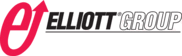

Catalog excerpts
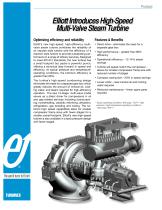
Elliott Introduces High-Speed Multi-Valve Steam Turbine Optimizing efficiency and reliability Features & Benefits Elliott’s new high-speed, high-efficiency multivalve steam turbine combines the reliability of an impulse style turbine with the efficiency of a reaction style turbine to provide outstanding performance in a range of refinery services. Designed to meet API 612 standards, the new turbine has a small footprint but packs a powerful punch, offering a technical leap forward in speed and efficiency. At typical pressure and temperature* operating conditions, the turbine’s efficiency is greater than 80%. Direct drive – eliminates the need for a separate gear box The turbine’s high-speed condensing design eliminates the need for a separate gear box which greatly reduces the amount of mineral oil, cooling water, and steam required for high-efficiency operation. The new 13-stage, multi-valve model serves as a direct driver for compressors in oil and gas-related services including hydrocracking, hydrotreating, catalytic reforming, alkylation, refrigeration, gas boosting and coking. The turbine’s high speed capabilities allow for smaller compressor frame sizes with fewer stages for a smaller overall footprint. Elliott’s new high-speed turbine is also available in a back pressure design with fewer stages. High performance – greater than 80% efficiency Operational efficiency – 12-14% steam savings Turbine will speed match the compressor allows for smaller compressor frame size with reduced number of stages Compact casing size – 20% in space savings Lower costs – less mineral oil and cooling water required Reduced maintenance – fewer spare parts required * Typical operating conditions: 600 psig / 750°F. High pressure / high temperature operating conditions: 1300 psig / 905° F
Open the catalog to page 1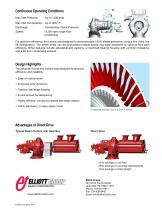
Continuous Operating Conditions Max Inlet Pressure: Condensing / Back Pressure For optimum efficiency, the turbine was designed to accommodate 100% steam admission using a five-valve, bar lift configuration. The steam chest can accommodate multiple nozzle ring base diameters to optimize flow path efficiency. Other features include adjustable end packing, a machined bearing housing with common threading, and a 30-inch condensing exhaust. Design Highlights The aeropath for the new turbine was designed to optimize efficiency and reliability. Ease of maintenance Improved rotor dynamics Titanium...
Open the catalog to page 2All Elliott Group catalogs and technical brochures
-
Elliott Tilting-Pad Bearings
4 Pages
-
Steam Turbines and Gas Expanders
12 Pages
-
YR Steam Turbines
8 Pages
-
Elliott Packaging Solutions
8 Pages
Archived catalogs
-
Elliott Bearing Isolators
2 Pages
-
Elliott Digital Governors
2 Pages
-
Elliott Turbine Generators
8 Pages
-
Elliott Steam Turbines
12 Pages
-
Elliott Compressors
12 Pages