
Catalog excerpts
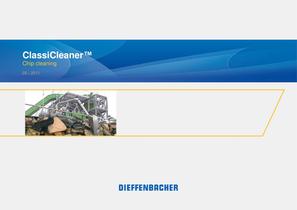
ClassiCleaner™ Chip cleaning 05 | 2011
Open the catalog to page 1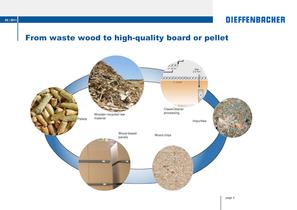
05 | 2011 From waste wood to high-quality board or pellet Pellets Wooden recycled raw material Wood-based panels ClassiCleaner processing Impurities Wood chips page 2
Open the catalog to page 2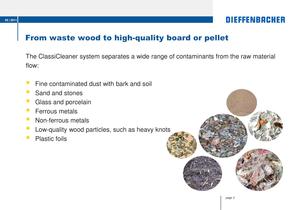
05 | 2011 From waste wood to high-quality board or pellet The ClassiCleaner system separates a wide range of contaminants from the raw material flow: Fine contaminated dust with bark and soil Sand and stones Glass and porcelain Ferrous metals Non-ferrous metals Low-quality wood particles, such as heavy knots Plastic foils page 3
Open the catalog to page 3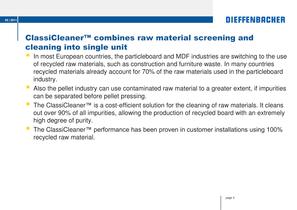
05 | 2011 ClassiCleaner™ combines raw material screening and cleaning into single unit In most European countries, the particleboard and MDF industries are switching to the use of recycled raw materials, such as construction and furniture waste. In many countries recycled materials already account for 70% of the raw materials used in the particleboard industry. Also the pellet industry can use contaminated raw material to a greater extent, if impurities can be separated before pellet pressing. The ClassiCleaner™ is a cost-efficient solution for the cleaning of raw materials. It cleans out...
Open the catalog to page 4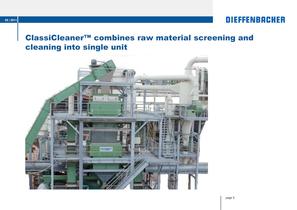
05 | 2011 ClassiCleaner™ combines raw material screening and cleaning into single unit page 5
Open the catalog to page 5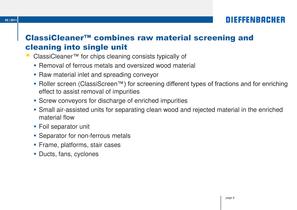
05 | 2011 ClassiCleaner™ combines raw material screening and cleaning into single unit ClassiCleaner™ for chips cleaning consists typically of Removal of ferrous metals and oversized wood material Raw material inlet and spreading conveyor Roller screen (ClassiScreen™) for screening different types of fractions and for enriching effect to assist removal of impurities Screw conveyors for discharge of enriched impurities Small air-assisted units for separating clean wood and rejected material in the enriched material flow Foil separator unit Separator for non-ferrous metals Frame, platforms,...
Open the catalog to page 6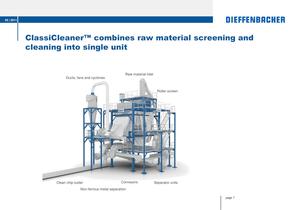
05 | 2011 ClassiCleaner™ combines raw material screening and cleaning into single unit Raw material inlet Ducts, fans and cyclones Roller screen Clean chip outlet Conveyors Separator units Non-ferrous metal separation page 7
Open the catalog to page 7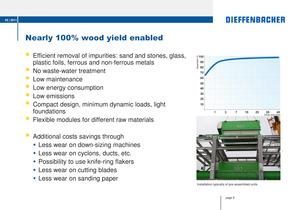
05 | 2011 Nearly 100% wood yield enabled Efficient removal of impurities: sand and stones, glass, plastic foils, ferrous and non-ferrous metals No waste-water treatment Low maintenance Low energy consumption Low emissions Compact design, minimum dynamic loads, light foundations Flexible modules for different raw materials Additional costs savings through Less wear on down-sizing machines Less wear on cyclons, ducts, etc. Possibility to use knife-ring flakers Less wear on cutting blades Less wear on sanding paper Installation typically of pre-assembled units page 8
Open the catalog to page 8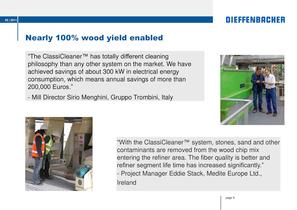
05 | 2011 Nearly 100% wood yield enabled “The ClassiCleaner™ has totally different cleaning philosophy than any other system on the market. We have achieved savings of about 300 kW in electrical energy consumption, which means annual savings of more than 200,000 Euros.” - Mill Director Sirio Menghini, Gruppo Trombini, Italy “With the ClassiCleaner™ system, stones, sand and other contaminants are removed from the wood chip mix entering the refiner area. The fiber quality is better and refiner segment life time has increased significantly.” - Project Manager Eddie Stack, Medite Europe Ltd.,...
