
Catalog excerpts
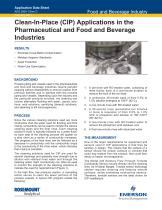
Application Data Sheet ADS 2000-13/rev.C February 2011 Food and Beverage Industry Clean-In-Place (CIP) Applications in the Pharmaceutical and Food and Beverage Industries RESULTS • Eliminate Cross-Batch Contamination • Maintain Hygienic Standards • Asset Protection • Water Use Optimization BACKGROUND Process piping and vessels used in the pharmaceutical and food and beverage industries require periodic cleaning without disassembly to remove residue from previous batches and to sanitize both the process piping and vessels. Depending upon the industry and the particular products involved, the cleaning can involve alternately flushing with water, caustic solutions, acid solutions, sanitizing (bleach) solutions, and steaming to kill microorganisms. PROCESS Since the various cleaning solutions used are more conductive than the water used for flushing and final rinsing, conductivity can be used to monitor the various cleaning steps and the final rinse. Each cleaning solution’s flush is typically followed by a water flush, so each step of the cleaning process will appear on a strip chart as a series of conductivity increases. The progress of the final rinse can be followed as a decrease in conductivity until the conductivity drops to the conductivity of the rinse water, which indicates that rinsing is complete. The cleaning solutions used for CIP are used for several cleanings and gradually lose strength due to dilution with residual rinse water and through the cleaning action itself. Conductivity can often be used to monitor the strength of the cleaning solutions to indicate the need for replenishment (Figure 1). In the high flow, low pressure system, a cascading action serves to clean the lower portions of the process vessels. A typical CIP program entails the following: 1. A pre-rinse with RO-treated water, consisting of three bursts, each of a one-minute duration to remove the bulk of the soil load; 2. A continuous 30-minute wash of from 0.5% to 1.0% alkaline detergent at 180°F (82°C); 3. A one-minute rinse with RO-treated water; 4. A 30-second rinse (sometimes ten minutes or more is requisite) of from 0.5% to 1.0% nitric or phosphoric acid solution at 150°-180°F (65°-82°C); 5. A two-minute rinse with RO-treated water to remove the phosphoric acid residues; and, 6. A final one-minute rinse with deionized water. THE MEASUREMENT One of the major requirements for equipment and sensors used in CIP applications is that they be sanitary in design. This means that the surface of a sensor should not contain contours or crevices that could trap residue from the product, that could then decay or harbor microorganisms. The Model 245 Sanitary Flow-Through Toroidal Conductivity Sensor mounts directly into the cleaning lines via tri-clamp flanges. Toroidal sensor technology seldom requires cleaning and features smooth surfaces, unlike contacting conductivity sensors. Therefore, toroidal sensors are the ideal choice for CIP installations.
Open the catalog to page 1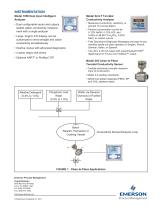
INSTRUMENTATION Model 1056 Dual Input Intelligent Analyzer Model Xmt-T Toroidal Conductivity Analyzer • Dual configurable inputs and outputs enable cation conductivity measurement with a single analyzer • Measures conductivity, resistivity, or percent (%) concentration. • Percent concentration curves for 0-12% NaOH, 0-15% HCl, and 0-25% or 96-99.7% H2SO4, 0-20% NaCl, or custom curves. • Fully Descriptive Diagnostic Messages and easy-to-use interface spells out each operation in English, French, German, Italian, or Spanish. ® • Two wire, 4-20 mA output with superimposed HART digital signal...
Open the catalog to page 2All Emerson Automation Solutions - ROSEMOUNT catalogs and technical brochures
-
VPS 53 Vapor Pressure Sensor
2 Pages
-
EasyHeat™ XD Cable Kits
2 Pages
-
FRL Accessories
14 Pages
-
TankRadar Pro
32 Pages
-
Rosemount™ 2140 Level Detector
22 Pages
-
Roxar subsea PIG
2 Pages
-
Roxar subsea Sand monitor
2 Pages
-
Roxar subsea CM10K
2 Pages
-
Roxar PTPT15K
2 Pages
-
Rosemount TankRadar OFC
2 Pages
-
SW-300
4 Pages
-
DL8000
12 Pages
-
DeltaV Analyze
8 Pages
-
AMS Machine Works
4 Pages
-
DeltaV Executive Portal
7 Pages
-
1500XA Gas Chromatograph
8 Pages
-
Rosemount 975UR
4 Pages
-
Rosemount 975HR
4 Pages
-
Rosemount 975UF
4 Pages
-
Rosemount 975MR
4 Pages
-
CT5400 Process Gas Analyzer
4 Pages
-
CT2211 Leak Detection System
4 Pages
-
Desalination of Seawater
2 Pages
-
700XA Process Gas Chromatograph
12 Pages
-
SafeGuard Alarm Controller
2 Pages
-
Safety Monitoring
6 Pages
-
AMS Suite
16 Pages
-
Drinking Water Sht 2V2
2 Pages
-
Line Card
2 Pages
-
Drinking Water Industry
16 Pages
-
Explosion Proof Video Camera
2 Pages
-
Net Safety UV Flame Detector
4 Pages
Archived catalogs
-
UV/IRS Flame Detector
4 Pages
-
UVS Flame Detector
4 Pages