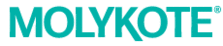

Catalog excerpts
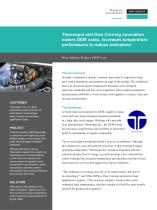
Thermopol and Dow Corning innovation lowers OEM costs, increases temperature performance to reduce emissions Hose Solution Reduces OEM Costs The environment In today’s automotive market, constant innovation is required to keep pace with competition and maintain an edge in the market. The combined forces of increased engine temperature demands, more stringent emissions standards and low-cost competitors force original equipment manufacturers (OEMs) to work closely with suppliers to reduce costs and increase performance. CUSTOMER Thermopol, Inc., is a New Hampshire-based producer of performance turbocharger, water coolant and specialty application hoses. PROJECT A North American OEM eliminated a component in its light duty truck engine design to save money and meet more stringent emissions standards. Working with Dow Corning, Thermopol enabled this solution by developing and commercializing a new hose liner solution that met increased temperature and oil resistance specifications, while reducing the standard product development and commercialization process time and costs. SOLUTION Multi-layered fluorosilicone and high-consistency rubber hose liner that met the increased temperature and oil resistance requirements set by the OEM. The challenge A North American automotive OEM sought to reduce costs and meet more stringent emissions standards in a light duty truck engine. Working with specialty hose manufacturer Thermopol Inc., the OEM found an innovative solution that allowed them to meet their goals by eliminating an engine component. The revised engine design presented a new set of problems. Although the solution cut costs and reduced emissions, it also increased engine operating temperature. Thermopol Inc. turned to long-time silicone solutions partner Dow Corning, to jointly develop a new material that could withstand the increased temperature specifications and the oil and fuel contact as well as other aggressive engine conditions. “The challenge was unique not only in its requirements, but also in its immediacy,” said Mike DiPino, Dow Corning automotive lead application engineer. “The customer needed a solution that could withstand high temperatures, and they needed it in half the time usually allowed for product development.”
Open the catalog to page 1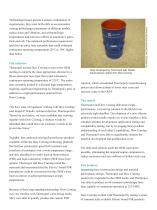
The solution Thermopol invited Dow Corning to join in the OEM meeting to identify the most appropriate silicone for a fluoro-elastomer hose liner that could withstand a continuous operating temperature of 235ºC. The entire hose assembly needed to withstand high temperatures, requiring significant engineering on Thermopol’s part, in addition to a high-performance material from Dow Corning. “We have years of experience working with Dow Corning,” said Joseph P. Schultz, technical director, Thermopol Inc. “Based on our history, we were confident that working together with Dow Corning, a...
Open the catalog to page 2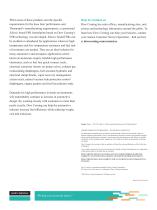
When none of these products met the specific requirements for the hose liner performance and Thermopol’s manufacturing requirements, a customized Silastic brand FSR formulation based on Dow Corning’s FSR technology was developed. Silastic brand FSRs can be molded or calendared for applications wherever high temperature and low temperature resistance and fuel and oil resistance are needed. They are an ideal solution for many automotive and aerospace applications where harsh environments require reliable high performance elastomers, such as fuel line quick-connect seals, electrical connector...
Open the catalog to page 3All Dow Corning catalogs and technical brochures
-
2 part RTV
6 Pages
-
Dow Corning and You Belgium
6 Pages
-
Elastomers from Dow Corning
8 Pages
-
Automotive Airbag
8 Pages
-
Molykote ® 1000
2 Pages
-
Molykote ® L-1210
2 Pages
-
Molykote ® Z Powder
2 Pages
-
Molykote? G-4501
2 Pages
-
Dow Corning Code of Conduct
10 Pages
-
Chip Scale Review Reprint
5 Pages
-
From the Pedal to the Pad
8 Pages
-
MOLYKOTE® 7325
2 Pages
-
MOLYKOTE® MH-62 GREASE
8 Pages
-
MOLYKOTE® 7325 GREASE
2 Pages
-
MOLYKOTE® HP-870
2 Pages
-
MOLYKOTE® 33
4 Pages
-
MOLYKOTE® BG-555
4 Pages
-
MOLYKOTE® G-0050
2 Pages
-
MOLYKOTE® 44
2 Pages
-
Molykote® 1292
2 Pages
-
MOLYKOTE® BR 2
2 Pages
-
Automative
4 Pages
-
Dow Corning Plasma Solutions
2 Pages
-
Design guide to optimize
8 Pages
-
Total Airbag Solutions
8 Pages
-
Adhesives advertisement
2 Pages
Archived catalogs
-
Molykote® Industrial Lubricants
52 Pages