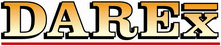
Catalog excerpts
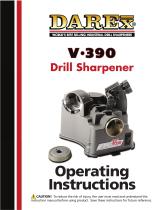
DAREX V390 Drill Sharpener ® Operating Instructions CAUTION! To reduce the risk of injury, the user must read and understand this instruction manual before using product. Save these instructions for future referen
Open the catalog to page 1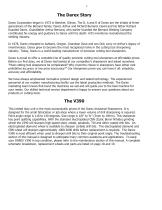
The Darex Story Darex Corporation began in 1973 in Beecher, Illinois. The D, A and R of Darex are the initials of three generations of the Bernard family; David, Arthur and Richard Bernard. David and his father Richard founded Darex. Grandfather Arthur Bernard, who earlier founded the Bernard Welding Company contributed his energy and guidance to Darex until his death. Art’s inventions revolutionized the welding industry. In 1978, Darex relocated to Ashland, Oregon. Grandson Dave and son Dick carry on Arthur’s legacy of inventiveness. Darex grew to become the most recognized name in the...
Open the catalog to page 3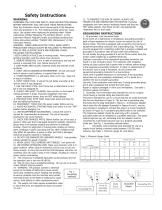
Safety Instructions 21. TO MINIMIZE THE RISK OF INJURY, ALWAYS USE PROPER EYE AND RESPIRATORY PROTECTION: Everyday REMEMBER FOR YOUR OWN SAFETY, READ INSTRUCTION MANUAL eyeglasses only have impact resistance lenses and they are BEFORE OPERATING TOOL AND SAVE THESE INSTRUCTIONS. NOT safety glasses. (See Decal at Left.) Use appropriate Wear Eye Protection. Never touch internal parts of the sharpener respiratory face or dust mask. when the sharpener is on. The rotating grinding wheel can cause injury. Use caution when replacing the grinding wheel. Follow GROUNDING INSTRUCTIONS instructions...
Open the catalog to page 4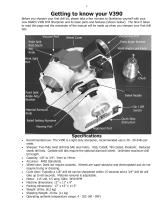
Getting to know your V390 Before you sharpen your first drill bit, please take a few minutes to familiarize yourself with your new DAREX V390 Drill Sharpener and its basic parts and features (shown below). The time it takes to read this page and the remainder of the manual will be made up when you sharpen your first drill bits. Vacuum Port Sharpening Port Wheel Cover Point Split Port Depth Adj. Knob Point Angle Bracket Point Angle Lock Knob Point Split Port Point Split Angle Adj. Bracket Relief Paddle Material Removal Knob Quick Step Instruction Relief Setting Numbers Viewing Port Alignment...
Open the catalog to page 5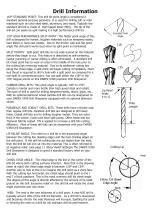
Drill Information 118º STANDARD POINT: This drill bit point angle is considered a standard general-purpose geometry. It is used for drilling soft or mild materials such as cold rolled steel, aluminum, and wood. Typically the standard drill bit is made of High Speed Steel (HSS). The tip of the drill bit can easily be split making it a high performance drill bit. Included Point Angle 135º HIGH PERFORMANCE SPLIT-POINT: The flatter point angle of this drill is designed for harder, tougher materials such as tempered steels, hard alloys or hard cast metals. Due to the thicker web and flat point...
Open the catalog to page 6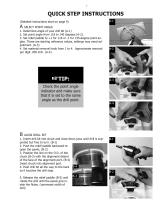
QUICK STEP INSTRUCTIONS A-1 (Detailed instructions start on page 9) SELECT POINT ANGLE 1. Determine angle of your drill bit (A-1) 2. Set point angle from 118 to 140 degrees (A-2). 3. Set relief paddle to +1 for 118 or -1 for 135-degree point angles. These are starting reference values, settings may need adjustment. (A-3) 4. Set material removal knob from 1 to 4. Approximate removal per digit .005 inch. (A-4) Check the point angle indicator and make sure that it is set to the same angle as the drill point. ALIGN DRILL BIT 1. Insert drill bit into chuck and close down jaws until drill is...
Open the catalog to page 7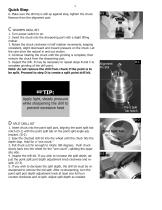
Quick Step 6. Make sure the drill tip is still up against stop, tighten the chuck. Remove from the alignment port. SHARPEN DRILL BIT 1. Turn power switch to on. 2. Insert the chuck into the sharpening port with a slight lifting motion. 3. Rotate the chuck clockwise in half rotation increments, keeping consistent, slight downward and inward pressure on the chuck. Let the cam drive the natural in and out motion. 4. Continue rotating the chuck until the grinding is complete, then remove the chuck from the sharpening port. 5. Inspect the drill. It may be necessary to repeat steps B and C to...
Open the catalog to page 8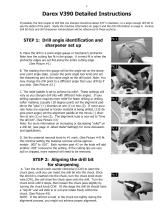
Darex V390 Detailed Instructions If possible, the first couple of drill bits you sharpen should be about 3/8” in diameter, or a large enough drill bit to see the detail of the point. Study the machine information on page 5 and the drill information on page 6. Various drill bit facts and drill sharpener nomenclature will be referenced in these sections. STEP 1: Drill angle identification and sharpener set up A. Place the drill in a point angle gauge or mechanic’s protractor. Note how the cutting lips fit in the gauge. A correct fit is when the protractor edges are set flat along the entire...
Open the catalog to page 9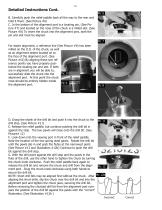
Detailed Instructions Cont. B. Carefully push the relief paddle back all the way to the rear and hold it there. (See Picture #6) C. In the bottom of the alignment port is a locating pin, (See Picture #7) and located on the nose of the chuck is a milled slot. (See Picture #8) To insert the chuck into the alignment port, both the pin and slot must be aligned. Pic 7 For easier alignment, a reference line (See Picture #9) has been milled on the O.D. of the chuck, as well as an alignment detent located on to the face of the alignment port. (See Picture #10) By aligning these two reference points...
Open the catalog to page 10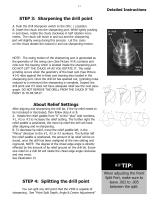
Detailed Instructions STEP 3: Sharpening the drill point A. Push the Drill Sharpener switch to the ON ( | ) position. B. Insert the chuck into the sharpening port. While lightly pushing in and down, rotate the chuck clockwise in half rotation increments. The chuck will move in and out and the sharpening port will slightly swing during this process. Let the cams on the chuck dictate the natural in and out sharpening motion. NOTE: The swing motion of the sharpening port is generated as the geometry of the swing cam (See Picture #14) contacts and rolls over the bearing which is located inside...
Open the catalog to page 11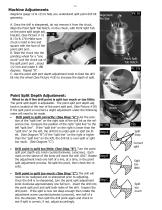
Machine Adjustments diagrams (page 12 & 13) to help you understand split point drill bit geometry. A. Once the drill is sharpened, do not remove it from the chuck. Align the Point Split Tab Notch, on the chuck, with Point Split Tab on the point split angle adj. bracket. (See Picture # 16 Pic 18 & 17a & 17b) Make sure chuck is held in-line and square with the face of the point split port. B. Slide the chuck into the grinding wheel for a “one count” pull the chuck out of the split point port , about 1/2 inch and rotate it 180 degrees. Repeat “B”. C. Use the point split port depth adjustment...
Open the catalog to page 12All Darex catalogs and technical brochures
-
Large Drill Attachment LEX050
19 Pages