
Catalog excerpts
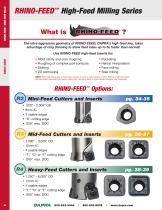
RHINO-FEED ™ HIGH-FEED MILLS RHINO-FEED ™ High-Feed Milling Series FEED What is The ultra-aggressive geometry of RHINO-FEED, DAPRA’s high-feed line, takes advantage of chip thinning to allow feed rates up to 5x faster than normal! Use RHINO-FEED high-feed inserts for: SINGLE-SIDED • old cavity and core roughing M • oughing of complex part contours R • Slotting • 2D contouring • Pocketing • Helical interpolation •FEED F ace milling • Step milling NOTE: High-feed milling does a tremendous amount of work in a short period of time. This line's high production rate can create more heat than typical milling tools. Strong air blast is recommended (multiple lines if possible). RHINO-FEED ™ Options: R2 Mini-Feed Cutters and Inserts • • • • • .500” - 2.000” OD 8mm IC 3 usable edges “D” cutting edge .030” max. DOC R3 Mid-Feed Cutters and Inserts • • • • • 1.000” - 3.000” OD 10mm IC 4 usable edges “T,” “D” or “F” cutting edge .045” max. DOC R4 Heavy-Feed Cutters and Inserts • • • • • 32
Open the catalog to page 1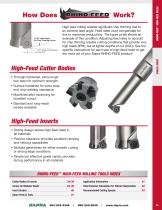
.010” actual chip thickness At .050” FPT High-feed milling creates significant chip thinning due to an extreme lead angle. Feed rates must compensate for FEED this to maximize productivity. The figure at left shows an example of this condition. Adjusting feed rates to account for chip thinning creates cutting conditions that provide very high feeds (IPM), but at lighter depths of cut (DOC). See the specific instructionsFEED of high-feed insert to get for each size the most out of your Dapra RHINO-FEED product! 11.50° Lead Angle (5x Chip Thinning Factor) RHINO-FEED ™ HIGH-FEED MILLS...
Open the catalog to page 2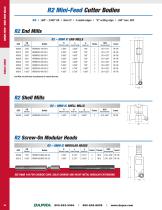
RHINO-FEED ™ HIGH-FEED MILLS R2 Mini-Feed Cutter Bodies R2 • .500” - 2.000” OD • 8mm IC • 3 usable edges • “D” cutting edge • .030” max. DOC Effective Length Overall Length End Mills are solid steel, manufactured for coolant thru tool. Effective Length R2 Screw-On Modular Heads R2 – 8MM IC MODULAR HEADS EDP Effective Length Overall Length Flutes Thread
Open the catalog to page 3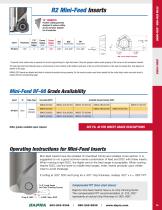
“D” INSERTS Positive cutting geometry designed to reduce cutting forces and heat. Suitable for all materials. T Corner Radius Corner Radius RHINO-FEED ™ HIGH-FEED MILLS * A special corner radius value is required for correct programming of a high-feed insert. Using the program radius avoids gouging of the corners in the workpiece material. The high-feed insert will naturally leave a small amount of extra material at the bottom-most layer of the cut, at the intersection of the wall and pocket floor. See diagram at bottom of this page. RHINO-FEED inserts are labeled with dots to indicate die...
Open the catalog to page 4
RHINO-FEED ™ HIGH-FEED MILLS R3 Mid-Feed Cutter Bodies R3 • 1.000” - 3.000” OD • 10mm IC • 4 usable edges • “T,” “D” or “F” cutting edge • .045” max. DOC Effective Length Overall Length End Mills are solid steel, manufactured for coolant thru tool. Effective Length Shell Mills are solid steel, manufactured for coolant thru tool. R3 Screw-On Modular Heads R3 – 10MM IC MODULAR HEADS EDP Effective Length Overall Length Flutes Thread Modular Heads are solid steel, manufactured for coolant thru tool
Open the catalog to page 5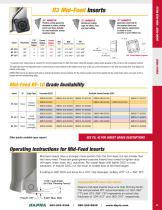
Left right: T, T, D Left to to right: N, N, D (Available in grade DMK30 only). Corner Radius Corner Radius “F” INSERTS Specially reinforced for the heaviest feeds and most abusive applications in steels or irons. “T” INSERTS Reinforced cutting edge for steels, irons and hard milling. .105” Corner Radius (Program) .190” * A special corner radius value is required for correct programming of a high-feed insert. Using the program radius avoids gouging of the corners in the workpiece material. The high-feed insert will naturally leave a small amount of extra material at the bottom-most layer of...
Open the catalog to page 6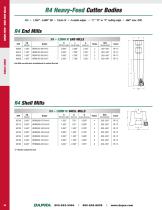
RHINO-FEED ™ HIGH-FEED MILLS R4 Heavy-Feed Cutter Bodies R4 • 1.250” - 6.000” OD • 12mm IC • 4 usable edges • “T,” “D” or “F” cutting edge • .060” max. DOC Effective Length Overall Length End Mills are solid steel, manufactured for coolant thru tool. Effective Length
Open the catalog to page 7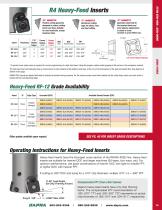
Left right: T, T, D Left to to right: N, N, D “F” INSERTS Specially reinforced for the heaviest feeds and most abusive applications in steels or irons. “T” INSERTS Reinforced cutting edge for steels, irons and hard milling. (Available in grade DMK30 only). Corner Radius Corner Radius .135” Corner Radius (Program) .220” * A special corner radius value is required for correct programming of a high-feed insert. Using the program radius avoids gouging of the corners in the workpiece material. The high-feed insert will naturally leave a small amount of extra material at the bottom-most layer of...
Open the catalog to page 8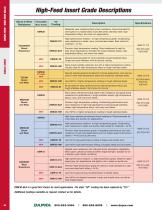
RHINO-FEED ™ HIGH-FEED MILLS High-Feed Insert Grade Descriptions Shock & Wear Resistance Uncoated (Base Grade) Moderate wear resistance/high shock resistance. Recommended for interrupted or unstable steel, most 300 series stainless steel, hightemperature alloys, and cast iron applications. High-performance medium- to high-temperature grade. Outstanding wear resistance in steels, irons, and stainless steels. Best suited for materials < 44 Rc. Premium high-temperature coating. Good resistance to heat for high-shock applications. Excellent for tough stainless steels, hightemperature alloys,...
Open the catalog to page 9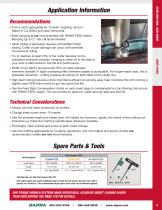
RHINO-FEED ™ HIGH-FEED MILLS Application Information Recommendations • ool is most appropriate for “Z-level” roughing; ramp to T Depth of Cut (DOC) and clear entire level. • olid plunging is not recommended with RHINO-FEED inserts. S Ramping (up to 2° max.) is recommended. • ry to maintain at least 75% of the cutter diameter on the T workpiece whenever possible. Hanging a cutter off to the side of your work is detrimental to tool life and performance. • idth of Cut (WOC) should be 60-75% of cutter diameter W whenever possible. A slight scalloping effect between passes is acceptable. For...
Open the catalog to page 10All Dapra Milling Solutions catalogs and technical brochures
-
Single-Sided Toroid Series
23 Pages
-
High Feed Indexable Milling
12 Pages
-
EXTREMEMetal Removal
25 Pages