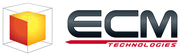
Group: ECM Group

Catalog excerpts
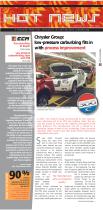
Quar terly no. 1 - July 2006 A MAGAZINE FROM ECM, SPECIALIST IN LOW-PRESSURE CARBURIZING inside pages Chrysler Group: low-pressure carburizing fits in with process improvement Low-pressure carbonitriding: tests with PSA back page I heartily thank Chrysler Group and Delphi for being so readily available to our editorial team for this first edition, and also PSA, for its cooperation during the carbonitriding tests. The productivity of our installations is continuously improving: between 20 and 33% in five years depending on the application. But this dynamic impetus would not be possible without your trust: the real measure of our performance is the quality of your components and the productivity of your processes. Our installations are much more than simple products: each of them provides a technological solution to your expectations. A solution that we want to define with you by participating at the earliest possible stage in the design of your future programs. Laurent Combaz ECM, Chief Executive Officer of ECM's low-pressure installations in service in Europe are equipped with gas quench. In North America, gas quench is fitted to 80% of ECM's installations. In Japan, oil quenching still prevails, on more than 80% of ECM installations. Photo: DaimlerChrysler More than 15% of new casehardening programs are today opting for low-pressure carburizing and three-quarters of the installations currently in service throughout the world are supplied by ECM. We feel that such experience should be shared with you and we are therefore pleased to be able to invite you, four times a year, to read the columns of this magazine. Chrysler 300C: several transmission components carburized under vacuum In 2003, the Chrysler Group commissioned its first low-pressure carburizing unit at its ITP2 site (Indiana, USA). The process has proven its worth by the reliability and quality of the parts produced. The manufacturer has set a course for a controlled change in favor of this technology. Today, the plant carburizes under vacuum more than three million transmission components every year. From September 2005, the process ince 2003, Chr ysler was extended to cover the production Group has gone from of pinion gears for the W5A580 transzero to more than three mission. A second carburizing unit has million parts treated per year since been installed. Quality targets using the low-pressure carburizhave been reached and the car manuing process in its Indiana facturer has noted a 20% increase in Transmission Plant II (ITP2) in productivity. Kokomo, Indiana. This sudden growth is the result of a policy of Equipment reliability continuous improvement of the At the outset, Chrysler Group had fixed manufacturing processes at a realistic targets, in line with its indussite that, last year alone, protrial logic. In the beginning, the goal duced 400,000 W5A580 autowas to improve quality for the long run matic transmissions designed for as benchmarks demonstrated potenDodge, Chrysler or Jeep® vehitial to increase surface cles. After a The manufacturer quality and decrease disseries of test campaigns, underaims at long-term tor tion thanks to gas quenching. For the first taken between quality installation, the financial 2001 and 2003, target was to break even, as neither Chr ysler Group confirmed an actual uptime nor maintenance cost improvement in quality of parts. data were available. However, due to The ITP2 plant acquired its first its policy of continuous reevaluation of low-pressure unit and launched processes, the manufacturer was able this carburizing process on the to confirm the reliability of the ICBP in input/output shaft production line. Continued next page >
Open the catalog to page 1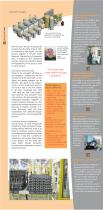
Continued from page 1 ECM Japan celebrates its first birthday A six-cell ICBP with gas quenching: 20% productivity increase in carburizing the ITP2 plant. The gain in productivity resulting from this factor alone is 10%, as estimated by Dave Kopka, tool and process engineer in Chrysler Group Advanced Manufacturing Engineering team. In addition to this productivity increase, enhanced component quality and repeatability of the process came as extra bonuses. Consistency within the load Thanks to the case-depth uniformity on the component – between the root and the pitch line of the pinion...
Open the catalog to page 2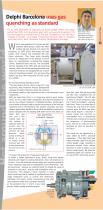
For its new generation of high-pressure diesel pumps, Delphi has equipped all the ICBPs in its Barcelona plant with gas quenching systems. The tier-one supplier is currently one of the rare companies to use two technologies in tandem – oil and gas. Prospective analysis, after an interview with Raul Perez, Heat Treatment Process Development Manager. Raul Perez, Heat Treatment Process Development Manager: "The main reason for this choice is the cost" ith its new generation of common rail highpressure diesel pumps, Delphi has taken another big step forward in its search for excellence. Its...
Open the catalog to page 3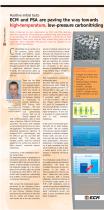
ECM and PSA are paving the way towards high-temperature, low-pressure carbonitriding Tests conducted on real components by ECM and PSA demonstrate the superiority of low-pressure carbonitriding over atmospheric technologies for all standard applications. Carried out at high temperature, these tests indicate that productivity gains can be expected. Once validated, the process could be adapted to all ECM's ICBP installations. With success: the metallurgical analysis, performed by the laboratory Etudes Métallurgiques et Traitement Thermique de Lyon (France), indicated nitrogen enrichment over...
Open the catalog to page 4All ECM Technologies catalogs and technical brochures
-
Vacuum furnace-CRISTAL
2 Pages
-
ICBP ECO
2 Pages
-
Carbonitriding lines
2 Pages
-
NUCLEAR APPLICATIONS
2 Pages
-
File Vacuum furnace
2 Pages
-
Induction furnaces - VIM
2 Pages