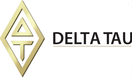

Catalog excerpts
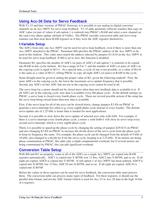
Technical Notes With V1.15 and later versions of PMAC firmware, it is possible to use analog-to-digital converter channels on an Acc-36P/V for servo loop feedback. V1.15 adds automatic software routines that copy an ADC value (or pair of values if sub-option 1 is ordered) into PMACs RAM and select a new channel on the card every phase update (default of 9 kHz). The PMAC encoder conversion table and servo loop routines can then treat these RAM registers as if they were the ADC registers themselves. > The ADCs from only one Acc-36P/V can be used for servo loop feedback, even if there is more than one Acc-36P/V attached to the PMAC. Parameter I60 specifies the PMAC address of the Acc-36P/V to be used in this fashion. This value must match the address selected by jumpers E1-E10 on the Acc-36P/V to be used for servo loop feedback. If I60 is set to zero, this function is disabled. Parameter I61 specifies the number of ADCs (or pairs of ADCs if sub-option 1 is ordered) to be copied into RAM in this cyclic fashion. I61 has a range of 0 to 7, and the number of ADCs or pairs of ADCs in the copying cycle is equal to I61+1. As a special note, a cycle of one is not possible, so a value of I61=0 is the same as a value of I61=7, telling PMAC to copy all eight ADCs (or pairs) in RAM in the cycle. Some thought must be given to setting the proper value of I61, given the following tradeoff. First, the more ADCs in the copying cycle, the lower the maximum servo update frequency that is possible. Second, any ADCs on this ADC that are not in the copying cycle cannot be used at all. The servo loop for a motor should not be closed more often than new feedback data is available to it. If all ADCs are in the copying cycle, new data is available every 8th phase cycle. At the default settings on PMAC, a servo loop is closed every fourth phase cycle. There are several possible actions if the setup has the servo loop being closed faster than new data is available. First, if the servo loop for all of the axes can be slowed down, change jumpers E3-E6 on PMAC to generate a servo interrupt less often (e.g. every eighth phase cycle instead of every fourth). The default servo update rate of 2.25 kHz is faster than is needed for most applications. Second, it is possible to slow down the servo update of selected axes only with Ix60. For example, if there is a servo interrupt every fourth phase cycle, a motor x with Ix60=1 will close its servo loop every second servo interrupt, which is every eighth phase cycle. Third, it is possible to speed up the phase cycle by changing the setting of jumpers E29-E33 on PMAC and also changing E3-E6 on PMAC to increase the divide-down of the servo cycle from the phase cycle to keep its frequency the same. For example, the phase cycle can be changed from the default of 9 kHz to 18 kHz, also changed to a divide-by-8 for the servo cycle, keeping it at 2.25 kHz. If no motors are doing phase commutation in PMAC, this adds only a slight computational overhead, but if several motors are being commutated by PMAC, this can add significant overhead. > With I60 and I61 set properly, some or all of the ADCs on a single Acc-36P/V are copied into RAM registers automatically. ADC1 is copied into Y:$0708, low 12 bits; ADC2 into Y:$0709, and so on. If all eight are copied, ADC8 is copied into Y:$070F. If sub-option 1 of Acc-36P/V has been ordered, ADC9 is copied into X:$0708, low 12 bits; ADC10 into X:$0709, and so on. If all eight are copied, ADC16 is copied into X:$070F. Before the values in these registers can be used for servo feedback, the conversion table must process them. The conversion table can process many types of feedback. For these registers, it should use the parallel data format, and not the ADC format (which is used for Acc-23 or Acc-28 data in the high 16 bits of a register). > Using Acc-36 Data for Servo Feedback 1 size="-1">
Open the catalog to page 1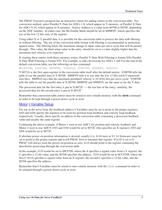
Using Acc-36 Data for Servo Feedback 2 >
Open the catalog to page 2All Delta Tau catalogs and technical brochures
-
Digital Counter/Tachometer H7CC
64 Pages
-
TURBO PMAC2 VME ULTRALITE
7 Pages
-
TURBO PMAC2 REALTIME EXPRESS
3 Pages
-
TURBO PMAC2 PCI
7 Pages
-
TURBO PMAC VME
6 Pages
-
POWER UMAC CPU 256 Axis
4 Pages
-
3U042
4 Pages
-
3U081
4 Pages
-
3U151
4 Pages
-
ACC-8D OPT4
3 Pages
-
ACC-8D OPT4A
3 Pages
-
ADVANTAGE 900 BASIC PACKAGE
3 Pages
-
PMAC MINI PCI 8 Axis
7 Pages
-
PMAC PCI 8 Axis
7 Pages
-
PMAC PCI LITE 8 Axis
7 Pages
-
PMAC VME 8 Axis
6 Pages
-
PMAC2A PC/104
6 Pages
-
POWER UMAC
4 Pages
-
TURBO UMAC
6 Pages
-
PMAC-NC PRO2 RUNTIME
3 Pages
-
Turbo Clipper Drive
2 Pages
-
Battery Issues with PMAC ISA
5 Pages
-
Digital IO accessories
2 Pages
-
MLDT Sensor
1 Pages
-
Slow communications
1 Pages