
Catalog excerpts
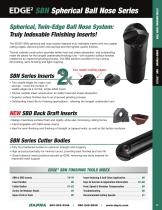
Spherical, Twin-Edge Ball Nose System: Truly Indexable Finishing Inserts! BALL NOSE FINISHING MILLS SBN Spherical Ball Nose Series Thicker carbide construction provides better heat and stress absorption, and outstanding insert life allows for the longest unattended finishing runs – with superior surface finishes created by an improved grinding process. The SBN series is excellent for tip-cutting, 3D profiling, semi-finishing and light roughing. Two usable cutting edges! The EDGE² SBN spherical ball nose system features truly indexable inserts with two usable cutting edges, delivering both cost savings and the highest-quality finishes. • wo usable edges for major cost T savings – twice the number of usable edges as a normal, single-sided insert • Thicker carbide insert construction for better heat and stress absorption • Superior surface finishes due to an improved grinding process • Outstanding insert life for finishing applications – allowing the longest unattended runs NEW SBD Back Draft Inserts • Design maximizes surface finish and rigidity while also minimizing cutting forces • Interchangeable with SBN series inserts • Ideal for semi-finishing and finishing of straight or tapered walls, as well as flat-bottom surfaces SBN Series Cutter Bodies • Fully thru-hardened bodies for optimum strength and longevity • High accuracy/centrality for minimal runout, providing best finishes and tool life • lose-tolerance insert pocket produced by EDM, removing less body material for C improved insert support
Open the catalog to page 1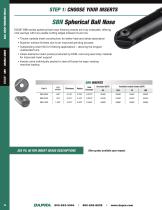
BALL NOSE FINISHING MILLS STEP 1: CHOOSE YOUR INSERTS SBN Spherical Ball Nose EDGE² SBN series spherical ball nose finishing inserts are truly indexable, offering cost savings with two usable cutting edges instead of just one. • Thicker carbide insert construction for better heat and stress absorption • Superior surface finishes due to an improved grinding process • utstanding insert life for finishing applications – allowing the longest O unattended runs • lose-tolerance insert pocket produced by EDM, removing less body material C for improved insert support • nserts come individually...
Open the catalog to page 2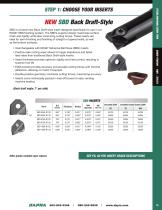
BALL NOSE FINISHING MILLS STEP 1: CHOOSE YOUR INSERTS NEW SBD Back Draft-Style SBD is a brand-new Back Draft-style insert designed specifically for use in our EDGE2 SBN finishing system. The SBD’s superior design maximizes surface finish and rigidity while also minimizing cutting forces. These inserts are ideal for semi-finishing and finishing of straight or tapered walls, as well as flat-bottom surfaces. • Interchangeable with EDGE2 Spherical Ball Nose (SBN) inserts • Positive-rake cutting wiper allows for larger stepdowns and faster feed rates than traditional Back Draft-style inserts •...
Open the catalog to page 3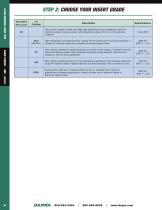
BALL NOSE FINISHING MILLS STEP 2: CHOOSE YOUR INSERT GRADE Uncoated (Base Grade) Sub-micron tungsten carbide with high edge strength and good toughness. Good for machining steels, stainless steels, high-temperature alloys, cast iron, and nonferrous materials. High-temperature and high-hardness coating. Proven performance and wear resistance in virtually all materials makes this a versatile and simple grade choice. New coating intended for general-purpose use across a wide variety of materials including steels and stainless steels. High-temperature grade providing excellent heat and wear...
