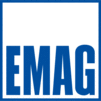

Catalog excerpts
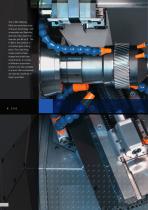
The K 300 Hobbing Machine combines state-of-the-art technology with universality and flexibility, and has a floor plan that requires just 86 sq ft. The K 300 is the solution to numerous gear cutting tasks. The machining range covers wheelshaped and shaft-type components. A number of different automation systems are also available to ensure that workpieces can also be machined in larger quantities.
Open the catalog to page 2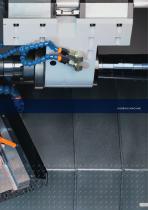
pittf ZZZZZZZZZZZZZZZZZZZZZZZZZZ /llHk> Z Z Z Z Z Z ' Z Z ? ? ? Z ZZZ}}}}?> ^"'/fl 7 7 / AJ£ ^ " c ^ZZZZZZZZZZZZZZZZZZZZZZ ZZX\/'^*ZZZZZZZZZZZZZZZZZZZZZZZ Z Z ZZZZZZZZZZZZZZZZZZZZZZZZ
Open the catalog to page 3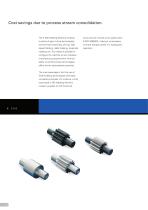
The K 300 Hobbing Machine employs a variety of gear cutting technologies: soft and hard machining, skiving, high speed hobbing, radial hobbing, tangential hobbing, etc. This makes it possible to configure the machine to suit individual manufacturing requirements. And the ability to combine these technologies offers further rationalization potential. The main advantage is that the use of finish-hobbing technologies eliminates complete processes. For instance, a fully automated K 300 Hobbing Machine makes it possible to soft finish-hob pump pinions module 4.0 to quality class 6 (DIN 3960/62),...
Open the catalog to page 4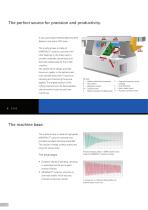
A fully automated Hobbing Machine 300 features nine active CNC axes. The machine base is made of MINERALIT® polymer concrete with roller bearings in the linear axes to provide a statically, dynamically and thermally stable base for the K 300 machine. The closed frame design provides maximum rigidity in the tailstock and main spindle areas even if maximum clamping and machining forces are applied. The angled position of the milling head ensures the best possible chip removal for both dry and wet machining. NC axes: A - Hobbing head swivel movement B - Hob rotation C - Workpiece rotation W -...
Open the catalog to page 6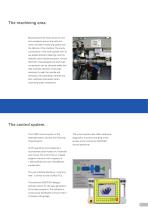
Maintenance-free direct drives for tool and workpiece ensure the best and most consistent machining quality over the lifetime of the machine. The sturdy construction of the work spindle with its pre-loaded precision bearings, and the hydraulic quick-clamping system, ensure that both wheel-shaped and shaft-type components can be clamped safely and help maintain precision. Draw-type clamping through the spindle and clamping with expanding mandrels are both methods that benefit when machining larger workpieces. The control system. The K 300's control system is the latest generation and has the...
Open the catalog to page 7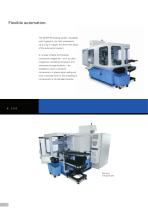
Flexible automation. The KOEPFER loading system, equipped with V-grippers, can hold workpieces up to 5 kg in weight, and forms the basis of the automation system A number of blank and finished component magazines – such as chain magazines, oscillating conveyors, and workpiece storage systems – are available to cover a variety of components. A gravity-type loading rail with a conveyor belt for the unloading of components is the standard solution. Rear view, with guard open
Open the catalog to page 8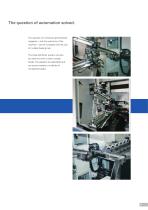
The question of automation solved. The capacity of a universal, gravity-based magazine – and the autonomy of the machine – can be increased with the use of multiple feeding rails. The triple distributor system can also be used as a twin or even a single feeder. The grippers are adjustable and can accommodate a multitude of workpiece lengths.
