthrough is fairly repeatable, and reduces the need for a separate CO or combustibles sensor.
Open the catalog to page 1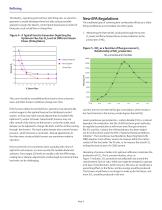
This ideal O2 operating point will vary with firing rate, so a function generator is usually developed from test data using a portable analyzer to assign the ideal O2 control point based upon an index of firing rate, such as fuel flow or charge flow. The traditional goal of achieving best combustion efficiency is often being modified to accommodate two other goals: 1. Minimizing the thermal NOx produced through the burner. O2 levels and flame temperatures are key indicators to the production of NOx. Figure 4 - A Typical Functio Generator Depicting the Optimum Flue Gas O2 Level at Different...
Open the catalog to page 2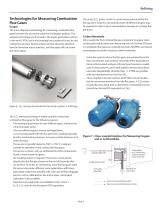
Technologies for Measuring Combustion Flue Gases The in situ ZrO2 probe results in a point measurement within the flue gas duct, however, and several probes of different lengths may be required in order to get a representative average across large flue gas ducts. Oxygen The most ubiquitous technology for measuring combustion flue gases has been the zirconium oxide fuel cell oxygen analyzer. This analyzer technology was first used in the power generation industry in the early 1970s, but the technology has transferred to use for any combustion process. Much has been written about the details...
Open the catalog to page 3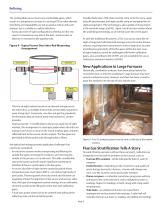
Refining Tunable diode lasers (TDL) have recently come onto the scene, again using IR spectroscopy, and again usually using an averaging line-ofsight arrangement. This technology is also capable of measuring O2 in the overtone range, and NOx. Again, much has been written about the underlying technology, so we will not cover this in this paper. The combustibles sensor burns any combustible gases, which results in a temperature increase in a sensing RTD or other element. Sensitivity and repeatability are not as good as with an infra-red analyzer, but is suitable as a safety indication. -...
Open the catalog to page 4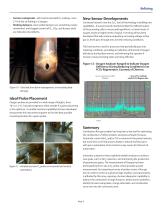
- Furnace casing leaks - will result in elevated O2 readings, since 21 % of the air leaking in is oxygen. - Sticking dampers- stack outlet dampers are sometimes poorly maintained, and sluggish control of O2, COe, and furnace draft are indicative of problems. Continued research into the ZrO2 fuel cell technology is yielding new capabilities. It was previously mentioned that the millivolt output of these sensing cells is inverse and logarithmic, so lower levels of oxygen results in higher levels of signal. A sensing cell has been developed that will continue outputting increasing voltage as...
Open the catalog to page 5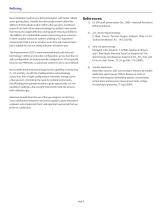
New installation locations are being attempted, with hotter radiant zones gaining favor. Variable insertion probe mounts afford the ability to find the ideal location within a flue gas duct. Continued research into fuel cell sensing technology has yielded a new sensor that measures oxygen deficiency during upset reducing conditions. The addition of a combustibles sensor is becoming more common in close-coupled extractive systems, yielding a “CO equivalent” measurement that is not as sensitive as an infra-red measurement, but is suitable for use as a safety indication of fuel/air ratio. 1)...
Open the catalog to page 6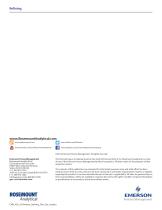
www.RosemountAnalytical.com www.analyticexpert.com ©2013 Emerson Process Management. All rights reserved. Emerson Process Management Rosemount Analytical Inc. Gas Analyzer Service Center 6565P Davis Industrial Parkway Solon, OH 44139 USA T +1 440 914 1261 Toll Free in US and Canada 800 433 6076 F +1 440 914 1262 US Response Center 800 654 7768 gas.csc@emerson.com The Emerson logo is a trademark and service mark of Emerson Electric Co. Rosemount Analytical is a mark of one of the Emerson Process Management family of companies. All other marks are the property of their respective owners. The...
Open the catalog to page 8All Emerson Automation Solutions - ROSEMOUNT catalogs and technical brochures
-
VPS 53 Vapor Pressure Sensor
2 Pages
-
EasyHeat™ XD Cable Kits
2 Pages
-
FRL Accessories
14 Pages
-
TankRadar Pro
32 Pages
-
Rosemount™ 2140 Level Detector
22 Pages
-
Roxar subsea PIG
2 Pages
-
Roxar subsea Sand monitor
2 Pages
-
Roxar subsea CM10K
2 Pages
-
Roxar PTPT15K
2 Pages
-
Rosemount TankRadar OFC
2 Pages
-
SW-300
4 Pages
-
DL8000
12 Pages
-
DeltaV Analyze
8 Pages
-
AMS Machine Works
4 Pages
-
DeltaV Executive Portal
7 Pages
-
1500XA Gas Chromatograph
8 Pages
-
Rosemount 975UR
4 Pages
-
Rosemount 975HR
4 Pages
-
Rosemount 975UF
4 Pages
-
Rosemount 975MR
4 Pages
-
CT5400 Process Gas Analyzer
4 Pages
-
CT2211 Leak Detection System
4 Pages
-
Desalination of Seawater
2 Pages
-
700XA Process Gas Chromatograph
12 Pages
-
SafeGuard Alarm Controller
2 Pages
-
Safety Monitoring
6 Pages
-
AMS Suite
16 Pages
-
Drinking Water Sht 2V2
2 Pages
-
Line Card
2 Pages
-
Drinking Water Industry
16 Pages
-
Explosion Proof Video Camera
2 Pages
-
Net Safety UV Flame Detector
4 Pages
Archived catalogs
-
UV/IRS Flame Detector
4 Pages
-
UVS Flame Detector
4 Pages