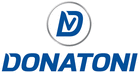
Catalog excerpts
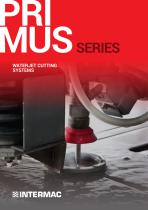
PRI MUS WATERJET CUTTING SYSTEMS
Open the catalog to page 1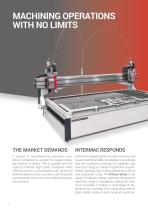
MACHINING OPERATIONS WITH NO LIMITS THE MARKET DEMANDS a change in manufacturing processes, enabling companies to accept the largest possible number of orders. This is coupled with the need to maintain high quality standards while offering product customisation with quick and defined delivery times, as well as satisfying the requirements of even the most highly-automated industries. INTERMAC RESPONDS with technological solutions which enhance and support technical skills, knowledge of processes and the continuous evolution of materials, and which can adapt to a range of application...
Open the catalog to page 2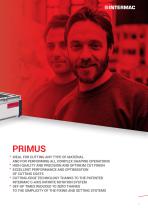
PRIMUS rIDEAL FOR CUTTING ANY TYPE OF MATERIAL AND FOR PERFORMING ALL COMPLEX SHAPING OPERATIONS rHIGH QUALITY AND PRECISION AND OPTIMUM CUT FINISH rEXCELLENT PERFORMANCE AND OPTIMISATION OF CUTTING COSTS rCUTTING-EDGE TECHNOLOGY THANKS TO THE PATENTED INTERMAC C-AXIS INFINITE ROTATION SYSTEM rSET-UP TIMES REDUCED TO ZERO THANKS TO THE SIMPLICITY OF THE FIXING AND SETTING SYSTEMS
Open the catalog to page 3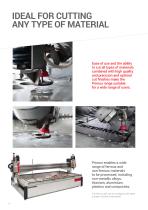
Ease of use and the ability to cut all types of materials combined with high quality and precision and optimal cut finishes make the Primus range suitable for a wide range of users. Primus enables a wide range of ferrous and non-ferrous materials to be processed, including non-metallic alloys, titanium, aluminium, plastics and composites. The Primus 402 can be configured with either a single or double cutting head.
Open the catalog to page 4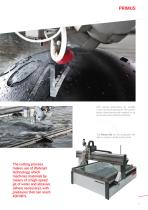
With special applications for variable Z-axis machining operations, this system allows three-dimensional materials to be processed using dedicated software. The Primus 202 can be configured with either a single or double cutting head. The cutting process makes use of Waterjet technology, which machines materials by means of a high-speed jet of water and abrasive (where necessary), with pressures that can reach 400 MPa. 5
Open the catalog to page 5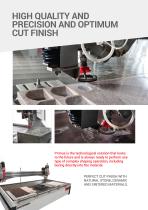
HIGH QUALITY AND PRECISION AND OPTIMUM CUT FINISH Primus is the technological solution that looks to the future and is always ready to perform any type of complex shaping operation, including boring directly into the material. PERFECT CUT FINISH WITH NATURAL STONE, CERAMIC AND SINTERED MATERIALS.
Open the catalog to page 6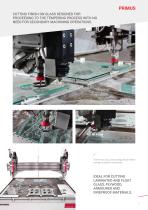
PRIMUS CUTTING FINISH ON GLASS DESIGNED FOR PROCEEDING TO THE TEMPERING PROCESS WITH NO NEED FOR SECONDARY MACHINING OPERATIONS. The Primus 322 can be configured with either a single or double cutting head. IDEAL FOR CUTTING LAMINATED AND FLOAT GLASS, PLYWOOD, ARMOURED AND FIREPROOF MATERIALS. 7
Open the catalog to page 7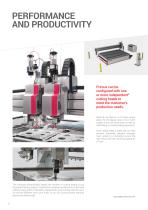
Primus can be configured with one or more independent* cutting heads to meet the customer's production needs. Work can be done on 3 or 5 axes, which allows for 45 degree cuts or 0 to +/-60° angled cuts to be performed, as well as chamfering or countersinking operations. Each cutting head is fitted with an independent, automatic abrasive management system to constantly ensure the right amount for the machining operation in hand. The software automatically adapts the number of cutting heads to suit the panels being created, to guarantee maximum productivity at all times without losing sight...
