
Catalog excerpts
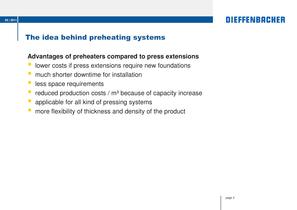
05 | 2011 The idea behind preheating systems Advantages of preheaters compared to press extensions lower costs if press extensions require new foundations much shorter downtime for installation less space requirements reduced production costs / m³ because of capacity increase applicable for all kind of pressing systems more flexibility of thickness and density of the product page 2
Open the catalog to page 2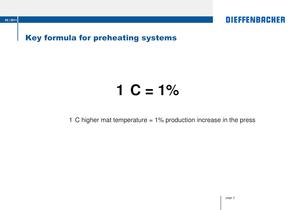
05 | 2011 Key formula for preheating systems 1 C = 1% 1 C higher mat temperature = 1% production increase in the press page 3
Open the catalog to page 3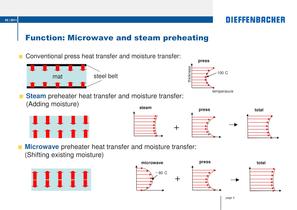
05 | 2011 Function: Microwave and steam preheating Conventional press heat transfer and moisture transfer: thickness mat mat press steel belt Steam preheater heat transfer and moisture transfer: (Adding moisture) steam 100 C 100 C temperature press total + Microwave preheater heat transfer and moisture transfer: (Shifting existing moisture) press microwave ~ 60 C total + page 4
Open the catalog to page 4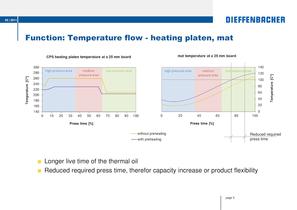
Function: Temperature flow - heating platen, mat CPS heating platen temperature at a 25 mm board high pressure area medium pressure area Press time [%] -with preheating Press time [%]
Open the catalog to page 5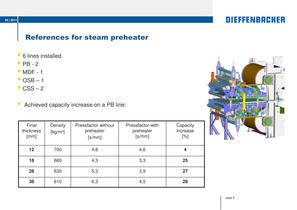
05 | 2011 References for steam preheater 6 lines installed PB - 2 MDF - 1 OSB – 1 CSS – 2 Achieved capacity increase on a PB line: Final thickness [mm] Density [kg/m³] Pressfactor without preheater [s/mm] Pressfactor with preheater [s/mm] Capacity Increase [%] 12 700 4,8 4,6 4 18 660 4,3 3,3 25 28 630 5,3 3,9 27 38 610 6,3 4,5 28 page 6
Open the catalog to page 6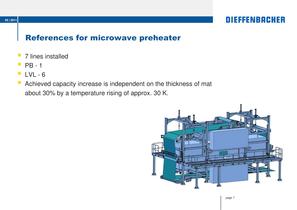
05 | 2011 References for microwave preheater 7 lines installed PB - 1 LVL - 6 Achieved capacity increase is independent on the thickness of mat about 30% by a temperature rising of approx. 30 K. page 7
Open the catalog to page 7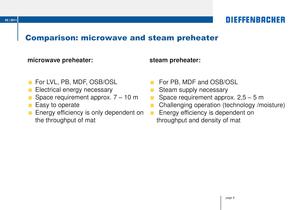
05 | 2011 Comparison: microwave and steam preheater microwave preheater: For LVL, PB, MDF, OSB/OSL Electrical energy necessary Space requirement approx. 7 – 10 m Easy to operate Energy efficiency is only dependent on the throughput of mat steam preheater: For PB, MDF and OSB/OSL Steam supply necessary Space requirement approx. 2,5 – 5 m Challenging operation (technology /moisture) Energy efficiency is dependent on throughput and density of mat page 8
Open the catalog to page 8All Dieffenbacher catalogs and technical brochures
-
Composites
12 Pages
-
Product Catalog
118 Pages
-
COMPRESS LITE
2 Pages
-
SMC DIRECTLINE
2 Pages
-
LFT direct process
3 Pages
-
Moulded product lines
5 Pages
-
Doorskin lines
3 Pages
-
Packaging line
3 Pages
-
Cut-to-size sawing line
8 Pages
-
Sanding line
4 Pages
-
CPS Press System
18 Pages
-
MDF Forming Concept
18 Pages
-
EVOjet?- and PROjet sys tems
2 Pages
-
PROjet
11 Pages
-
EVOjet
4 Pages
-
Fiber Cleaning Process
22 Pages
-
Z-Sifter
3 Pages
-
Fiber drying process
3 Pages
-
ClassiCleaner Chip cleaning
18 Pages
Archived catalogs
-
Tools for metal forming
12 Pages
-
Wood based panel plant
12 Pages