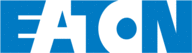

Eaton Torque Limiting Coupling Installation, Operation and Maintenance Manual Airflex® Product Line
20Pages
Catalog excerpts
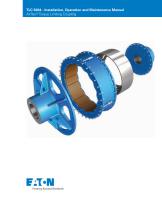
TLC 5004 - Installation, Operation and Maintenance Manual Airflex® Torque Limiting Coupling F;T>N Powering Business Worldwide
Open the catalog to page 1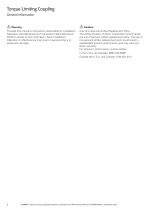
Torque Limiting Coupling General information Forward this manual to the person responsible for Installation, Operation and Maintenance of the product described herein. Without access to this information, faulty Installation, Operation or Maintenance may result in personal injury or equipment damage. Use Only Genuine Airflex Replacement Parts. The Airflex Division of Eaton Corporation recommends the use of genuine Airflex replacement parts. The use of non-genuine Airflex replacement parts could result in substandard product performance, and may void your Eaton warranty. For optimum...
Open the catalog to page 2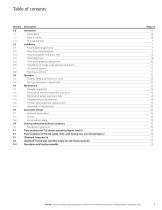
2.3 Mounting spider and drum hub8_ 2.5 Axial locking device adjustment 10 2.6 Installation of single wide element and drum 11 3.2 Control component adjustment 12 4.2 Removal of element assembly and drum 14 4.3 Removal of spider and drum hub 14 4.5 Friction shoe assembly replacement 14 5.0 Spare parts storage 15 6.0 Ordering information/technical assistance 15 7.1 Parts breakdown of TLC element assemblies figures 1 and 10 16 8.1 Parts breakdown of TLC hub, spider, drum, axial locking assy. and rotorseal figure 2 16 9.2 (Standard) Friction shoe assembly, torque bar and release spring kit 17...
Open the catalog to page 3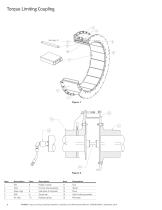
Torque Limiting Coupling Item Description Item Description Item Description 1 Rim 2 Tube 3 Snap rings 4 QRV 5 Air tube 11 Hub 12 Spider 13 Drum 14 Axial locking assembly 15 Rotorseal Rubber washer Friction shoe assembly Side plate (2 required) Torque bar Release spring EATON Torque Limiting Coupling Installation, Operation and Maintenance Manual E-MEQD-II002-E September 2015
Open the catalog to page 4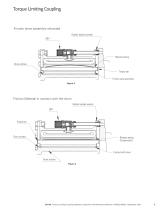
Torque Limiting Coupling Friction shoe assembly retracted Rubber backed washer QRV Release spring Drum surface Torque bar Friction shoe assembly Figure 3 Friction Material in contact with the drum Rubber backed washer QRV Drum surface Release spring (Compressed) Contact with drum Drum surface Figure 4 EATON Torque Limiting Coupling Installation, Operation and Maintenance Manual E-MEQD-II002-E September 2015
Open the catalog to page 5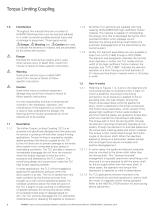
1.0 Introduction Throughout this manual there are a number of HAZARD Warnings that must be read and adhered to in order to prevent possible personal injury and/ or damage to equipment. Three signal words Danger, A Warning and A Caution are used to indicate the severity of a hazard, and are preceded by the safety alert symbol A Danger Denotes the most serious hazard, and is used when serious injury or death WILL result from misuse or failure to follow specific instructions. A Warning Used when serious injury or death MAY result from misuse or failure to follow specific instructions. A...
Open the catalog to page 6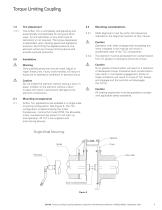
1.3.1 The Airflex TLC is completely self-adjusting and automatically compensates for lining and drum wear. Air line lubrication or any other type of lubrication is not required. The torque developed is dependent upon rotating speed and applied air pressure. By limiting the applied pressure, the element will act as a torque limiting device and provide overload protection. Only qualified personnel should install, adjust or repair these units. Faulty workmanship will result in exposure to hazardous conditions or personal injury. A Caution Do not inflate the element without having a drum in...
Open the catalog to page 7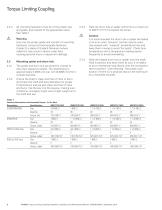
Heat the drum hub or spider uniformly to a maximum of 250°F (121°C) to expand the bores. Caution It is recommended the drum hub or spider be heated in oil or an oven; however, torches may be used. Use several with "rosebud” (broad-flame) tips and keep them moving to avoid "hot spots". Check bore temperature with a temperature reading device frequently to avoid overheating. Slide the heated drum hub or spider onto the shaft. Hold in position and allow them to cool. It is helpful to put a mechanical stop device onto the component face to prevent "over-shooting” the proper axial location if...
Open the catalog to page 8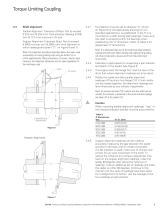
Torque Limiting Coupling Parallel Alignment Tolerance (Offset): Not to exceed 0.010 inch (0.254 mm) Total Indicator Reading (0.005 inch (0.127 mm) maximum off- set). Angular Alignment Tolerance (Gap): Not to exceed 0.0005 inch per inch (0.0005 mm/ mm) diameter at which readings are taken (“D” on Figure 6 and 7). Note: The alignment procedure described below has been used successfully on many grinding mills using an Airflex TLC or clutch application(s). Other procedures, of course, may be used; however, the alignment tolerances are the same regardless of the technique used. Bracket Dial...
