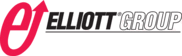

Catalog excerpts
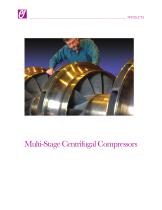
Multi-Stage Centrifugal Compressors
Open the catalog to page 1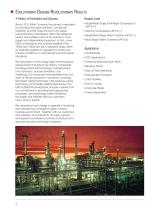
Evolutionary Designs Revolutionary Results A History of Innovation and Success Product Lines Since 1910, Elliott Company has earned a reputation for providing innovative solutions, unmatched expertise, and first-class service to the global turbomachinery marketplace. Elliott has designed, tested, and installed some of the industry’s most rugged and dependable equipment. In fact, some Elliott compressors and turbines installed in the 1940s and 1950s are still in operation today, either as originally supplied or upgraded to handle new process conditions or more stringent environmental...
Open the catalog to page 2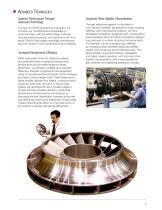
Advanced Technology Superior Performance Through Advanced Technology Through our EDGE development program, we combine our comprehensive knowledge of turbomachinery with the latest design software, manufacturing processes, and machine tools. As a result, Elliott’s multi-stage centrifugal compressors lead the industry in both performance and reliability. Increased Aerodynamic Efficiency Elliott uses state-of-the-art interactive design and prediction tools to optimize aerodynamic performance and increase flange-to-flange efficiencies. Compressor impeller and matched stationary flowpath...
Open the catalog to page 3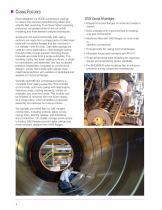
Casing Features Elliott designed our EDGE compressor casings to reduce the required manufacturing steps and simplify field assembly. To achieve higher operating pressures, we applied state-of-the-art solids modeling and finite element analysis techniques. Small and mid-sized horizontally split casing sections are made from a single piece of rolled steel plate with horizontal flanges that are machined— not welded—into the side. Cast steel casings are used for some applications. High-strength casing through-bolts provide superior clamping forces. Endwalls are made from a single solid plate....
Open the catalog to page 4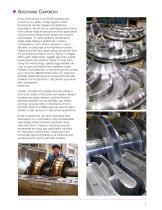
Aerodynamic Components A key achievement of the EDGE development program is our ability to offer superior, threedimensional impeller designs and stationary diaphragms. We do this by maximizing performance over a broad range of pressure and flow applications using the latest aerodynamic design and analysis technologies. To verify predicted performance, single-stage testing is performed in various configurations, such as with vaneless or vaned diffusers, or using high or low tip Mach numbers. Higher and lower flow stage ratings are derived from the prototype test data to form a “family” of...
Open the catalog to page 5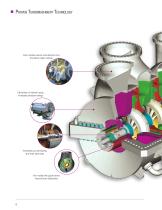
Proven Turbomachinery Technology Cast nozzles reduce manufacture time and allow higher ratings Elimination of dished heads increases pressure ratings Increased journal bearing and shaft seal sizes Non-radial inlet guide vanes improve flow distribution
Open the catalog to page 6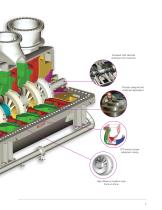
Increased shaft diameter enhances rotor dynamics Precisely designed and machined diaphragms CFD ensures proper sidestream mixing High-efficiency impellers scale frame-to-frame
Open the catalog to page 7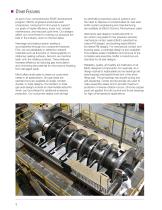
Other Features As part of our comprehensive EDGE development program, Elliott’s engineers examined each compressor component to find ways to support our goals of higher efficiency, lower cost, simpler maintenance, and reduced cycle time. Our designs reflect our commitment to making our products the best in the industry, down to the last detail. Interstage and balance piston sealing is accomplished through two component features. First, we use abradable or deflection-tolerant materials such as fluorosint or nickel-graphite on stationary sealing surfaces. Second, we machine teeth onto the...
Open the catalog to page 8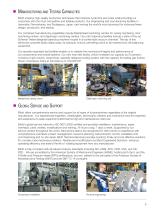
Manufacturing and Testing Capabilities Elliott employs high-quality production techniques that minimize cycle time and costs while providing our customers with the most competitive and reliable products. Our engineering and manufacturing facilities in Jeannette, Pennsylvania, and Sodegaura, Japan, rank among the world’s most advanced for turbomachinery design, production, and testing. Our combined manufacturing capabilities include Masterhead machining centers for casing machining, rotor machining centers, and diaphragm machining centers. Our rotor balancing facilities include...
Open the catalog to page 9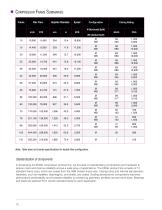
Compressor Frame Summaries Frame Impeller Diameter Configuration M (Horizontal Split) MB (Vertical Split) Casing Rating BARG Note: Table does not include specifications for double flow configuration. Standardization of Components In developing the EDGE compressor product line, we focused on standardizing components and hardware to reduce costs and improve reliability across a wide array of applications. The EDGE product line consists of 15 standard frame sizes, which are scaled from the 38M median frame size. Casing bores and internal aerodynamic hardware, such as impellers, diaphragms, and...
Open the catalog to page 10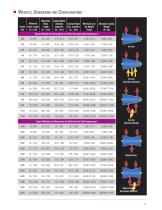
Weights, Dimensions and Configurations Frame Size Minimum Rotor Length (in. / mm) Maximum Rotor Length (in. / mm) Casing Width (includes Casing Height supports) (exc. supports) (in. / mm) (in. / mm) Minimum Casing Weight (lb/kg) Maximum Casing Weight (lb / kg) Typical Weights and Dimensions for Elliott Horizontal Split Compressors* 10M In-Line with Side-Streams In-Line with Iso-Cooling Typical Weights and Dimensions for Elliott Vertical Split Compressors* 10MB Back-to-Back Iso-Cooler Optional
Open the catalog to page 11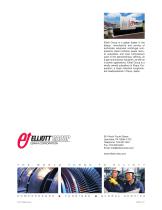
Elliott Group is a global leader in the design, manufacture and service of technically advanced centrifugal compressors, steam turbines, power recover expanders and axial compressors used in the petrochemical, refining, oil & gas and process industries, as well as in power applications. Elliott Group is a wholly owned subsidiary of Ebara Corporation, a major industrial conglomerate headquartered in Tokyo, Japan. 901 North Fourth Street Jeannette, PA 15644-1473 Telephone: 724-527-2811 Fax: 724-600-8442 Email: info@elliott-turbo.com www.elliott-turbo.com
Open the catalog to page 12All Elliott Group catalogs and technical brochures
-
Elliott Tilting-Pad Bearings
4 Pages
-
Steam Turbines and Gas Expanders
12 Pages
-
YR Steam Turbines
8 Pages
-
Elliott Packaging Solutions
8 Pages
Archived catalogs
-
Elliott Bearing Isolators
2 Pages
-
Elliott Digital Governors
2 Pages
-
Elliott Turbine Generators
8 Pages
-
Elliott Steam Turbines
12 Pages
-
Elliott Compressors
12 Pages