
Catalog excerpts
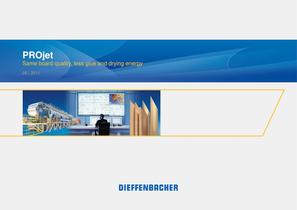
PROjet Same board quality, less glue and drying energy 05 | 2011
Open the catalog to page 1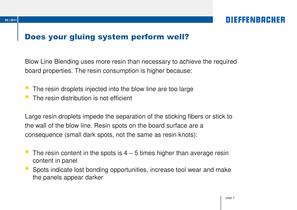
05 | 2011 Does your gluing system perform well? Blow Line Blending uses more resin than necessary to achieve the required board properties. The resin consumption is higher because: The resin droplets injected into the blow line are too large The resin distribution is not efficient Large resin droplets impede the separation of the sticking fibers or stick to the wall of the blow line. Resin spots on the board surface are a consequence (small dark spots, not the same as resin knots): The resin content in the spots is 4 – 5 times higher than average resin content in panel Spots indicate lost...
Open the catalog to page 2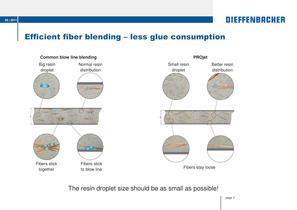
05 | 2011 Efficient fiber blending – less glue consumption Common blow line blending Big resin droplet Normal resin distribution Fibers stick together Fibers stick to blow line PROjet Small resin droplet Better resin distribution Fibers stay loose The resin droplet size should be as small as possible! page 3
Open the catalog to page 3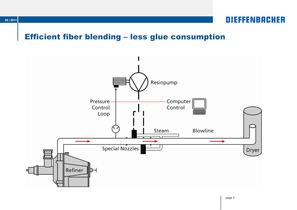
05 | 2011 Efficient fiber blending – less glue consumption page 4
Open the catalog to page 4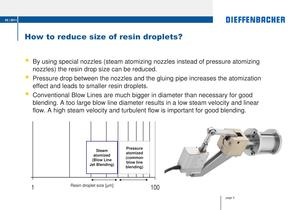
Resin atomization trough nozzle 05 | 2011 How to reduce size of resin droplets? By using special nozzles (steam atomizing nozzles instead of pressure atomizing nozzles) the resin drop size can be reduced. Pressure drop between the nozzles and the gluing pipe increases the atomization effect and leads to smaller resin droplets. Resin atomization trough Conventional Blow Lines are much bigger in diameter than necessary for good 1 blending. A too large blow line diameter results in nozzle steam velocity and linear a low flow. A high steam velocity and turbulent flow is important for good...
Open the catalog to page 5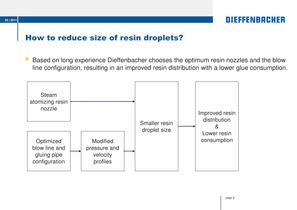
05 | 2011 How to reduce size of resin droplets? Based on long experience Dieffenbacher chooses the optimum resin nozzles and the blow line configuration, resulting in an improved resin distribution with a lower glue consumption. Steam atomizing resin nozzle Smaller resin droplet size Optimized blow line and gluing pipe configuration Modified pressure and velocity profiles Improved resin distribution & Lower resin consumption page 6
Open the catalog to page 6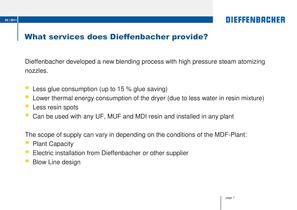
05 | 2011 What services does Dieffenbacher provide? Dieffenbacher developed a new blending process with high pressure steam atomizing nozzles. Less glue consumption (up to 15 % glue saving) Lower thermal energy consumption of the dryer (due to less water in resin mixture) Less resin spots Can be used with any UF, MUF and MDI resin and installed in any plant The scope of supply can vary in depending on the conditions of the MDF-Plant: Plant Capacity Electric installation from Dieffenbacher or other supplier Blow Line design page 7
Open the catalog to page 7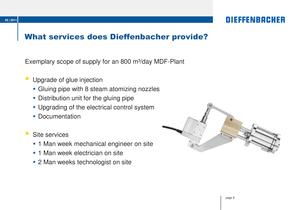
05 | 2011 What services does Dieffenbacher provide? Exemplary scope of supply for an 800 m³/day MDF-Plant Upgrade of glue injection Gluing pipe with 8 steam atomizing nozzles Distribution unit for the gluing pipe Upgrading of the electrical control system Documentation Site services 1 Man week mechanical engineer on site 1 Man week electrician on site 2 Man weeks technologist on site page 8
Open the catalog to page 8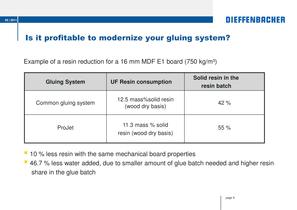
05 | 2011 Is it profitable to modernize your gluing system? Example of a resin reduction for a 16 mm MDF E1 board (750 kg/m³) Gluing System UF Resin consumption Solid resin in the resin batch Common gluing system 12.5 mass%solid resin (wood dry basis) 42 % ProJet 11.3 mass % solid resin (wood dry basis) 55 % 10 % less resin with the same mechanical board properties 46.7 % less water added, due to smaller amount of glue batch needed and higher resin share in the glue batch page 9
Open the catalog to page 9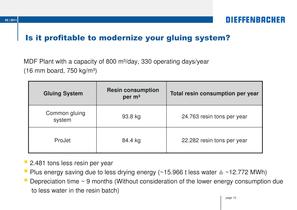
05 | 2011 Is it profitable to modernize your gluing system? MDF Plant with a capacity of 800 m³/day, 330 operating days/year (16 mm board, 750 kg/m³) Gluing System Resin consumption per m³ Total resin consumption per year 93.8 kg 24.763 resin tons per year 84.4 kg 22.282 resin tons per year Common gluing system ProJet 2.481 tons less resin per year Plus energy saving due to less drying energy (~15.966 t less water ≙ ~12.772 MWh) Depreciation time ~ 9 months (Without consideration of the lower energy consumption due to less water in the resin batch) page 10
Open the catalog to page 10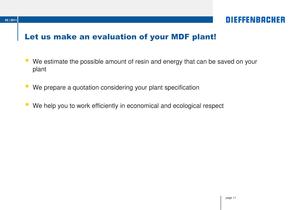
05 | 2011 Let us make an evaluation of your MDF plant! We estimate the possible amount of resin and energy that can be saved on your plant We prepare a quotation considering your plant specification We help you to work efficiently in economical and ecological respect page 11
Open the catalog to page 11All Dieffenbacher catalogs and technical brochures
-
Composites
12 Pages
-
Product Catalog
118 Pages
-
COMPRESS LITE
2 Pages
-
SMC DIRECTLINE
2 Pages
-
LFT direct process
3 Pages
-
Moulded product lines
5 Pages
-
Doorskin lines
3 Pages
-
Packaging line
3 Pages
-
Cut-to-size sawing line
8 Pages
-
Sanding line
4 Pages
-
CPS Press System
18 Pages
-
Preheating Systems
8 Pages
-
MDF Forming Concept
18 Pages
-
EVOjet?- and PROjet sys tems
2 Pages
-
EVOjet
4 Pages
-
Fiber Cleaning Process
22 Pages
-
Z-Sifter
3 Pages
-
Fiber drying process
3 Pages
-
ClassiCleaner Chip cleaning
18 Pages
Archived catalogs
-
Tools for metal forming
12 Pages
-
Wood based panel plant
12 Pages