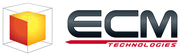
Group: ECM Group

Catalog excerpts
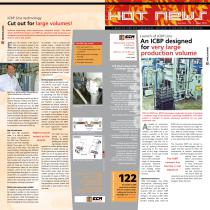
Quar tely – no. 7 – June 2009 a Optimum sequencing, easier maintenance, integrated design… The finest details of ECM Technologies’ new ICBP Line, intended for high production, are designed to meet the productivity requirements of equipment manufacturers. Shall we take a look inside? two in the carburizing module and five in the final diffusion module (see figure 1). "This is just an example, but by reaching 1,670 kg of parts per hour, the ICBP Line has the highest productivity level on the low-pressure carburizing market," enthuses Gérard Tissot, ECM Technologies’ Technical Director. By way of comparison, it is worth noting that ECM Technologies’ modular ICBPs treat between 1,000 and 1,200 kg of parts per hour depending on the procedure, with loads of 350 kg. Identical-phase procedures The ICBP Line can be used to treat most of the usual types of part, particularly for gears. Industrial tests carried out by ECM Technologies have shown that the quality of carburizing and level of reproducibility are comparable to those achieved with modular ICBPs. As the machine is sequenced, the procedures are simple, involving a succession of identical carburizing and diffusion phases. It is simply a matter of adjusting the respective lengths of the phases to vary the enrichment profiles. "It is even possible to change the treatment without shutting down the ICBP, provided that two procedures have the same sequence!" explains Gérard Tissot. Hot and cold areas With such high production Highest hourly The ICBP Line thus rates, it is vital to protect output on the retains a certain the various components of flexibility. By adding the ICBP Line. Thermal promarket heating and carburiztection is the first necessity. ing modules it will be Gérard Tissot goes on: "All the mechapossible to achieve greater depths nisms are in cold areas." The three hot of treatment or larger volumes. As areas (heating, carburizing and diffusion far as quenching is concerned, the modules), which have graphite heating elICBP Line can be equipped with an ements, are operating constantly at temoil quenching module or gas quenchperatures in excess of 900°C. They are ing module, as required. It should fully insulated and closed at each end by be noted in passing that the design hinged graphite felt doors that open only of the gas quenching module was when the loads are moving. As a result, optimized by simulation and that its the temperature inside the four transfer efficiency is enhanced by the fact modules, where all the drive functions that smaller loads make for more are concentrated (see figure 2), never exuniform cooling. In the future, it will ceeds 80°C. To complete the protection, be possible to equip an ICBP Line a powerful suction evacuation system sitwith both quenching systems: ECM uated in the carburizing module recovers Technologies is already working on a the acetylene cracking by-products. two-directional transfer pusher that will be able to steer loads to one or Motors and sensors kept outside! the other. In addition to being thermally protected, the pushers’ position on the machine is also a considerable help when it comes to maintenance. ECM Technologies has pursued this concept to its logical conclusion by installing as many sensitive parts carb urizing • ne load every 9 to O 12 minutes depending on the procedure ICBP Line: Cut out for large volumes! • 50 kg per load, excluding 2 fixturing back page An ICBP designed for very large production volume • Acetylene carburizing • il or gas quenching O Full steam ahead after a strategic change in direction ECM Technologies was created on 24 December 2008 following the takeover of the assets, patents and goodwill of ECM and ECM Infrafours and acquisition of the American and Chinese subsidiaries. Our company has retained all the strengths of the ECM group: first-rate personnel, a diversified, innovative product range, and a global leader’s position on the low-pressure carburizing market. We are the only group in the sector with the structure required to ride out the current economic downturn. The pusher motors are accessible from outside the ICBP Line. Our strategy will focus on three areas: HEATING 8 loads • developing leading-edge installations and processes in the fields of vacuum thermochemical treatments, vacuum furnaces and crystallization furnaces for the photovoltaic industry; Quenching Unloading Fig 1 : Overall view of an ICBP Line. Loading module Unloading end quenching cell Fig 2 : 3D view of transfer pusher. • serving our customers, who are all renowned in their respective fields; • setting up new sites and developing our existing ones, to stay close to our markets. I would like to thank our customers, suppliers and partners for placing their trust in us and enabling us to embrace 2009 with confidence. Laurent Pelissier, CEO the number of ICBPs connected to our hotline from our customers’ plants, making sure they have the advantage of an immediate analysis by our specialists. Low-pressure carburizing, the productivity of a pusher furnace. With the ICBP Line, ECM Technologies inaugurates its policy of providing a complete range of low-pressure carburizing installations. This latest product is intended to provide continuous treatment for very large production runs. ICBP Line is a continuous low-pressure vailable for demonstracarburizing line suited to very large voltion at ECM Technoloumes and highly repetitive production gies’ facility in Grenoble runs. With its simple design, it offers (France), the ICBP Line is crehigh-performance, high-quality vacuum ating a sensation in the heat heat treatment and gas quenching for treatment field. With this lata very reasonable investment cost. est technology innovation, ECM Technologies has met the reThe innovative ICBP Line concept requirements of intensive produclies on a set of technologies that no tion by applying low-pressure longer hold any secrets for ECM: the carburizing to the heat treatmechanisms of vacuum pusher-type ment of very large, continuous furnaces – ECM Technologies has been production. A clear sign of ECM making them since Technologies’ inten1964 –, low-pressure tion to offer a complete The ICBP carburizing – used range of low-pressure concept has in mass production carburizing solutions since 1992 and confor all types of indusbecome a real stantly optimized –, trial strategy based signature and gas quenching. on its signature ICBP "All recent ICBP deconcept. velopments are to be found in the ICBP Line" stresses Alfred Rallo, ECM TechOptimised investment nologies’ Sales Director. ECM Technologies now offers low-pressure carburizing equipment for small companies, with the ICBP-Duo, and for large industries, with the "classic" ICBP or the ICBP Line. In the latter category, the classic ICBP offers greater flexibility with its independent heating cells, while the High-precision carburizing at Turbomeca inside pages The ICBP Line in brief The figure for this quarter Gérard Tissot, ECM Technologies’ Technical Director: "All the mechanisms are in cold areas!" as possible – and in particular the pusher motors… outside the ICBP! This means that maintenance personnel have only a short time to wait and maintenance operations can be performed very quickly. The many position sensors that help to synchronise load movements are also easily accessible: "We chose inductive sensors that are screwed on to the machine walls from the outside," says Gérard Tissot. Result: a faulty probe can be replaced “cold” in just a few seconds! very nine minutes, a new load of 250 kg of parts is placed in the ICBP Line loading module. At the other end of the line, as in all pusher-type furnaces, a carburized load is delivered from the quenching module. In between, 15 loads are in the process of being treated – eight in the heating module,
Open the catalog to page 1All ECM Technologies catalogs and technical brochures
-
Vacuum furnace-CRISTAL
2 Pages
-
ICBP ECO
2 Pages
-
Carbonitriding lines
2 Pages
-
NUCLEAR APPLICATIONS
2 Pages
-
File Vacuum furnace
2 Pages
-
Induction furnaces - VIM
2 Pages