
Catalog excerpts
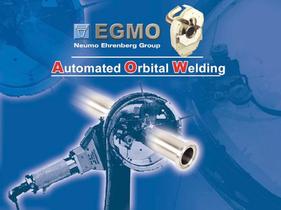
Neumo Ehrenberg Group Automated ©rbital OTeldin
Open the catalog to page 1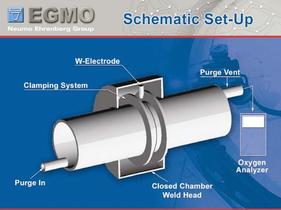
Clamping System Closed Chamber Weld Head
Open the catalog to page 2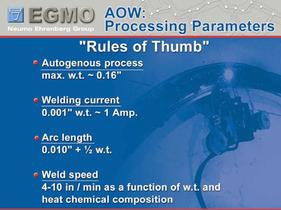
heat chemical composition
Open the catalog to page 3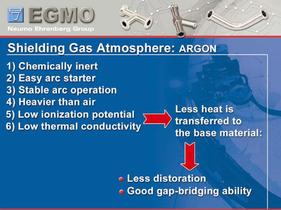
Shielding Gas Atmosphere: ARGON 5) Low ionization potential 5-\ ^ess hea 6) Low thermal conductivity L-/ ferr • Good gap-bridging ability
Open the catalog to page 4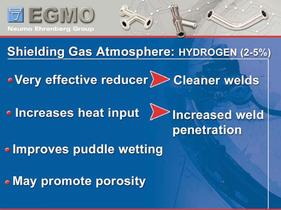
Shielding Gas Atmosphere: HYDROGEN (2-5% "Very effective reducer)^> Cleaner welds • Increases heat input 2> Increased weld Improves puddle wetting
Open the catalog to page 5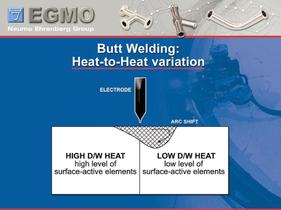
Butt Welding: Heat-to-Heat variation surface-active elements surface-active elements
Open the catalog to page 7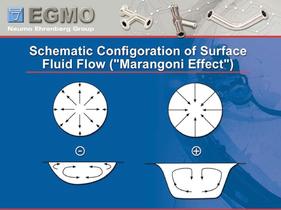
Schematic Configoration of Surface Fluid Flow ("Marangoni Effect")
Open the catalog to page 8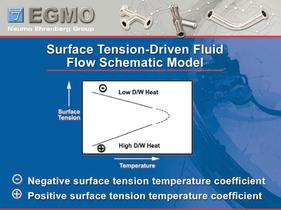
Surface Tension-Driven Fluid Flow Schematic Model © Negative surface tension temperature coefficien ® Positive surface tension temperature coefficient
Open the catalog to page 9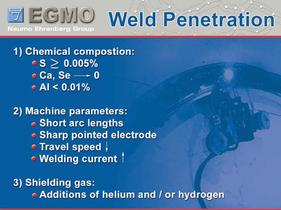
Sharp pointed electrode Additions of helium and / or hydrogen
Open the catalog to page 10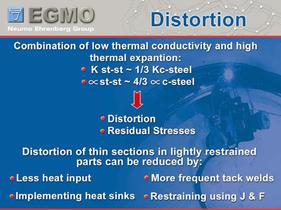
Combination of low thermal conductivity and high thermal expantion: • Residual Stresses Distortion of thin sections in lightly restrai Less heat input r More frequent tack welds - Implementing heat sinks Restraining using J & F
Open the catalog to page 11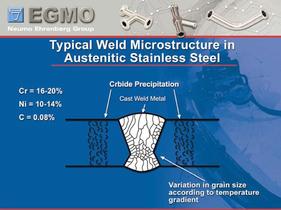
Typical Weld Microstructure in Austenitic Stainless Steel Crbide Precipitation Cast Weld Metal ariation in grain size
Open the catalog to page 15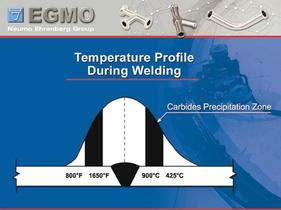
Temperature ProfiI During Welding Carbides Precipitation
Open the catalog to page 16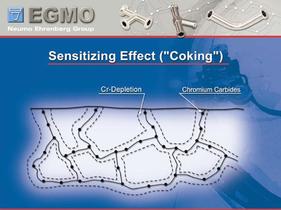
