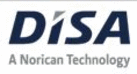
Catalog excerpts
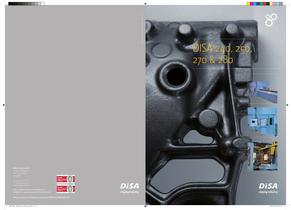
DISA 240, 250, 270 & 280 DISA Industries A/S Herlev Hovedgade 17 DK - 2730 Herlev Denmark T: +45 44 50 50 50 F: +45 44 94 52 25 www.disagroup.com Subject to technical alterations • 07/09 • © DISA Group Norican Group is the parent company of DISA and Wheelabrator. DISA® is a registered trademark of DISA Holding A/S. DISAMATIC® is a registered trademark of DISA Industries A/S. DB_DISA_NG240_280_2010_print.ind2-3 2-3 10.02.2010 06:35:55
Open the catalog to page 1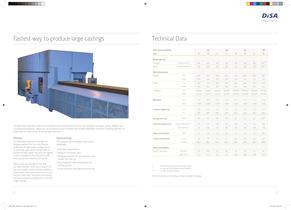
Fastest way to produce large castings The DISA New Generation series of vertical green sand moulding machines sets new standards for speed, quality, reliability and cost effective production. More than 150 foundries all over the world have installed DISA New Generation moulding machines for production of a wide variety of casting types and sizes. 2 Efficiency The DISA New Generation machines are designed perfectly for the cost effective production of large quality castings due to an extremely rigid machine design with an unmatched high speed. This gives the highest output compared to the...
Open the catalog to page 2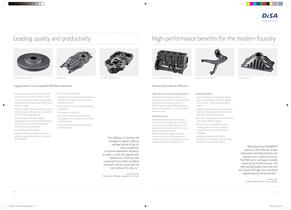
Leading quality and productivity 12 good reasons for choosing the DISA New Generation 6 Fastest moulding machine on the market with up to 450 uncored moulds an hour Superior uptime with fewer moving parts, more rigid design and reduced maintenance and parts usage Minimal machine-related mismatch for less fettling, lower production costs, increased efficiency and higher earnings Comprehensive real-time computer integrated manufacturing (CIM) monitoring and reporting for optimum production process efficiency and quality Low manpower requirements Automatic Pattern Change Unit for fast pattern...
Open the catalog to page 3
A sustainable solution Performance-enhancing options 4 5 Designed to be safe, clean and lean The DISA New Generation machines offer the following advantages to satisfy increasing demands concerning health, safety and consumption: In-chamber spray for enhanced workplace air quality, prevention of wear on pattern plates and minimised consumption of spray liquids Easy maintenance access for a safe working environment and time efficiency Quieter operation for a more comfortable working environment • • • Prepared for air exhaustion from the moulding chamber for clean working environment Use of...
Open the catalog to page 4All DISA catalogs and technical brochures
-
General Specifications Metric
20 Pages
-
DISAMATIC D3
8 Pages
-
DISAMATIC C3
4 Pages
-
General Specification
2 Pages
-
DISACOOL
4 Pages
-
DISA SMC
4 Pages
-
DISA TM Mixer
8 Pages
-
DISA SAM Mixer
8 Pages
-
Foundry Plan Solutions
8 Pages
-
DISA MATCH
4 Pages
-
DISA 231
4 Pages
-
DISAMATIC 2110
8 Pages
-
DISA 130
4 Pages
Archived catalogs
-
DISA Company presentation
6 Pages
-
DISA Global Service
6 Pages
-
DISACOOL Cooling drum
4 Pages
-
DISA Foundry Projects
8 Pages
-
DISA Aluminium process
6 Pages
-
DISA Core Solutions
8 Pages
-
DISA SAM MIXER
6 Pages
-
DISA TM Mixer
6 Pages
-
Aluminium shot blasting
2 Pages