
Catalog excerpts
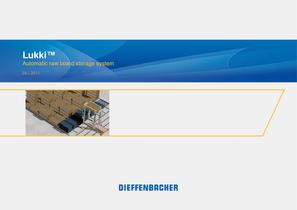
Lukki™ Automatic raw board storage system 05 | 2011
Open the catalog to page 1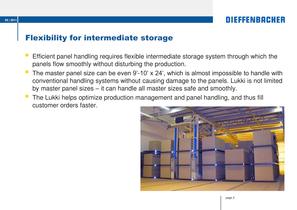
05 | 2011 Flexibility for intermediate storage Efficient panel handling requires flexible intermediate storage system through which the panels flow smoothly without disturbing the production. The master panel size can be even 9’-10’ x 24’, which is almost impossible to handle with conventional handling systems without causing damage to the panels. Lukki is not limited by master panel sizes – it can handle all master sizes safe and smoothly. The Lukki helps optimize production management and panel handling, and thus fill customer orders faster. page 2
Open the catalog to page 2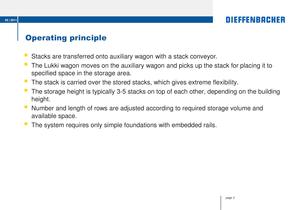
05 | 2011 Operating principle Stacks are transferred onto auxiliary wagon with a stack conveyor. The Lukki wagon moves on the auxiliary wagon and picks up the stack for placing it to specified space in the storage area. The stack is carried over the stored stacks, which gives extreme flexibility. The storage height is typically 3-5 stacks on top of each other, depending on the building height. Number and length of rows are adjusted according to required storage volume and available space. The system requires only simple foundations with embedded rails. page 3
Open the catalog to page 3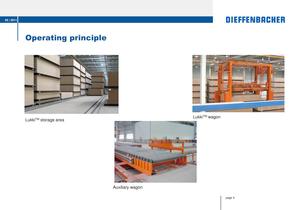
05 | 2011 Operating principle LukkiTM wagon LukkiTM storage area Auxiliary wagon page 4
Open the catalog to page 4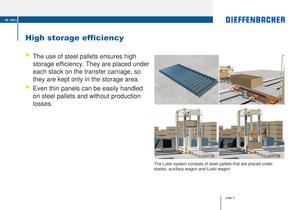
05 | 2011 High storage efficiency The use of steel pallets ensures high storage efficiency. They are placed under each stack on the transfer carriage, so they are kept only in the storage area. Even thin panels can be easily handled on steel pallets and without production losses. The Lukki system consists of steel pallets that are placed under stacks, auxiliary wagon and Lukki wagon page 5
Open the catalog to page 5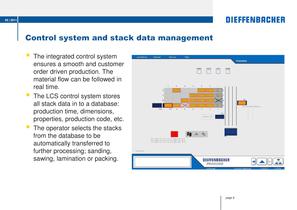
05 | 2011 Control system and stack data management The integrated control system ensures a smooth and customer order driven production. The material flow can be followed in real time. The LCS control system stores all stack data in to a database: production time, dimensions, properties, production code, etc. The operator selects the stacks from the database to be automatically transferred to further processing; sanding, sawing, lamination or packing. page 6
Open the catalog to page 6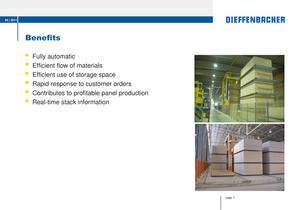
05 | 2011 Benefits Fully automatic Efficient flow of materials Efficient use of storage space Rapid response to customer orders Contributes to profitable panel production Real-time stack information page 7
Open the catalog to page 7All Dieffenbacher catalogs and technical brochures
-
Composites
12 Pages
-
Product Catalog
118 Pages
-
COMPRESS LITE
2 Pages
-
SMC DIRECTLINE
2 Pages
-
LFT direct process
3 Pages
-
Moulded product lines
5 Pages
-
Doorskin lines
3 Pages
-
Packaging line
3 Pages
-
Cut-to-size sawing line
8 Pages
-
Sanding line
4 Pages
-
CPS Press System
18 Pages
-
Preheating Systems
8 Pages
-
MDF Forming Concept
18 Pages
-
EVOjet?- and PROjet sys tems
2 Pages
-
PROjet
11 Pages
-
EVOjet
4 Pages
-
Fiber Cleaning Process
22 Pages
-
Z-Sifter
3 Pages
-
Fiber drying process
3 Pages
-
ClassiCleaner Chip cleaning
18 Pages
Archived catalogs
-
Tools for metal forming
12 Pages
-
Wood based panel plant
12 Pages