Open the catalog to page 9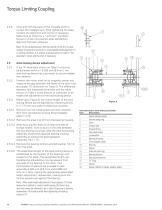
Item description axial locking assembly Item Description 1 Spider adapter plate 2 Internal snap ring 9 Drum adapter plate 12 External snap ring 18 Spacer (Wired to spider adapter plate) Shim and shift the base of the movable shaft to correct the misalignment. After tightening the base, recheck the alignment and correct if necessary. Make sure to check for a "soft foot” condition. Dowel or chock into position after satisfactory aligment has been achieved. Note: On some applications, thermal growth of the mill or gear reducer (if present) may result in unacceptable shaft alignment in a...
Open the catalog to page 10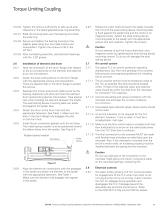
Rotate the motor shaft and push the spider towards the mill until the axial locking device mounting plate is flush against the spider face and the motor is on magnetic center. Attach the axial locking device mounting plate to the spider with the appropriate screws and lock washers. Tighten the screws. Caution Do not attempt to pull the motor shaft back onto magnetic center by tightening the axial locking device mounting screws. To do so will damage the axial locking device. Air control system The typical TLC air control system(s) operating charateristics vary from one grinding mill to...
Open the catalog to page 11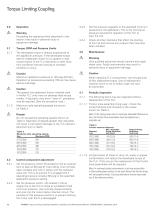
Operation Warning Exceeding the operating limits described in this section may result in personal injury or equipment damage. Torque, RPM and Pressure Limits The developed torque is directly proportional to the applied air pressure. If the developed torque seems inadequate, check for oil, grease or dust contamination of the TLC elements or other drive train conditions that are causing an overload condition to occur. Caution Maximum applied air pressure is 125 psig (8.5 bar). Operation at pressures exceeding 150 psi may cause element damage. Caution The special (non-asbestos) friction...
Open the catalog to page 12All Eaton Hydraulics catalogs and technical brochures
-
W Series
80 Pages
-
Eaton STC® Connectors Catalog
48 Pages
-
Eaton VSQ Vane Pumps
28 Pages
-
EHST-3-40 Series
8 Pages
-
Power amplifier
60 Pages
-
Fluid Conveyance Master Catalog
196 Pages
-
KBH-05 10 Series
22 Pages
-
GD5-Series
24 Pages
-
Motion control valves
124 Pages
-
KBCG-6-1
16 Pages
-
KBCG-3-1*
16 Pages
-
LifeSense Master Catalog
58 Pages
-
Electronic Feedback Cylinders
48 Pages
-
TLC Slip Detect Control Panel
18 Pages
-
Success made simple
16 Pages
-
Coils
14 Pages
-
2 Speed axial piston motor
14 Pages
-
Hydraulics Portfolio Brochure
12 Pages
-
Eaton HP50
4 Pages
-
Eaton Easy Couple H201
2 Pages
-
Eaton Delta motor
4 Pages
-
Eaton Weatherhead Core
20 Pages
-
Eaton Food Processing
26 Pages
-
Eaton Aeroquip Core
16 Pages
-
Eaton Engineered Solutions
12 Pages
-
Eaton EC600 X-FLEX
2 Pages
-
Press control blocks
4 Pages
-
Eaton Brass Products Master Catalog
166 Pages
-
Eaton® Industrial Cylinders
12 Pages
-
Airflex® Water-Cooled Brakes
22 Pages
-
Airflex® DBB & DBA Brakes
12 Pages
-
DG4V-3 70 Design Segment D
10 Pages
-
DG3V-8 & DG5V-8 Segment J
30 Pages
-
DG3V-7 & DG5V-7 Segment I
16 Pages
-
DG3V-5 & DG5V-5 Segment H
16 Pages
-
DG3V-3, DG4VP-3 Segment F
10 Pages
-
DG5V-7 30 Design & DG3V-7 20
16 Pages
-
Eaton Floating Housing Brake
8 Pages
-
Track Drive Motor - 2-Speed
16 Pages
-
Hydraulic Remote Controls
26 Pages
-
CNG Hose Catalog
12 Pages
-
External Gear Pump – GD5 Series
24 Pages
-
Low Speed, High Torque Motors
294 Pages
-
BECODISC Stacked Disc Cartridges
20 Pages
-
X20 Series 220 - Pump Catalog
20 Pages
-
Eaton Winner LQA Program - EMEA
54 Pages
-
Eaton Aeroquip Master Catalog
384 Pages
-
Eaton Guardian Seal
4 Pages
-
Accumulators Master Catalog
30 Pages
-
Filters Master Catalog
156 Pages
-
Industrial Hose and Tubing
216 Pages
-
Eaton?s Pump and Motor Products
24 Pages
-
E-HOEV-MC001
68 Pages
-
E-HOEV
2 Pages
-
EH066
2 Pages
-
A-HC
8 Pages
-
509200
4 Pages
-
E-HOBV
2 Pages
-
A-HOAK
69 Pages
-
et3000
19 Pages
-
ttc
28 Pages
-
ETRLD
20 Pages
-
x505901
21 Pages
-
509400
8 Pages
-
v fifi
36 Pages
-
i730
8 Pages
-
C001
23 Pages
-
XQ5
20 Pages
-
E2
21 Pages
-
E1
19 Pages
-
1E
2 Pages
-
DP
12 Pages
-
DBA
4 Pages
Archived catalogs
-
Accumulators
30 Pages
-
GEAR PUMPS AND MOTORS
35 Pages
-
ETON MOBILE VALVES
8 Pages
-
Hydro-Line® N5 Series Cylinders
36 Pages