
Catalog excerpts
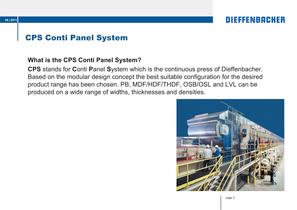
05 | 2011 CPS Conti Panel System What is the CPS Conti Panel System? CPS stands for Conti Panel System which is the continuous press of Dieffenbacher. Based on the modular design concept the best suitable configuration for the desired product range has been chosen. PB, MDF/HDF/THDF, OSB/OSL and LVL can be produced on a wide range of widths, thicknesses and densities. page 2
Open the catalog to page 2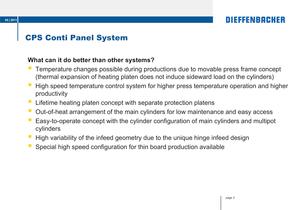
05 | 2011 CPS Conti Panel System What can it do better than other systems? Temperature changes possible during productions due to movable press frame concept (thermal expansion of heating platen does not induce sideward load on the cylinders) High speed temperature control system for higher press temperature operation and higher productivity Lifetime heating platen concept with separate protection platens Out-of-heat arrangement of the main cylinders for low maintenance and easy access Easy-to-operate concept with the cylinder configuration of main cylinders and multipot cylinders High...
Open the catalog to page 3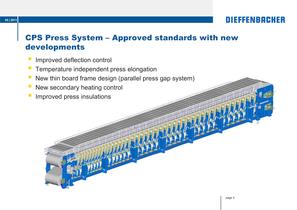
05 | 2011 CPS Press System – Approved standards with new developments Improved deflection control Temperature independent press elongation New thin board frame design (parallel press gap system) New secondary heating control Improved press insulations page 4
Open the catalog to page 4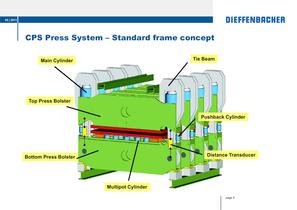
05 | 2011 CPS Press System – Standard frame concept Tie Beam Main Cylinder Top Press Bolster Pushback Cylinder Distance Transducer Bottom Press Bolster Multipot Cylinder page 5
Open the catalog to page 5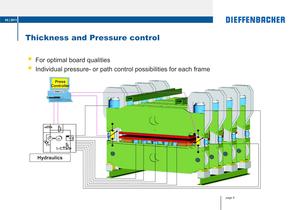
05 | 2011 Thickness and Pressure control For optimal board qualities Individual pressure- or path control possibilities for each frame Press Controller Hydraulics page 6
Open the catalog to page 6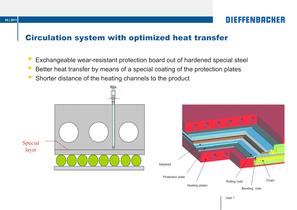
05 | 2011 Circulation system with optimized heat transfer Exchangeable wear-resistant protection board out of hardened special steel Better heat transfer by means of a special coating of the protection plates Shorter distance of the heating channels to the product Special layer Steelbelt Protection plate Rolling rods Heating platen Bending rods page 7 Chain
Open the catalog to page 7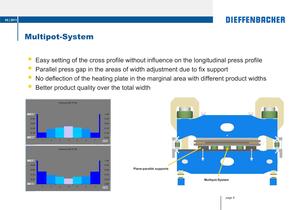
05 | 2011 Multipot-System Easy setting of the cross profile without influence on the longitudinal press profile Parallel press gap in the areas of width adjustment due to fix support No deflection of the heating plate in the marginal area with different product widths Better product quality over the total width Plane-parallel supports Multipot-System page 8
Open the catalog to page 8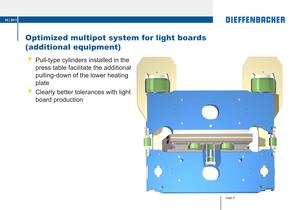
05 | 2011 Optimized multipot system for light boards (additional equipment) Pull-type cylinders installed in the press table facilitate the additional pulling-down of the lower heating plate Clearly better tolerances with light board production page 9
Open the catalog to page 9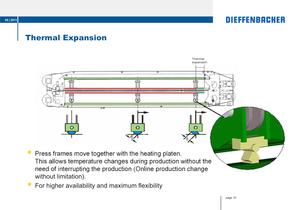
05 | 2011 Thermal Expansion Press frames move together with the heating platen. This allows temperature changes during production without the need of interrupting the production (Online production change without limitation). For higher availability and maximum flexibility page 10
