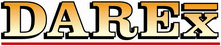
Catalog excerpts
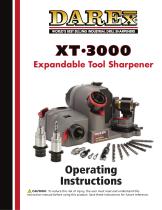
Operating Instructions CAUTION: To reduce the risk of injury, the user must read and understand this instruction manual before using this product. Save these instructions for future reference. 1
Open the catalog to page 1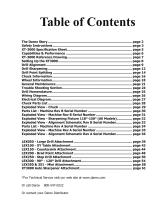
Or contact your Darex Distributor
Open the catalog to page 3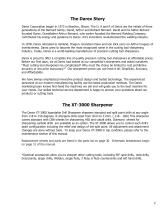
The Darex Story Darex Corporation began in 1973 in Beecher, Illinois. The D, A and R of Darex are the initials of three generations of the Bernard family; David, Arthur and Richard Bernard. David and his father Richard founded Darex. Grandfather Arthur Bernard, who earlier founded the Bernard Welding Company, contributed his energy and guidance to Darex. Art’s inventions revolutionized the welding industry. In 1978, Darex relocated to Ashland, Oregon. Grandson Dave and son Dick carry on Arthur’s legacy of inventiveness. Darex grew to become the most recognized name in the cutting tool...
Open the catalog to page 4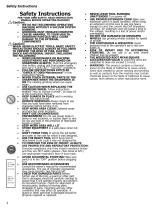
Safety Instructions Safety Instructions FOR YOUR OWN SAFETY, READ INSTRUCTION MANUAL BEFORE OPERATING MACHINE! WE DO NOT RECOMMEND OPERATING MACHINE WITHOUT A VACUUM SYSTEM RUNNING GRINDING DUST INHALED/INGESTED CAN BE HARMFUL TO YOUR HEALTH. GRINDING PARTIALS WILL CAUSE DAMAGE TO THE INTERNAL COMPONENTS • WHEN USING ELECTRIC TOOLS, BASIC SAFETY PRECAUTIONS SHOULD ALWAYS BE FOLLOWED • TO PREVENT THE RISK OF FIRE, ELECTRIC SHOCK AND PERSONAL INJURY, INCLUDING THE FOLLOWING: • • WHEN MAINTENANCE OR MACHINE ADJUSTMENTS ARE PERFORMED ON SHARPENER ALWAYS: Push the emergency • stop button, unplug...
Open the catalog to page 5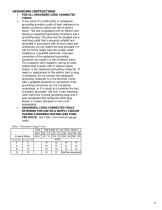
GROUNDING INSTRUCTIONS • FOR ALL GROUNDED CORD CONNECTED TOOLS: In the event of a malfunction or breakdown, grounding provides a path of least resistance for electric current to reduce the risk of electric shock. This tool is equipped with an electric cord having an equipment-grounding conductor and a grounding plug. The plug must be plugged into a matching outlet that is properly installed and grounded in accordance with all local codes and ordinances. Do not modify the plug provided if it will not fit the outlet, have the proper outlet installed by a qualified electrician. Improper...
Open the catalog to page 6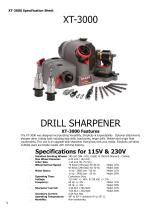
DRILL SHARPENER XT-3000 Features The XT-3000 was designed incorporating Versatility, Simplicity & Expandability. Optional attachments sharpen other cutting tools including step drills, brad points, larger drills, Weldon and single flute countersinks. This unit is an upgrade-able sharpener that grows with your needs. Simplicity will allow multiple users successful results with minimal training. Standard Grinding Wheels: Max Wheel Diameter: Arbor Size: Wheel Surface Speed: Motor Specs: Operating Time: Voltage: Frequency: Sharpener Current: Accessory Current: Operating Temperature: Humidity:...
