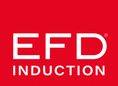

Catalog excerpts
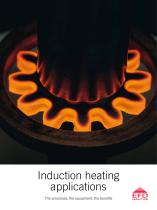
Induction heating applications The processes, the equipment, the benefits
Open the catalog to page 1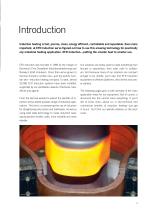
Introduction Induction heating is fast, precise, clean, energy efficient, controllable and repeatable. Even more important, at EFD Induction we’ve figured out how to use this amazing technology for practically any industrial heating application. EFD Induction—putting the smarter heat to smarter use. EFD Induction was founded in 1996 by the merger of Germany’s Fritz Düsseldorf Induktionserwärmung and Norway’s ELVA Induksjon. Since then we’ve grown to become Europe’s number one—and the world’s number two—induction heating company. To date, almost 20,000 EFD Induction systems have been...
Open the catalog to page 3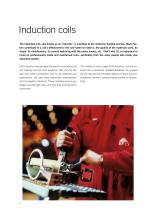
Induction coils The induction coil, also known as an ‘inductor’, is essential to the induction heating process. Many factors contribute to a coil’s effectiveness: the care taken to make it, the quality of the materials used, its shape, its maintenance, its correct matching with the power source, etc. That’s why it’s so important to insist on professionally made and maintained coils—preferably from the same people who made your induction system. EFD Induction has perhaps the world’s most advanced coil making and coil care programs. We not only design and make customized coils for all...
Open the catalog to page 4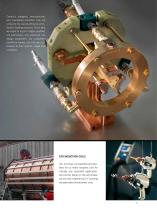
Correctly designed, manufactured and maintained induction coils are critical to the overall efficiency of induction heating solutions. That’s why we invest so much in highly qualified coil technicians and advanced coil design equipment. Our customers benefit by having coils that are customized to their specific needs and conditions. EFD INDUCTION COILS Our in-house coil expertise and facilities let us make bespoke coils for virtually any specialist application. And as the photo on the left shows, we are also experienced in building exceptionally dimensioned coils.
Open the catalog to page 5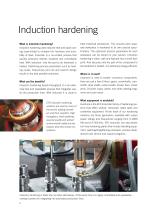
Induction hardening What is induction hardening? Induction hardening uses induced heat and rapid cooling (quenching) to increase the hardness and durability of steel. Induction is a no-contact process that quickly produces intense, localized and controllable heat. With induction, only the part to be hardened is heated. Optimizing process parameters such as heating cycles, frequencies and coil and quench design results in the best possible outcomes. What are the benefits? Induction hardening boosts throughput. It is an extremely fast and repeatable process that integrates easily into...
Open the catalog to page 6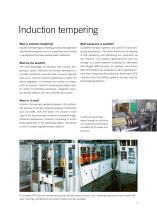
Induction tempering What is induction tempering? What equipment is available? Induction tempering is a heating process that optimizes mechanical properties such as toughness and ductility in workpieces that have already been hardened. Complete HardLine systems are ideal for many tempering applications. The chief benefit of such systems is that hardening and tempering are performed by one machine. This delivers significant time and cost savings in a small footprint compared to alternative technologies. With furnaces, for example, one furnace often first hardens the workpieces, with a...
Open the catalog to page 7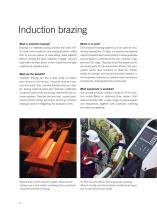
Induction brazing What is induction brazing? Brazing is a materials-joining process that uses a filler metal (and usually an anti-oxidizing solvent called flux) to join two pieces of close-fitting metal together without melting the base materials. Instead, induced heat melts the filler, which is then drawn into the base materials by capillary action. EFD Induction brazing systems can be used for virtually any brazing task. To date, our systems are typically used in the electrotechnical industry to braze generator and transfomer components like bars, strands, rings, wires and SC-rings. They...
Open the catalog to page 8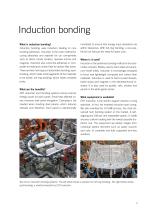
Induction bonding What is induction bonding? Induction bonding uses induction heating to cure bonding adhesives. Induction is the main method for curing adhesives and sealants for car components such as doors, hoods, fenders, rearview mirrors and magnets. Induction also cures the adhesives in composite-to-metal and carbon fiber-to-carbon fiber joints. There are two main types of automotive bonding: spotbonding, which heats small segments of the materials to be joined; full-ring bonding, which heats complete joints. What are the benefits? EFD Induction spot bonding systems ensure precise...
Open the catalog to page 9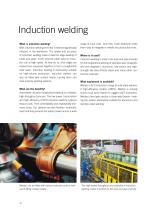
Induction welding What is induction welding? With induction welding the heat is electromagnetically induced in the workpiece. The speed and accuracy of induction welding make it ideal for edge welding of tubes and pipes. In this process, pipes pass an induction coil at high speed. As they do so, their edges are heated then squeezed together to form a longitudinal weld seam. Induction welding is particularly suitable for high-volume production. Induction welders can also be fitted with contact heads, turning them into dual purpose welding systems. What are the benefits? Automated induction...
Open the catalog to page 10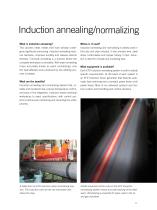
Induction annealing/normalizing What is induction annealing? This process heats metals that have already undergone significant processing. Induction annealing reduces hardness, improves ductility and relieves internal stresses. Full-body annealing is a process where the complete workpiece is annealed. With seam annealing (more accurately known as seam normalizing), only the heat-affected zone produced by the welding process is treated. Induction annealing and normalizing is widely used in the tube and pipe industry. It also anneals wire, steel strips, knife blades and copper tubing. In...
Open the catalog to page 11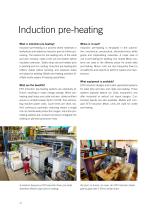
Induction pre-heating What is induction pre-heating? Induction pre-heating is a process where materials or workpieces are heated by induction prior to further processing. The reasons for pre-heating vary. In the cable and wire industry, cable cores are pre-heated before insulation extrusion. Steels strips are pre-heated prior to pickling and zinc coating. Induction pre-heating also softens metals before bending, and prepares tubes and pipes for welding. Mobile pre-heating solutions facilitate onsite repairs of bearing assemblies. Induction pre-heating is employed in the automotive,...
Open the catalog to page 12All EFD Induction Group catalogs and technical brochures
-
HARDLINE CP 600
2 Pages
-
Crankshaft hardening
4 Pages
-
Hardline CIHM-C
2 Pages
-
Coating Removal System
8 Pages
-
Seam normalizing
4 Pages
-
Induction coils
8 Pages
-
TERAC 25/40
2 Pages
-
HARDLINE VL 1000
2 Pages
-
Energy Management System
4 Pages
-
EFD Induction
22 Pages
-
Weldac
5 Pages
-
Sinac
5 Pages
-
HardLine
6 Pages