Sensitizing Effect ("Coking") Chromium Carbides
Open the catalog to page 17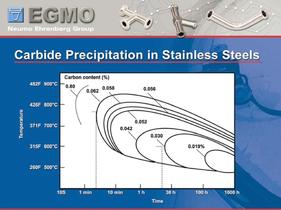
Carbide Precipitation in Stainless Steels
Open the catalog to page 18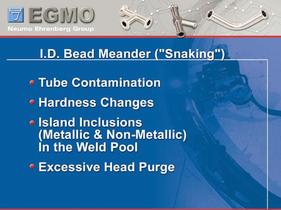
I.D. Bead Meander ("Snaking") Tube Contamination Hardness Changes Island Inclusions (Metallic & Non-Metallic) Excessive Head Purge
Open the catalog to page 20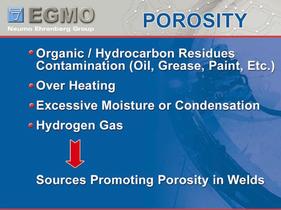
• Organic / Hydrocarbon Residues Contamination (Oil, Grease, Paint, Etc.) r Excessive Moisture or Condensation Sources Promoting Porosity in Welds
Open the catalog to page 21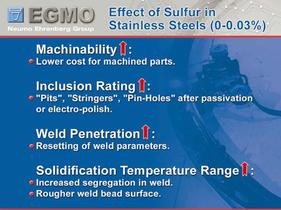
r Lower cost for machined parts. Inclusion Rating : «■ "Pits", "Stringers", "Pin-Holes" after passivation Resetting of weld parameters. Solidification Temperature Range Increased segregation in weld. Rouoher weld bead surface.
Open the catalog to page 22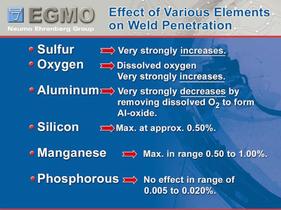
(?. c) Effect of Various Elements OJns^ on Weld Penetration • Sulfur s=> Very strongly increases. •Oxygen s=> Dissolved oxygen -^^B Very strongly increases. m r Aluminums Very strongly decreases by removing dissolved 02 to form r Silicon s=>Max. at approx. 0.50%. PhOSphorOUS No effect in range of
Open the catalog to page 23All EGMO LTD. catalogs and technical brochures
-
TMX Control Head
2 Pages
-
ESV CATALOG
4 Pages
-
MAXCLEAN
2 Pages
-
PVE LEAFLET
2 Pages
-
TWISTMAX CATALOG
17 Pages
-
SOLAR CATALOG
2 Pages
-
SCIMAX CATALOG
36 Pages
-
MAXPURE CATALOG
52 Pages
-
EGMO GENERAL LEAFLET
2 Pages
-
Mobile CIP
8 Pages
-
Butterfly valve
12 Pages
-
Sanitary Equipment Line
51 Pages
-
CF Flanges
36 Pages
-
ASA Fanges
16 Pages
-
ISO Fanges
16 Pages
-
Weld Fittings
16 Pages
-
Surface characterizations
12 Pages
-
Semi-Conductor industry
23 Pages
-
stainless steel
13 Pages
-
Corrosion in stainless steel
8 Pages
-
AL-6XN
2 Pages
-
880 Elbow
2 Pages
-
ASME BPE
11 Pages
-
Flanges
20 Pages
-
Vessels & Reactors
6 Pages
-
Sampling Valves
4 Pages
-
Single Seat
2 Pages
-
Butterfly & Ball - Midi
3 Pages
-
Butterfly & Ball - Mini
4 Pages