Open the catalog to page 9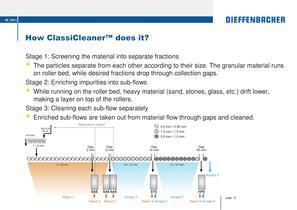
05 | 2011 How ClassiCleaner™ does it? Stage 1: Screening the material into separate fractions The particles separate from each other according to their size. The granular material runs on roller bed, while desired fractions drop through collection gaps. Stage 2: Enriching impurities into sub-flows While running on the roller bed, heavy material (sand, stones, glass, etc.) drift lower, making a layer on top of the rollers. Stage 3: Cleaning each sub-flow separately Enriched sub-flows are taken out from material flow through gaps and cleaned. page 10
Open the catalog to page 10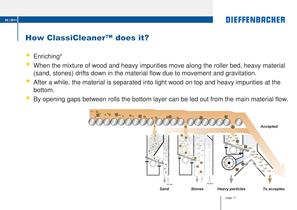
05 | 2011 How ClassiCleaner™ does it? Enriching* When the mixture of wood and heavy impurities move along the roller bed, heavy material (sand, stones) drifts down in the material flow due to movement and gravitation. After a while, the material is separated into light wood on top and heavy impurities at the bottom. By opening gaps between rolls the bottom layer can be led out from the main material flow. page 11
Open the catalog to page 11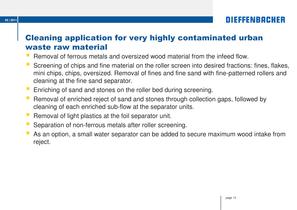
05 | 2011 Cleaning application for very highly contaminated urban waste raw material Removal of ferrous metals and oversized wood material from the infeed flow. Screening of chips and fine material on the roller screen into desired fractions: fines, flakes, mini chips, chips, oversized. Removal of fines and fine sand with fine-patterned rollers and cleaning at the fine sand separator. Enriching of sand and stones on the roller bed during screening. Removal of enriched reject of sand and stones through collection gaps, followed by cleaning of each enriched sub-flow at the separator units....
Open the catalog to page 12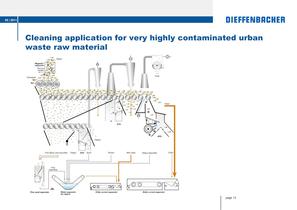
Cleaning application for very highly contaminated urban Fine flakes and impurities Flakes SAS Sand Stones Mini chips Heavy impurities Chips Fine sand separator Water separator Eddy current separator Eddy current separator
Open the catalog to page 13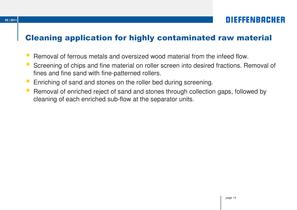
05 | 2011 Cleaning application for highly contaminated raw material Removal of ferrous metals and oversized wood material from the infeed flow. Screening of chips and fine material on roller screen into desired fractions. Removal of fines and fine sand with fine-patterned rollers. Enriching of sand and stones on the roller bed during screening. Removal of enriched reject of sand and stones through collection gaps, followed by cleaning of each enriched sub-flow at the separator units. page 14
Open the catalog to page 14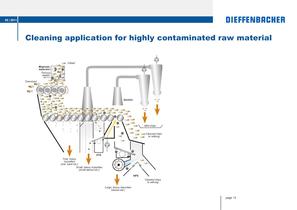
Cleaning application for highly contaminated raw material Fine, heavy Small, heavy impurities Cleaned chips Large, heavy impurities
Open the catalog to page 15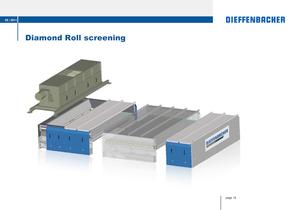
05 | 2011 Diamond Roll screening page 16
Open the catalog to page 16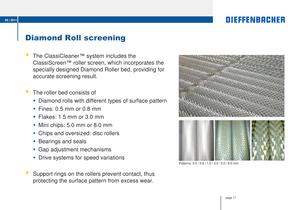
05 | 2011 Diamond Roll screening The ClassiCleaner™ system includes the ClassiScreen™ roller screen, which incorporates the specially designed Diamond Roller bed, providing for accurate screening result. The roller bed consists of Diamond rolls with different types of surface pattern Fines: 0.5 mm or 0.8 mm Flakes: 1.5 mm or 3.0 mm Mini chips: 5.0 mm or 8.0 mm Chips and oversized: disc rollers Bearings and seals Gap adjustment mechanisms Drive systems for speed variations Patterns: 0.5 / 0.8 / 1.5 / 3.0 / 5.0 / 8.0 mm Support rings on the rollers prevent contact, thus protecting the surface...
Open the catalog to page 17All Dieffenbacher catalogs and technical brochures
-
Composites
12 Pages
-
Product Catalog
118 Pages
-
COMPRESS LITE
2 Pages
-
SMC DIRECTLINE
2 Pages
-
LFT direct process
3 Pages
-
Moulded product lines
5 Pages
-
Doorskin lines
3 Pages
-
Packaging line
3 Pages
-
Cut-to-size sawing line
8 Pages
-
Sanding line
4 Pages
-
CPS Press System
18 Pages
-
Preheating Systems
8 Pages
-
MDF Forming Concept
18 Pages
-
EVOjet?- and PROjet sys tems
2 Pages
-
PROjet
11 Pages
-
EVOjet
4 Pages
-
Fiber Cleaning Process
22 Pages
-
Z-Sifter
3 Pages
-
Fiber drying process
3 Pages
Archived catalogs
-
Tools for metal forming
12 Pages
-
Wood based panel plant
12 Pages