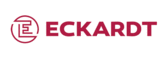
Catalog excerpts
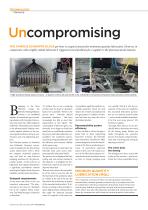
TECHNOLOGY Stamping THE FAMOUS SCHNAPPS GLASS per hour is a typical amount for minimum quantity lubrication. However, in conjunction with a highly volatile lubricant it triggered several problems for a supplier to the pharmaceutical industry. 1 High-precision dosing systems ensure 2 Quality is the be all and end all as far as Eckardt is concerned; exhaustive tests precede commissioning. elonging to the Swiss Dätwyler Group, the Dätwyler Sealing Solutions division is an established supplier of customized caps and seal ing solutions with 16 production loca tions and more than 5600 employees worldwide. Their products are utilized in the pharmaceutical industry, auto motive supplier industry, in the con sumer goods market as well as in con struction and civil engineering pro jects. The Dätwyler location in Ittersbach near Karlsruhe, Germany, concen trates on products for the first of those sectors named above. This is where the company exclusively produces caps and seals on state-of-the-art stamping machines for the pharma ceutical market. As the tools run at high speed, their regular lubrication is a significant precondition towards achieving the highest levels of process reliability and minimum downtimes. Stringent requirements At the same time, there is one very important requirement: “The phar maceutical seal must be absolutely free of oil”, explains Stefan Leicht weis, Tool Shop Manager at Dätwyler in Ittersbach. “To achieve this we use a vanishing oil that must be dosed in quantities kept as low as possible.” However, the process used – Dätwyler utilized pneumatic nebulizers – had been increasingly less able to meet their requirements in this regard. “The consumption of lubricant grew con tinuously, so we began to think hard about how we could further optimize the process and reduce lubricant con sumption”, Mr. Leichtweis summa rizes the growing dissatisfaction with the efficiency and economic viability of this process step. On the lookout for an alternative the Dätwyler team came across mini mum quantity lubrication (MQL). The process can be deployed for both cutting and non-cutting metalwork. The objective is to dissipate the fric tional heat created at the tools and to improve lubrication. That not only reduces the susceptibil ity of the tools to wear, but also the thermal load of the production plant as a whole; at the end of the day that also affects the uniformity of quality of the manufactured products. To lu bricate according to this principle re quires high-precision dosing systems that apply the lubricant precisely where it is required. At the same time reprint from bbr October 2017 www.bbr.de it is possible to apply the smallest con ceivable quantities, which not only reduces the overall consumption but also guarantees no residues of lubri cant find their way from the tool to the finished product. Reproducibility pushes efficiency As they are able to call on the appro priate level of plant engineering know-how in-house, the Dätwyler team themselves installed the MQL system designed to meet the require ments of the diverse production pro cesses. “A particularly important aspect in this case is the repeat accu racy of the lubrication patterns, be cause the diversity of products means we have to change stamping tools very quickly. Which is why the pa rameters of the tools are coupled to the associated lubrication parame ters via our machine control system – and are made available immediate ly for the next setup process,” Mr. Leichtweis explains. “Amongst other aspects, we are spe cifically able to determine how much oil the dosing pump delivers per stroke throughout the respective process. Previously, we had the labo rious task of making this setting by adjusting a setscrew.” The valve does the dosing The dosing process has a central role to play in this scenario – and in par ticular the valves responsible for ap MINIMUM QUANTITY LUBRICATION (MQL) MQL requires a lot less oil than normal quantity lubrication; nevertheless, despite greater productivity it increases tool life in comparison with dry production processes many times over. And it goes without saying that not only are the procurement costs lower, but also the disposal, storage and cleaning
Open the catalog to page 1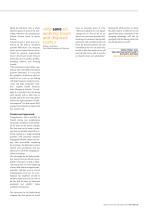
plying the lubricant. This is where Dätwyler places its trust in the tech nology offered by the manufacturer Eckardt Systems based in nearby Bretten. Eckardt focuses a great deal of at tention on the field of minimum quantity lubrication. The company stocks special valves that can be in stalled for quantity requirements from 2–40 mm3 per stroke. They are primarily used to produce profiles, stamping contacts and forming threads. “The maintenance aspect plays a sig nificant role in the field of minimum quantity lubrication. It is true that the quantities of lubricant used are small, but as a...
Open the catalog to page 2All Eckardt Umformtechnik GmbH Systeme für die Umformtechnik catalogs and technical brochures
-
About us
22 Pages
-
Precision lubrication
5 Pages
-
product-brochure_Eckardt
4 Pages