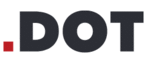

Catalog excerpts
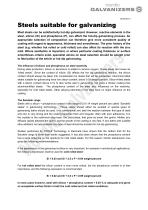
Steels suitable for galvanizing Most steels can be satisfactorily hot-dip galvanized. However, reactive elements in the steel, silicon (Si) and phosphorus (P), can affect the hot-dip galvanizing process. An appropriate selection of composition can therefore give more consistent quality of coating with regard to appearance, thickness and smoothness. The prior history of the steel (e.g. whether hot rolled or cold rolled) can also affect its reaction with the zinc melt. Where aesthetics is important, or where particular coating thickness or surface smoothness criteria exist, specialist advice on steel selection should be sought prior to fabrication of the article or hot dip galvanizing. The influence of silicon and phosphorus on steel reactivity During steel production, silicon or aluminium is added to remove oxygen. These steels are known as “killed steels”. Since the content of silicon (Si) affects the hot dip galvanizing reaction, the silicon content should always be taken into consideration for steels that will be galvanized. Aluminium-killed steels suitable for galvanizing have low silicon content, below 0.03 weight percent. Silicon-killed steels with a silicon content above 0.14 % also works well in galvanizing, but gives a thicker coating than aluminiumkilled steels. The phosphorus content of the steel also influences on the reactivity, especially for cold rolled steels. Other alloying elements in the steel have no major influence on the coating. The Sandelin range Steels with a silicon + phosphorus content in the range 0.03-0.14 weight percent are called “Sandelin steels” in galvanizing terminology. These steels should either be avoided or special types of galvanizing baths should be used. In a conventional zinc bath the reaction between this type of steel and zinc is very strong and the coating becomes thick and irregular, often with poor adherence. It is the crystals in the outermost alloy layer, the zeta-phase, that grow as small, thin grains. Molten zinc diffuses rapidly between the grains and the growth of the coating is very fast. If zinc baths with suitable alloy additions not are available, this type of steel should be avoided for hot-dip galvanizing. Studies performed by FORCE Technology in Denmark have shown that the bottom limit for the Sandelin range is lower than earlier suggested. It has also been shown that the phosphorus content has a large influence on the reactivity for cold rolled steels. For this reason, Nordic Galvanizers now gives the following recommendations: If the appearance of the galvanized surface is very important, for example in architectural applications, the following expression shall be used for cold rolled steel: Si < 0.03 and Si + 2.5 x P < 0.04 weight percent For hot rolled steel the silicon content is even more critical, but the phosphorus content is of less importance, and the following expression is recommended: Si < 0.02 and Si + 2.5 x P < 0.09 weight percent In most cases however, steel with silicon + phosphorus content < 0.03 % is adequate and gives an acceptable surface finish in both the cold rolled and hot rolled condit
Open the catalog to page 1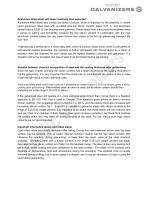
Aluminium killed steel with lower reactivity than expected Aluminium killed steels also contain low levels of silicon, which is important for the reactivity. In recent years aluminium killed steel with so-called ultra-low silicon content, below 0.01 %, and aluminium content above 0.035 % ,has become more common. These steels have many positive properties when it comes to cutting and formability, however the low silicon content in combination with the high aluminium content makes the zinc layers thinner than stated in the hot dip galvanizing standard EN ISO 1461. If galvanizing is performed...
Open the catalog to page 2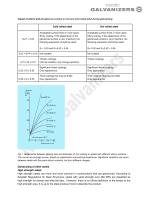
Impact of silicon and phosphorus content on hot and cold rolled steel during galvanizing: Cold rolled steel Hot rolled steel Acceptable surface finish in most cases. Shiny coating. If the appearance of the galvanized surface is very important, the following expression should be used: Acceptable surface finish in most cases. Shiny coating. If the appearance of the galvanized surface is very important, the following expression should be used: Thicker coatings. Internal oxidation may change reactivity. Thicker coatings. Significant thicker coatings. Grey appearance. Significant thicker...
Open the catalog to page 3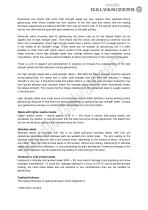
Experience has shown that some high strength steels are less reactive than expected during galvanizing, while others instead are very reactive. In the first case that means that the coating thickness requirement according to EN ISO 1461 may be hard to fulfil. In the second case the coating can be very thick and dull grey with poor adherence to the steel surface. Generally, when choosing steel for galvanizing, the same rules as for low alloyed steels can be applied also to high strength steel. That means that the silicon and phosphorus contents must be taken into consideration. Some high...
Open the catalog to page 4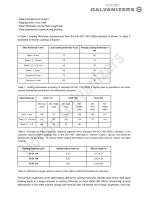
• Steel phosphorous content • Dipping time in zinc melt • Steel dimension and surface roughness • Heat treatments of steel during working In table 1 coating thickness requirements from the EN ISO 1461:2009 standard is shown. In table 2 examples of thicker coatings are given. Steel thickness in mm Local coating thickness in µm Average coating thickness in µm Table 1. Coating thicknesses according to standard EN ISO 1461:2009. If nothing else is specified in the order, coating thicknesses according to the table above are given. Steel thickness Table 2. Examples of thicker coatings. (National...
Open the catalog to page 5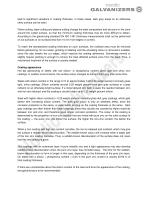
lead to significant variations in coating thickness. In these cases, dark grey areas on an otherwise shiny surface can be seen. Flame-cutting, laser-cutting and plasma-cutting change the steel composition and structure in the zone around the cutted surface, so that the minimum coating thickness may be more difficult to obtain. According to the galvanizing standard EN ISO 1461 thickness measurements shall not be performed on cut surfaces or on surfaces less than 10 mm from edges or corners. To reach the standardized coating thickness on such surfaces, the oxidized area must be removed before...
Open the catalog to page 6All DOT A/S catalogs and technical brochures
-
Zinc regulation
3 Pages
-
Operation and maintenance
3 Pages