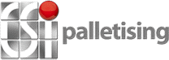

Catalog excerpts
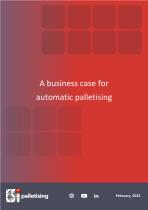
Remote service Providing service anytime, anywhere, A business case for anyway automatic palletising [Type here]
Open the catalog to page 1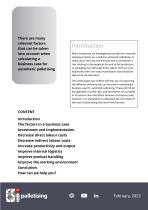
There are many relevant factors that can be taken into account when calculating a business case for automatic palletising Introduction Many companies are investigating moving from manually stacking products on a pallet to automatic palletising. In many cases, the only cost element that is considered is that relating to the people at the end of the production or packaging line. Although direct labour costs are very important, there are many more factors that should be taken into consideration. This white paper was written with the aim of presenting the different elements that can be used in...
Open the catalog to page 2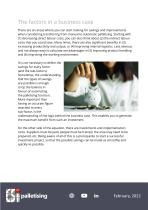
The factors in a business case There are six areas where you can start looking for savings and improvements when considering transferring from manual to automatic palletising. Starting with (1) decreasing direct labour costs, you can also think about (2) the indirect labour costs that you could save. Many times, there are also significant benefits in (3) increasing productivity and output, or (4) improving internal logistics. Less obvious and not always easy to calculate are advantages in (5) improving product handling and (6) improving the working environment. It is not necessary to define...
Open the catalog to page 3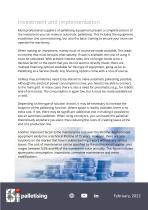
Investment and implementation Most professional suppliers of palletising equipment present a complete picture of the investment you can make in automatic palletising. This includes the equipment, installation and commissioning, but also the basic training to ensure your team can operate the machinery. When making an investment, money must of course be made available. This leads to interest that must be paid. Alternatively, if cash is available, the cost of using it must be calculated. With present interest rates, this no longer tends to be a decisive factor. In the event that you do not...
Open the catalog to page 4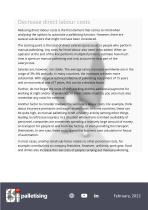
Decrease direct labour costs Reducing direct labour costs is the first element that comes to mind when analysing the options to automate a palletising function. However, there are several sub-factors that might not have been considered. The starting point is the total of direct salaries (gross) paid to people who perform manual palletising. Any costs for hired labour also need to be added. When an operator at the end of the line performs multiple functions, estimate how much time is spent on manual palletising and only account for that part of the salary/costs. Salaries are, however, not...
Open the catalog to page 5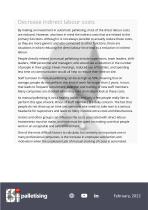
Decrease indirect labour costs By making an investment in automatic palletising, most of the direct labour costs are reduced. However, also bear in mind the indirect costs that are related to the primary functions. Although it is not always possible to actually reduce these costs, as they are more generic and also connected to other functions, there are situations in which reducing the direct labour force lead to a reduction in indirect labour. People directly related to manual palletising include supervisors, team leaders, shift leaders, HRM personnel and managers, who would see a...
Open the catalog to page 6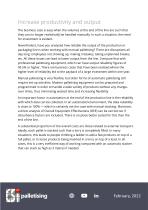
Increase productivity and output The business case is easy when the volumes at the end of the line are such that they can no longer realistically be handled manually. In such a situation, the need for investment is evident. Nevertheless, have you analysed how reliable the output of the production or packaging line is when working with manual palletising? There are disruptions all day long: employees not showing up, making mistakes, taking unplanned breaks, etc. All these issues can lead to lower output from the line. Compare that with professional palletising equipment, which can have...
Open the catalog to page 7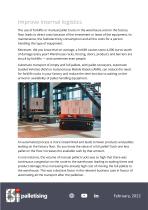
Improve internal logistics The use of forklifts or manual pallet trucks in the warehouse and on the factory floor leads to direct costs because of the investment or lease of the equipment, its maintenance, the fuel/electricity consumption and all the costs for a person handling this type of equipment. Moreover, did you know that on average, a forklift causes some 4,000 euros worth of damage every year? Warehouse racks, fencing, doors, products and barriers are struck by forklifts — and sometimes even people. Automatic transport of empty and full pallets, with pallet conveyors, Automatic...
Open the catalog to page 8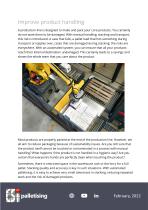
Improve product handling A production line is designed to make and pack your core products. You certainly do not want them to be damaged. With manual handling, stacking and transport, this risk is introduced. A case that falls, a pallet load that hits something during transport or topples over, cases that are damaged during stacking: the risks are everywhere. With an automated system, you can ensure that all your products reach their internal destination undamaged. This certainly leads to a savings and shows the whole team that you care about the product. Most products are properly packed...
Open the catalog to page 9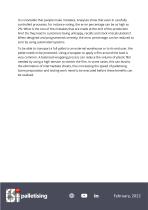
It is inevitable that people make mistakes. Analyses show that even in carefully controlled processes, for instance voting, the error percentage can be as high as 2%. What is the cost of the mistakes that are made at the end of the production line? Do they lead to customers being unhappy, recalls and stock miscalculations? When designed and programmed correctly, the error percentage can be reduced to zero by using automated systems. To be able to transport a full pallet to an external warehouse or to its end user, the pallet needs to be protected. Using a wrapper to apply a film around the...
Open the catalog to page 10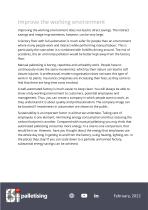
Improve the working environment Improving the working environment does not lead to direct savings. The indirect savings and image improvements, however, can be very large. A factory floor with full automation is much safer for people than an environment where many people work and interact while performing manual labour. This is particularly the case when it is combined with forklifts driving around. The risk of accidents, the air and noise pollution would be better kept away from the factory floor. Manual palletising is boring, repetitive and unhealthy work. People have to continuously make...
Open the catalog to page 11All CSi industries BV catalogs and technical brochures
-
Leasing palletising equipment
10 Pages
-
Remote service
9 Pages
-
AGV versus AMR
6 Pages
-
Sustainability
1 Pages