Open the catalog to page 4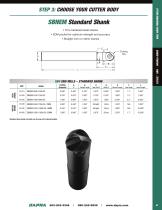
BALL NOSE FINISHING MILLS STEP 3: CHOOSE YOUR CUTTER BODY SBNEM Standard Shank • Thru-hardened steel shanks • EDM pocket for optimum strength and accuracy • Straight inch or metric shanks SBN END MILLS – STANDARD SHANK EDP Cutting Diameter Straight Length Effective Length Taper Angle Overall Length METRIC SHANK INCH SHANK Standard steel shank end mills
Open the catalog to page 5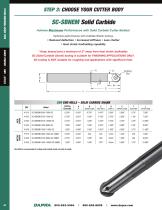
BALL NOSE FINISHING MILLS STEP 3: CHOOSE YOUR CUTTER BODY SC-SBNEM Solid Carbide Achieve Maximum Performance with Solid Carbide Cutter Bodies! Optimize performance with Carbide Shank tooling: • Reduced deflection • Increased stiffness • Less chatter • Heat shrink toolholding capability * Keep brazed joint a minimum of 2” away from heat shrink toolholder. SC (Solid Carbide Shank) tooling is suitable for FINISHING APPLICATIONS ONLY. SC tooling is NOT suitable for roughing and applications with significant heat. SBN END MILLS – SOLID CARBIDE SHANK EDP Cutting Diameter Straight Length Effective...
Open the catalog to page 6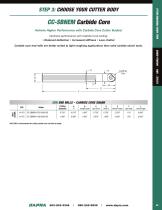
BALL NOSE FINISHING MILLS STEP 3: CHOOSE YOUR CUTTER BODY CC-SBNEM Carbide Core Achieve Higher Performance with Carbide Core Cutter Bodies! Optimize performance with Carbide Core tooling: • Reduced deflection • Increased stiffness • Less chatter Carbide core end mills are better suited to light roughing applications than solid carbide shank tools. SBN END MILLS – CARBIDE CORE SHANK INCH SHANK Cutting Diameter Straight Length Effective Length Taper Angle Overall Length Wire EDM is recommended for cutting carbide core end mills to length.
Open the catalog to page 7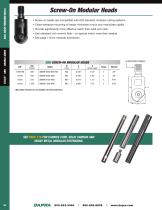
BALL NOSE FINISHING MILLS Screw-On Modular Heads • crew-on heads are compatible with ISO standard modular cutting systems S • lose-tolerance mounting of heads minimizes runout and maximizes rigidity C • rovide significantly more effective reach than solid end mills P • se standard inch wrench flats – no special metric wrenches needed U • See page 116 for modular extensions SBN SCREW-ON MODULAR HEADS DIA Effective Length * M8 modular extensions are not available. Use ISO standard bars. SEE PAGE 116 FOR CARBIDE CORE, SOLID CARBIDE AND HEAVY METAL MODULAR EXTENSIONS.
Open the catalog to page 8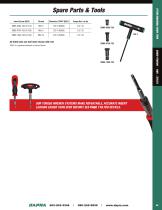
All listed tools use Anti-Seize Grease ASG-120. BALL NOSE FINISHING MILLS Spare Parts & Tools TORX ® is a registered trademark of Camcar/Textron. OUR TORQUE WRENCH SYSTEMS MAKE REPEATABLE, ACCURATE INSERT LOADING EASIER THAN EVER BEFORE! SEE PAGE 118 FOR DETAILS.
Open the catalog to page 9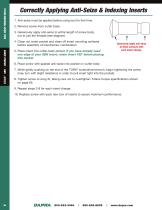
BALL NOSE FINISHING MILLS Correctly Applying Anti-Seize & Indexing Inserts 1. nti-seize must be applied before using tool for first time. A 2. emove screw from cutter body. R 3. enerously apply anti-seize to entire length of screw body, G not to just the threads (see diagram). 4. lean out insert pocket and clean off insert mounting surfaces C before assembly of insert/screw combination. Generously apply anti-seize to these surfaces with each insert change. 5. lace insert into cutter-body pocket. If you have already used P one edge of your SBN insert, rotate insert 180° before placing into...
Open the catalog to page 10All Dapra Milling Solutions catalogs and technical brochures
-
Single-Sided Toroid Series
23 Pages
-
High Feed Indexable Milling
12 Pages
-
EXTREMEMetal Removal
25 Pages