Open the catalog to page 9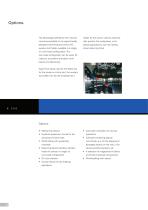
The advantages offered by this machine include accessibility to its ergonomically designed machining area and an NC auxiliary tool holder, available in a single-or a twin-head configuration. The twin-head configuration can be used, for instance, to position and debur workpieces simultaneously. Apart from being used for the deburring for the wheel or cutting tool, the auxiliary tool holder can also be employed as a holder for the sensor used to automatically position the workpieces, or for special applications, such as holding driven deburring tools. Options: • Milling hob arbours •...
Open the catalog to page 10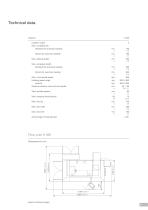
Max. workpiece dia. Standard (for automatic loading) mm 140 Option (for automatic loading) mm 195 Max. workpiece length Standard (for automatic loading) mm 300 Option (for automatic loading) mm 800 Max. work spindle speed rpm 800 Hobbing speed range rpm 200 / 2,500 Distance between work and tool spindle mm 20 - 130 Work spindle capacity mm 60 Max. clamping force tailstock kN 15 Swivel angle of hobbing head ± 45° Subject to technical changes
Open the catalog to page 11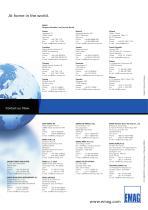
EMAG Gruppen-Vertriebs- und Service GmbH E-mail: info@salach.emag.com E-mail: info@muenchen.emag.com E-mail: info@frankfurt.emag.com E-mail: info@austria.emag.com E-mail: info@koeln.emag.com E-mail: info@leipzig.emag.com Denmark Horsvangen 31 7120 Vejle 0 Denmark Phone: +45 75 854854 E-mail: info@daenemark.emag.com Sweden Glasgatan 19B 73130 Koping Sweden Phone: +46 221 40305 E-mail: info@sweden.emag.com E-mail: j.tomczak@erall.pl Czech Republic Lolkova 766 103 00 Praha 10 - Kolovraty Czech Republic Phone: +420 731 476070 E-mail: mdelis@emag.com Russia ul. Akademika...
Open the catalog to page 12All EMAG GmbH & Co. KG catalogs and technical brochures
-
VL-SERIES
16 Pages
-
Hardening Systems
12 Pages
-
Joining Machines
12 Pages
-
ECM-/PECM-Machines
16 Pages
-
Laser-Welding Machine - ELC 160
20 Pages
-
Gear Hobbing Machine - VLC 200 H
12 Pages
-
Gear Hobbing Machine - K 200
12 Pages
-
Gear Hobbing Machines - K 160
12 Pages
-
Machining Centers - VLC
20 Pages
-
Machining Centers - VM series
16 Pages
-
Grinding Machine - HG 2
8 Pages
-
Grinding Machine - SN 204-208
12 Pages
-
Grinding Machine - VG 110
16 Pages
-
Grinding Machine - SK 204
8 Pages
-
Grinding Machine - PM 310-320
12 Pages
-
Grinding Machine - PM 2
8 Pages
-
Turning Machine - VTC 315 DS
12 Pages
-
Turning Machine - VTC
16 Pages
-
Turning Machine - VTC 100 GT
4 Pages
-
Turning Machine - VT
8 Pages
-
Turning Machine - VSC DUO twin
24 Pages
-
Turning Machines - VSC
20 Pages
-
Turning Machine - VMC
12 Pages
-
Turning Machine - VM
4 Pages
-
Turning Machine - VLC 250
20 Pages
-
Turning Machines - VL
16 Pages
-
Vertical grinding machine VG 110
16 Pages
-
VERTICAL TURNING MACHINES
20 Pages
-
ELC Laser Welding Systems
20 Pages
-
ECM / PECM Technology
20 Pages
-
Product Summary EMAG Group
36 Pages
-
Crankshaft grinder PM2
8 Pages
-
Crankshaft grinder PM310/320
12 Pages