Open the catalog to page 7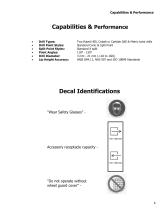
Capabilities & Performance Capabilities & Performance • • • • • • Drill Types: Drill Point Styles: Split Point Styles: Point Angles: Drill Diameter: Lip Height Accuracy: Two fluted HSS, Cobalt or Carbide SAE & Metric twist drills Standard Conic & Split Point Standard X split 118° - 150° 3 mm - 21 mm (.118 to .826) ANSI B94.11, NAS 907 and ISO 10899 Standards Decal Identifications “Wear Safety Glasses” - Accessory receptacle capacity - “Do not operate without wheel
Open the catalog to page 8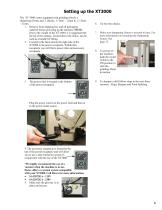
Setting up the XT3000 The XT-3000 comes equipped with grinding wheels, a sharpening fixture and 2 chucks, 1; 3mm – 12mm & 1; 12mm – 21mm. 1. Remove from shipping box and all packaging material before powering up the machine. NOTE: Due to the weight of the XT-3000, it is suggested that the lip of the casting, located above the motor, can be used as a handle for lifting. 2. Located at the back and on the right side of the XT3000 is the power receptacle. Within that receptacle you will find a power inlet and accessory receptacle. The power inlet is located at the bottom of the power...
Open the catalog to page 10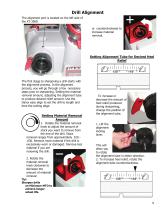
Drill Alignment The alignment port is located on the left side of the XT-3000. or counterclockwise to increase material removal. Setting Alignment Tube for Desired Heel Relief 135° The first stage to sharpening a drill starts with the alignment process. In the alignment process, you will go through a few necessary steps prior to sharpening. Setting the material removal amount, adjusting the alignment tube to produce desired relief amount. Use the Darex easy align to set the drill to length and time the cutting edge. Setting Material Removal Amount 1. Rotate the material removal knob to...
Open the catalog to page 11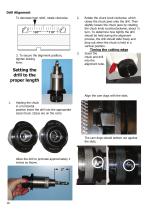
Drill Alignment To decrease heel relief, rotate clockwise. 3. To secure the alignment position, tighten locking lever. Rotate the chuck knob clockwise, which closes the chuck jaws onto the drill. Then slightly loosen the chuck jaws by rotating the chuck knob counterclockwise, about ½ turn. To determine how tightly the drill should be held during the alignment process, the drill should slide freely and drop out when the chuck is held in a vertical position. Timing the cutting edge Insert the chuck and drill into the alignment tube. Setting the drill to the proper length Align the cam dogs...
Open the catalog to page 12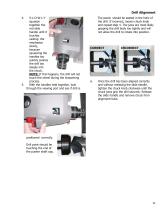
S-L-O-W-L-Y squeeze together the red slide handle until it touches casting. We emphasize slowly, because squeezing the handles too quickly pushes the drill too deeply into the chuck. NOTE: If this happens, the drill will not touch the wheel during the sharpening process. 5. With the handles held together, look through the viewing port and see if drill is The pawls should be seated in the helix of the drill. If incorrect, loosen chuck knob and repeat step 4. The jaws are most likely gripping the drill body too tightly and will not allow the drill to rotate into position. Once the drill has...
Open the catalog to page 13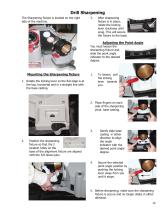
Drill Sharpening The Sharpening fixture is located on the right side of the machine. After sharpening fixture is in place, rotate the locking lever clockwise until snug. This will secure the fixture to the base. Adjusting the Point Angle You must loosen the sharpening fixture and slide the point angle indicator to the desired degree. Mounting the Sharpening fixture 1. Rotate the locking lever so the flat edge is at the top, horizontal and in a straight line with the base casting. To loosen, pull the locking lever towards you. 2. Place fingers on each side of the sharpening pivot base...
Open the catalog to page 14All Darex catalogs and technical brochures
-
Large Drill Attachment LEX050
19 Pages
-
V-390 Drill Sharpener
20 Pages