Open the catalog to page 10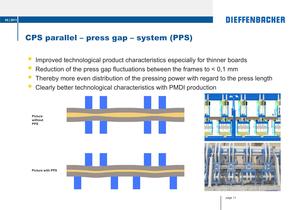
05 | 2011 CPS parallel – press gap – system (PPS) Improved technological product characteristics especially for thinner boards Reduction of the press gap fluctuations between the frames to < 0,1 mm Thereby more even distribution of the pressing power with regard to the press length Clearly better technological characteristics with PMDI production Picture without PPS Picture with PPS page 11
Open the catalog to page 11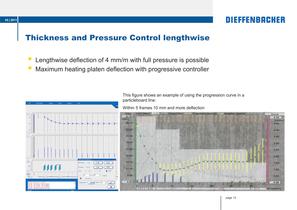
05 | 2011 Thickness and Pressure Control lengthwise Lengthwise deflection of 4 mm/m with full pressure is possible Maximum heating platen deflection with progressive controller This figure shows an example of using the progression curve in a particleboard line: Within 5 frames 10 mm and more deflection page 12
Open the catalog to page 12
05 | 2011 CPS heating regulation Faster control valves Temperature control to heating platen temperature Intelligent pilot control of the control valves XXYY % Controller (PLC) M Control valve 2-way M Pump (secondary circuit) Sensor (temp) Heating plate Temperature sensor page 13
Open the catalog to page 13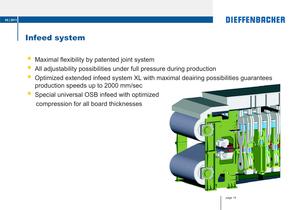
05 | 2011 Infeed system Maximal flexibility by patented joint system All adjustability possibilities under full pressure during production Optimized extended infeed system XL with maximal deairing possibilities guarantees production speeds up to 2000 mm/sec Special universal OSB infeed with optimized compression for all board thicknesses page 14
Open the catalog to page 14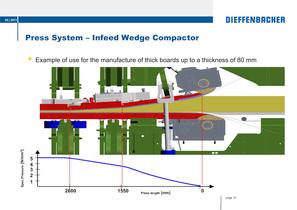
05 | 2011 Press System – Infeed Wedge Compactor Spec.Pressure [N/mm²] Example of use for the manufacture of thick boards up to a thickness of 80 mm 5 4 3 2 1 2600 1550 Press length [mm] 0 page 15
Open the catalog to page 15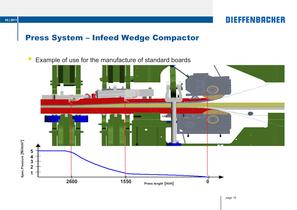
05 | 2011 Press System – Infeed Wedge Compactor Spec.Pressure [N/mm²] Example of use for the manufacture of standard boards 5 4 3 2 1 2600 1550 Press length [mm] 0 page 16
Open the catalog to page 16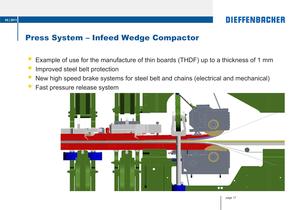
05 | 2011 Press System – Infeed Wedge Compactor Example of use for the manufacture of thin boards (THDF) up to a thickness of 1 mm Improved steel belt protection New high speed brake systems for steel belt and chains (electrical and mechanical) Fast pressure release system page 17
Open the catalog to page 17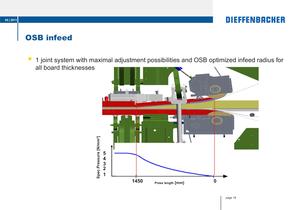
05 | 2011 OSB infeed Spec.Pressure [N/mm²] 1 joint system with maximal adjustment possibilities and OSB optimized infeed radius for all board thicknesses 5 4 3 2 1 1450 Press length [mm] 0 page 18
Open the catalog to page 18All Dieffenbacher catalogs and technical brochures
-
Composites
12 Pages
-
Product Catalog
118 Pages
-
COMPRESS LITE
2 Pages
-
SMC DIRECTLINE
2 Pages
-
LFT direct process
3 Pages
-
Moulded product lines
5 Pages
-
Doorskin lines
3 Pages
-
Packaging line
3 Pages
-
Cut-to-size sawing line
8 Pages
-
Sanding line
4 Pages
-
Preheating Systems
8 Pages
-
MDF Forming Concept
18 Pages
-
EVOjet?- and PROjet sys tems
2 Pages
-
PROjet
11 Pages
-
EVOjet
4 Pages
-
Fiber Cleaning Process
22 Pages
-
Z-Sifter
3 Pages
-
Fiber drying process
3 Pages
-
ClassiCleaner Chip cleaning
18 Pages
Archived catalogs
-
Tools for metal forming
12 Pages
-
Wood based panel plant
12 Pages