

Catalog excerpts
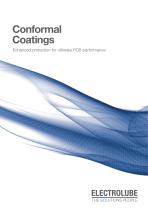
Conformal Coatings Enhanced protection for ultimate PCB performance
Open the catalog to page 1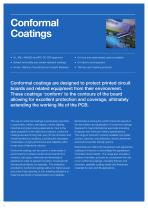
Conformal Coatings • UL, MIL-I-46058C and IPC-CC-830 approved • UV cure and water-based options available • Solvent removable and solvent resistant coatings • UV trace to aid inspection • Acrylic, Silicone, Polyurethane and Hybrid Materials • Thinners and masking products Conformal coatings are designed to protect printed circuit boards and related equipment from their environment. These coatings ‘conform’ to the contours of the board allowing for excellent protection and coverage, ultimately extending the working life of the PCB. The use of conformal coatings is particularly...
Open the catalog to page 2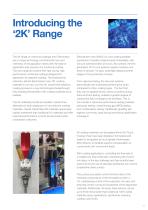
Introducing the ‘2K’ Range The 2K range of conformal coatings from Electrolube are a unique technology combining the two-part chemistry of encapsulation resins with the ease of application and process of a conformal coating. The new range are solvent-free, fast-curing, high performance conformal coatings designed for application by selective coating. The fundamental chemistry behind Electrolube’s new ‘2K’ coating materials is not new, but the 2K, solvent-free selective coating process is a new technological breakthrough, fully enabling the benefits of 2K coating materials to...
Open the catalog to page 3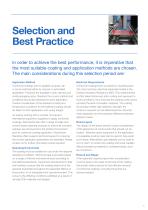
Selection and Best PracticeIn order to achieve the best performance, it is imperative that the most suitable coating and application methods are chosen. The main considerations during this selection period are: Application Method Conformal coatings can be applied via spray, dip or brush methods either by manual or automated application. Products are available in bulk, aerosol and small packaging sizes, therefore the correct method and conditions should be assessed for each application. Careful consideration of the advised humidity and temperature conditions for the selected coating...
Open the catalog to page 5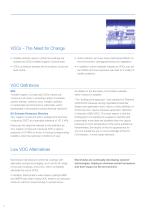
VOCs - The Need for Change • Volatile solvents used in conformal coatings are classed as VOCs (Volatile Organic Compounds). • VOCs contribute towards the formulation of ground level ozone. • Such pollution can have many detrimental effects on the environment, damaging forests and vegetation. • In addition, some materials classed as VOCs can act as irritants and over exposure can lead to a variety of health problems. VOC Definitions EPA ‘Volatile Organic Compounds (VOC) means any compound of carbon, excluding carbon monoxide, carbon dioxide, carbonic acid, metallic carbides or carbonates and...
Open the catalog to page 6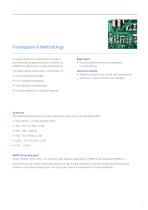
Investigation & Methodology A coating needs to be exposed to a range of environments via appropriate test conditions to establish its performance range and limitations. Basic tests: • Electrical performance and accelerated humidity testing. The ideal coating should offer a combination of: Advanced testing: • Severe conditions such as salt mist, temperature extremes or rapid environmental changes. • Good electrical properties • Low moisture permeability • Good physical characteristics • Excellent adhesion to all board materials Approvals The following Electrolube conformal coatings are...
Open the catalog to page 7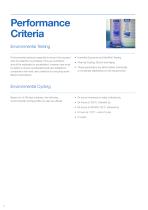
Performance Criteria Environmental Testing Environmental testing is essential to ensure the required level of protection is achieved. End-use conditions should be replicated or accelerated, however care must be taken to ensure accelerated tests are suitable for comparison with end-use conditions by inducing some failure mechanisms: • Humidity Exposure and Salt Mist Testing • Thermal Cycling, Shock and Aging • These parameters are either tested individually or combined depending on the requirements Based on UL746 test methods, the following environmental cycling profile can also be utilised:...
Open the catalog to page 8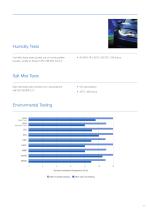
Humidity Tests Humidity tests were carried out on comb pattern boards, similar to those in IPC-TM 650 2.6.3.4: Salt Mist Tests Salt mist tests were carried out in accordance with IEC 60068-2-11: • salt solution 5% • 35°C, 168 hours Environmental Testing DCA Heat Cure DCA Ambient Cure LTC AFA URC UVCL WBP 2K100 2K500 0 2 4 6 8 10 12 Surface Insulation Resistance (10xΩ) After humidity testing after salt mist test
Open the catalog to page 9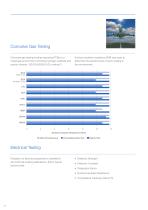
Corrosive Gas Testing Corrosive gas testing involves exposing PCBs to a Surface insulation resistance (SIR) was used to mixed gas environment combing hydrogen sulphide and determine the performance of each coating in sulphur dioxide - BS EN 60068-2-60, method 1. this environment: Surface Insulation Resistance (10xQ) After 2hrs Recovery M Immediately After Test M Before Test Evaluation of electrical properties is essential in all conformal coating applications. Some typical tests include: • Dielectric Strength • Dielectric Constant • Dissipation Factor • Surface Insulation Resistance •...
Open the catalog to page 10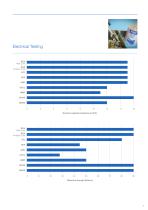
Surface Insulation Resistance (10xQ) Dielectric strength (kV/mm)
Open the catalog to page 11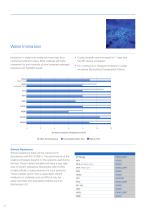
Water Immersion Immersion in water is an extremely harsh test for a conformal coating to pass. Most coatings will resist immersion for short periods of time however prolonged exposure can highlight issues. • Coated boards were immersed for 7 days and the SIR results compared. • For continuous or frequent immersion in water we advise Electrolube Encapsulation Resins DCA ' Heat Cure i DCA Ambient Cure LTC AFA URC UVCL WBP 2K100 i 2K500 Surface Insulation Resistance (10xQ) Immediately After Test Before Test Solvent Resistance Solvent resistance tests can be carried out in accordance with IEC...
Open the catalog to page 12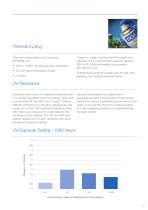
A thermal cycling profile was set up as per IEC 60068-2-14: • -55°C to +125°C, 25 minutes at each temperature • 12°C/min rate of temperature change • 20 cycles Coated tin, copper, aluminium and FR4 panels were subjected to the cycling and then tested for adhesion (BS EN ISO 2409) and flexibility (3mm mandrel -IPC-TM 650 2.4.5.1) All Electrolube conformal coatings pass this test when applied to the substrates described above. Electrolube have carried out weathering resistance tests on a number of available conformal coatings. Tests were in accordance with ISO 4892, Part 3, Cycle 1:...
Open the catalog to page 13All ELECTROLUBE catalogs and technical brochures
-
Thermal Management
20 Pages
-
Maintenance & Service Aids
16 Pages
-
Polyurethane & Epoxy Resins
16 Pages
-
Electrolube Company
8 Pages
Archived catalogs
-
Electrolube Product Selector
8 Pages
-
Product Selector Chart
6 Pages
-
Contact Lubricants
16 Pages
-
Electrolube Product Catalogue
36 Pages
-
Thermal management
6 Pages
-
Automotive lubricants
4 Pages
-
New products
2 Pages