
Catalog excerpts
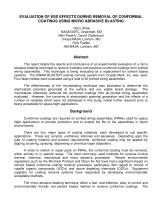
EVALUATION OF ESD EFFECTS DURING REMOVAL OF CONFORMAL COATINGS USING MICRO ABRASIVE BLASTING Harry Shaw NASA/GSFC, Greenbelt, MD Nitin Parekh, Carroll Clatterbuck Unisys/NASA, Lanham, MD Felix Frades HEI/NASA, Lanham, MD Abstract This report details the results and conclusions of an experimental evaluation of a micro abrasive blasting technique to remove urethane and parylene conformal coatings from printed wiring assemblies. This technique is being evaluated as a replacement for solvent based systems. The SWAM BLASTER coating removal system from Crystal Mark, Inc. was used. Four blast medias were evaluated using a total of 20 printed wiring assemblies. The effectiveness of the microblasting technique was evaluated to determine the electrostatic potential generated at the surface and any visible board damage. The microblaster effectively removed the conformal coatings from all printed wiring assemblies evaluated. However, the concerns of electrostatic potential generation and the effects of a number of variables which were not addressed in this study, needs further research prior to being acceptable for space flight applications. Background Conformal coatings are required on printed wiring assemblies (PWAs) used for space flight applications to provide protection and to extend the life of the assemblies in harsh environments. There are four major types of coating materials, each developed to suit specific applications. These are: acrylics, urethanes, silicones and parylenes. Depending upon the type of coating material and product requirements, conformal coating may be applied by dipping, brushing, spraying, dispensing or chemical vapor deposition. In order to rework or repair parts on PWAs, the conformal coating must be removed, either entirely or in specific areas. The most commonly used methods for removal involve thermal, chemical, mechanical and micro abrasive processes. Recent environmental regulations such as the Montreal Protocol and Clean Air Act have had a significant impact on solvent based conformal coating removal processes, particularly with regard to control of volatile organic compounds (VOCs) and ozone depleting chemicals (ODCs). Equipment suppliers for coating removal systems have responded by developing environmentally acceptable methods. The micro abrasive blasting technique offers a fast, cost-effective, easy to control and environmentally friendly non-solvent based method to remove conformal coatings. The
Open the catalog to page 1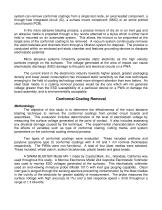
system can remove conformal coatings from a single test node, an axial leaded component, a through-hole integrated circuit (IC), a surface mount component (SMC) or an entire printed circuit board (PCB). In the micro abrasive blasting process, a precise mixture of dry air or an inert gas and an abrasive media is propelled through a tiny nozzle attached to a stylus which is either hand held or mounted on an automated system. This allows the mixture to be pinpointed at the target area of the conformal coating to be removed. A vacuum system continuously removes the used materials and channels...
Open the catalog to page 2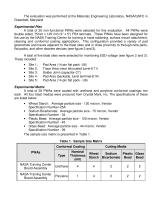
The evaluation was performed at the Materials Engineering Laboratory, NASA/GSFC in Greenbelt, Maryland. Experimental Plan A total of 20 non-functional PWAs were selected for this evaluation. All PWAs were double sided, 75mm x 125 mm (3" x 5") FR4 laminate. These PWAs have been designed for the use by the NASA Training Center for training in hand soldering, surface mount attachment, cleaning and conformal coating applications. This configuration provided a variety of pad geometries and traces adjacent to the blast sites and in close proximity to through-hole parts, flat packs, and other...
Open the catalog to page 3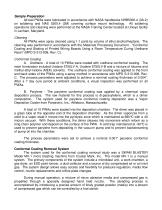
Sample Preparation All test PWAs were fabricated in accordance with NASA handbooks NHB5300.4 (3A-2) on soldering and NAS 5300.4 (3M) covering surface mount technology. All soldering operations and cleaning were performed at the NASA Training Center located at Unisys facility in Lanham, Maryland. Cleaning All PWAs were spray cleaned using 1:1 parts by volume of ethyl alcohol/heptane. The cleaning was performed in accordance with the Materials Processing Document - "Conformal Coating and Staking of Printed Wiring Boards Using a Room Temperature Curing Urethane Resin" (MPD S-313-008, Rev. C)....
Open the catalog to page 4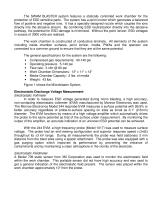
The SWAM BLASTER system features a statically controlled work chamber for the protection of ESD sensitive parts. The system has a point ionizer which generates a balanced flow of positive and negative ions. It has a specially designed nozzle which couples the ions directly into the abrasive stream. By combining ESD neutralization directly into the abrasive pathway, the potential for ESD damage is minimized. Without the point ionizer, ESD voltages in excess of 3000 volts are realized. The work chamber is constructed of conductive laminate. All elements of the system including inside chamber...
Open the catalog to page 5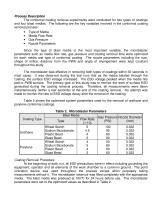
Process Description The conformal coating removal experiments were conducted for two types of coatings and four blast medias. The following are the key variables involved in the conformal coating removal process: • Type of Media • Media Flow Rate • Gas Pressure • Nozzle Parameters Since the type of blast media is the most important variable, the microblaster parameters such as media flow rate, gas pressure and coating removal time were optimized for each media and type of conformal coating. The nozzle parameters including the size, shape of orifice, distance from the PWA and angle of...
Open the catalog to page 6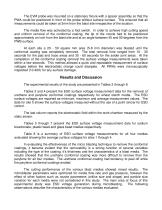
The EVM probe was mounted on a stationary fixture with a spacer assembly so that the PWA could be positioned in front of the probe without surface contact. This ensured that all measurements could be taken at 3mm from the blast site irrespective of the location. The media flow was activated by a foot switch. In order to achieve high cutting speed and uniform removal of the conformal coating, the tip of the nozzle had to be positioned approximately an inch from the blast site and at an angle between 45 and 90 degrees from the PWB surface. At each site a 20 - 50 square mm area (5-8 mm...
Open the catalog to page 7All Crystal Mark catalogs and technical brochures
-
Basic Equipment
1 Pages
-
Desiccant Air Dryers
2 Pages
-
Air Filter Dryers
1 Pages
-
The Point Ionizer System
1 Pages
-
Turbo Max
2 Pages
-
Conformal Coating Removal
1 Pages
-
The SWAM® Complete Work Cell
2 Pages
-
SWAM® Wire Abrading System
1 Pages
-
The Eco Blaster
1 Pages
-
Dust Collector Model 64 & 74
1 Pages
-
TURBO-station and TURBO-cab
1 Pages
-
Dust Collector Model DC100
1 Pages
-
SWAM-BLAST® All
1 Pages