Open the catalog to page 8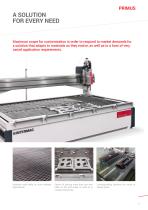
A SOLUTION FOR EVERY NEED Maximum scope for customisation in order to respond to market demands for a solution that adapts to materials as they evolve, as well as to a host of very varied application requirements. Stainless steel table for pure waterjet applications. Option of placing more than one template on the work table, in order to increase productivity. Locking/tooling systems for round or square pipes.
Open the catalog to page 9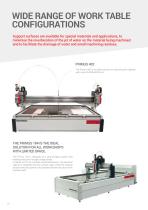
WIDE RANGE OF WORK TABLE CONFIGURATIONS Support surfaces are available for special materials and applications, to minimise the reverberation of the jet of water on the material being machined and to facilitate the drainage of water and small machining residues. PRIMUS 402 The Primus 402 is the ideal solution for machining all materials with a size of 4000x2000 mm. THE PRIMUS 184 IS THE IDEAL SOLUTION FOR ALL WORKSHOPS WITH LIMITED SPACE. The Primus 184 is designed as a plug-and-play system that enables production to begin straight away. It stands out for its compact overall dimensions - the...
Open the catalog to page 10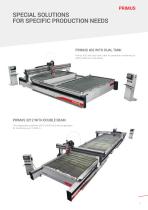
SPECIAL SOLUTIONS FOR SPECIFIC PRODUCTION NEEDS PRIMUS 402 WITH DUAL TANK Primus 402 with dual tank: ideal for pendulum machining for 4000 x 2000 mm size sheets. PRIMUS 3212 WITH DOUBLE BEAM Two independent machines (3210 x 6000 mm) with single beam for machining up to 12,000 m.
Open the catalog to page 11
SETTING AND BLOCKING AS SIMPLE AS POSSIBLE Once the piece has been positioned on the table and the machining parameters have been entered, the machine is ready to start cutting. Very simple blocking of the piece being machined (sometimes not even necessary), and minimal machine settings required. Aluminium set square for positioning the pieces. Clamps for locking the panel in place from 4 to 50 mm. Clamps for locking the panel in place from 1 to 3 mm.
Open the catalog to page 12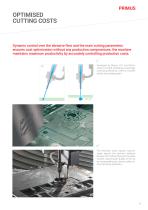
OPTIMISED CUTTING COSTS Dynamic control over the abrasive flow and the main cutting parameters ensures cost optimisation without any production compromises: the machine maintains maximum productivity by accurately controlling production costs. Developed by Biesse, JPC (Jet Performance Control) technology maximises machining efficiency in terms of profile quality and cutting speed The thickness tracer system automatically adjusts the optimum distance between the cutting head and the piece surface, improving the quality of the cut and guaranteeing the utmost safety during machining operations.
Open the catalog to page 13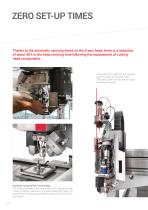
ZERO SET-UP TIMES Thanks to the automatic centring check on the 5-axis head, there is a reduction of about 90% in the head centring time following the replacement of cutting head components. Laser pointer for defining the positioning of the sheet on the work table. The laser pointer can be used for manual template learning. Maximum accessibility in total safety. The main advantage of this new solution with opening casing is that it enables customers to quickly inspect the head unit and perform maintenance operations, with no need to remove the casing. 14
Open the catalog to page 14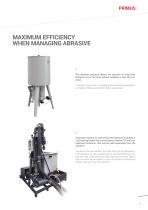
MAXIMUM EFFICIENCY WHEN MANAGING ABRASIVE The abrasive propulsor allows the operator to load fresh abrasive in the first tank without needing to stop the machine. It consists of two parts - one tank with an abrasive load capacity of about 330kg, and another that is pressurised. Automatic system for removing used abrasive (including a 1m3 big-bag holder with control panel, relative PLC and management software), that can be used separately from the machine. Thanks to this new solution, the work hours of the abrasive removal system can be programmed in any time band (e.g. during the night,...
Open the catalog to page 15All Donatoni catalogs and technical brochures
-
DONATONI JET 625
32 Pages
-
SPRINTER BRIDGE SAW CNC
36 Pages
-
SPIN CNC BRIDGE SAW
32 Pages