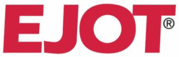
Catalog excerpts
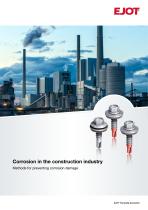
Corrosion in the construction industry Methods for preventing corrosion damage
Open the catalog to page 1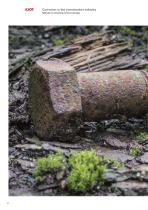
Corrosion in the construction industry Methods for preventing corrosion damage
Open the catalog to page 2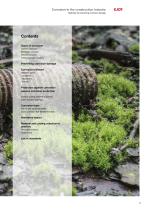
Methods for preventing corrosion damage Types of corrosion Uniform corrosion Bimetallic corrosion Crevice corrosion Stress corrosion cracking Corrosion resistant Stainless steels - Austenitic - Martensitic - Ferritic Surface coating systems in general EJOT standard coatings Corrosion tests Neutral salt-spray test (NSS) Cyclic corrosion test (Kesternich test) Material and coating practice Rural area (exterior) Road tunnel
Open the catalog to page 3
Corrosion in the construction industry Methods for preventing corrosion damage Introduction Corrosion processes cause costs amounting to several billion euros each year. In addition to the financial consequences, numerous dramatic damage events can also be attributed to corrosion. The risk of the occurrence and spread of corrosion can be significantly reduced by selecting suitable active and passive corrosion protection. In particular, the selection of suitable corrosion protection plays an important role when designing screw connections. Not only must the screw material be taken into...
Open the catalog to page 4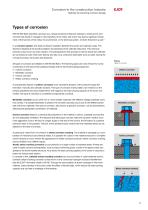
Corrosion in the construction industry Methods for preventing corrosion damage Types of corrosion DIN EN ISO 8044 describes corrosion as a “physicochemical interaction between a metal and its environment that results in changes in the properties of the metal, and which may lead to significant impairment of the function of the metal, the environment, or the technical system, of which these form a part.” In a corrosion system, this leads to electron migration between the anodic and cathodic areas. The electrons released at the anode (oxidation) are absorbed at the cathode (reduction). This...
Open the catalog to page 5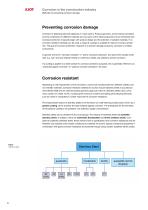
Corrosion in the construction industry Methods for preventing corrosion damage Preventing corrosion damage Corrosion of fastening elements depends on many factors. Product geometry, environmental conditions and the combination of different materials are only some of the influencing factors to be mentioned here. Corrosion protection measures begin with product design and the selection of suitable materials. If no corrosion-resistant materials can be used, a range of coatings is available to improve corrosion protection. The goal of corrosion protection measures is to prevent damage caused by...
Open the catalog to page 6
Methods for preventing corrosion damage Figure Micrographs 500 times magnification The fastening technology industry primarily uses austenitic stainless steels of type A2 (V2A) and A4 (V4A). The steels are characterised by good corrosion resistance in moderately aggressive atmospheres. For especially aggressive atmospheres, stainless steels of type HCR (e.g. 1.4529) should be used, as these have the highest corrosion resistance among stainless steels. The most important materials for screws and the corresponding corrosion resistance classes can be found in Table I. Table II Compatibility...
Open the catalog to page 7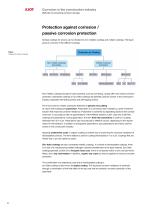
Corrosion in the construction industry Methods for preventing corrosion damage Protection against corrosion / passive corrosion protection Surface coatings for screws can be divided into non-metallic coatings and metallic coatings. The figure gives an overview of the different coatings. Figure Indexing of surface coatings Non-metallic coatings (except for paint systems), such as burnishing, usually offer only limited corrosion protection. Galvanised coatings or zinc flake coatings are generally used for screws in the construction industry, especially self-drilling screws and self-tapping...
Open the catalog to page 8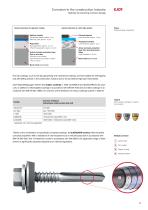
Methods for preventing corrosion damage General structure of a galvanic coating General structure of a zinc flake system Figure Schematic layer composition Optional coating Transparent sealant: approx. 2 pm Black top coat: approx. 10 pm Passivation Blue passivation: approx. 0.1 pm Thick-film passivation: approx. 0.5 pm Actual corrosion protection layer: Zinc or zinc alloy (Zinc/iron or zinc/nickel) Layer thickness according to requirement: 5-20 pm Basic metal (screw/steel) Hot-dip coatings, such as hot-dip galvanising and mechanical coatings, are less suitable for self-tapping and...
Open the catalog to page 9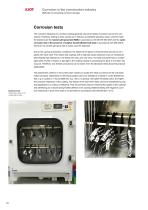
Corrosion in the construction industry Methods for preventing corrosion damage Corrosion tests The corrosion resistance of a surface coating generally cannot be tested in practice due to time constraints. Therefore, testing is often carried out in defined, accelerated laboratory tests. Common tests for fasteners are the neutral salt-spray test (NSS) in accordance with DIN EN ISO 9227 and the cyclic corrosion test in the presence of sulphur dioxide (Kesternich test) in accordance with DIN 50018. However, the neutral salt-spray test is mainly used for fasteners. Due to the varying atmospheric...
Open the catalog to page 10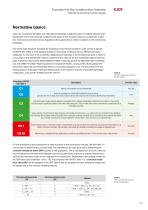
Methods for preventing corrosion damage Normative basics There are a number of European and international standards available to assist in material selection and assessment of the environmental conditions with regard to the corrosion stress to be expected. In addition, there are several other national regulations that supplement or define exceptions to the international standards. One of the most important standards for assessing environmental conditions under corrosive aspects is DIN EN ISO 12944-2. This standard divides environmental conditions into six different corrosivity categories....
Open the catalog to page 11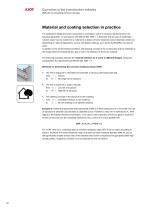
Corrosion in the construction industry Methods for preventing corrosion damage Material and coating selection in practice It is essential to design the screw connection in accordance with the corrosion requirements for the practical application. In accordance with DIN EN ISO 1993-1-4, fasteners that are used in weathered outdoor areas must be made from a material of at least corrosion resistance class II (stainless steels A2). Depending on national regulations, screws with duplex coatings, such as the EJOGUARD, can also be used. In addition to the environmental conditions, the cleaning...
Open the catalog to page 12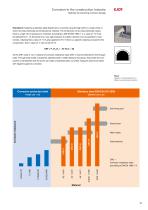
Corrosion in the construction industry Methods for preventing corrosion damage Example II: Fastening a stainless steel attachment in concrete using through bolts in a road tunnel, in which de-icing chemicals are introduced by vehicles. The introduction of de-icing chemicals means there is a high risk of exposure to chlorides. According to DIN EN ISO 1993-1-4, a value of -10 must be selected for F1. At the same time, very high exposure to sulphur dioxide is to be expected in road tunnels, meaning that a value of -10 is also applied for F2. If there is a specific cleaning concept for the...
Open the catalog to page 13All EJOT catalogs and technical brochures
-
Flat Roofing
40 Pages
-
Fasteners for timber construction
114 Pages
-
Highlights 2019
28 Pages
-
Catalogue Building Fasteners
416 Pages
-
EJOT EPPsys DR
1 Pages
-
EJOT DELTAsert
2 Pages
-
EJOT-FDS-AUDI-R8
2 Pages
-
EJOT-EVO-PT
2 Pages
-
EJOT-DELTA-PT
2 Pages
-
EJOT_DELTA_PT_DS
2 Pages