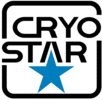

Catalog excerpts
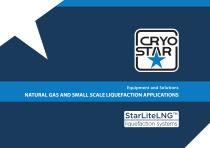
NATURAL GAS AND SMALL SCALE LIQUEFACTION APPLICATIONS
Open the catalog to page 1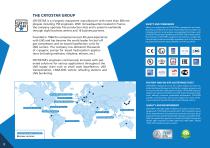
THE CRYOSTAR GROUP CRYOSTAR is a cryogenic equipment manufacturer with more than 600 employees including 150 engineers. With its headquarters located in France, the company operates five production sites and is present worldwide through eight business centers and 16 business partners. Founded in 1966 the company has over 40 years experience with LNG and has become the world leader for boil off gas compressors and on-board liquefaction units for LNG carriers. The company has delivered thousands of cryogenic pumps for liquid hydrocarbon applications (including methane, ethylene, ethane, etc.)...
Open the catalog to page 2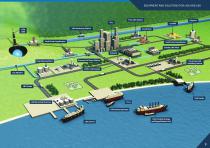
Small Scale Liquefaction Peak Shaving Plant Small Town Small Scale Liquefaction
Open the catalog to page 3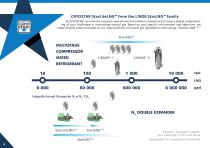
CRYOSTAR StarLiteLNG™ from the LINDE StarLNG™ family At CRYOSTAR, we have the requisite operational and industrial experience to have a global understanding of your challenges in monetizing natural gas. Based on your specific environment and objectives, we create flexible solutions based on our wide portfolio of natural gas liquefaction technology, "StarLite LNG TM." MULTISTAGE COMPRESSOR MIXED REFRIGERANT Integrally Geared Compander N or N / CH N0 DOUBLE EXPANDER StarLNGL StarLNG™ StarLNG™, StarLNGL™, LIMUM® are a trademark of The Linde Group. StarLite LNGTM is a trademark of CRYOSTAR.
Open the catalog to page 4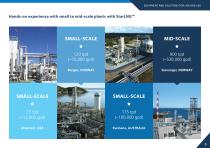
Hands-on experience with small to mid-scale plants with StarLNG™ Bergen, NORWAY Stavanger, NORWAY Kwinana, AUSTR
Open the catalog to page 5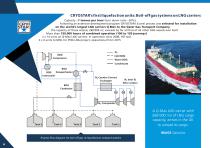
CRYOSTAR’s first liquefaction units: Boil-off gas systems on LNG carriers Capacity ~7 tonnes per hour (turn down ratio ~30%), Following an extensive development program CRYOSTAR’s Ecorel process was selected for installation on the world’s largest LNG carriers Q-Max to the Qatar Gas Transport Company. The capacity of these vessels, 266’000 m3, exceeds by far all that of all other LNG vessels ever built More than 150,000 hours of combined operation (100 to 120 journeys) 2 x 14 units on Q-Max LNG carriers. In operation since 2008, 187 tpd 2 x 4 units to MOL for PNG LNG project, operational...
Open the catalog to page 6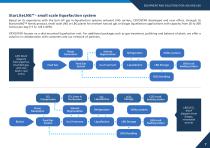
StarLiteLNG™ - small scale liquefaction system Based on its experience with the boil off gas re-liquefaction systems onboard LNG carriers, CRYOSTAR developed and now offers, through its StarLiteLNG™ family product, small scale LNG or LBG plants for onshore natural gas or biogas liquefaction applications with capacity from 20 to 200 tonnes per day (17 to 124 k GPD). CRYOSTAR focuses on a skid-mounted liquefaction unit. For additional packages such as gas treatment, polishing and balance of plant, we offer a solution in collaboration with customers and our network of partners. LNG block...
Open the catalog to page 7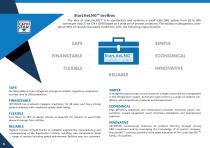
StarLiteLNG™ toolbox The idea of StarLiteLNG™ is to standardize and optimize a small scale LNG system from 20 to 200 tonnes per day (17 to 124 k GPD) based on a wide set of process variations. The toolbox is designed to cover about 90% of real-life boundary conditions, with the following major benefits: SAFE FINANCEABLE INNOVATIVE RELIABLE SAFE No flammable or toxic refrigerant storage for simpler regulatory compliance and less time to LNG production. A straightforward process control based on a single turbomachine (compander) in the refrigeration system. Automatic load control in a range...
Open the catalog to page 8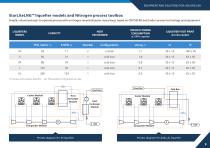
StarLiteLNG™ liquefier models and Nitrogen process toolbox Simple, robust and easy-to-operate process with a nitrogen reverse Brayton closed loop, based on CRYOSTAR and Linde‘s proven technology and equipment. LIQUEFIERS MODEL HEAT EXCHANGER SPECIFIC POWER CONSUMPTION at 100% capacity LIQUEFIER FOOT PRINT w/o Air coolers (1) Varies with project specifics Cooler Module Heat Exchanger Module Process diagram for XS liquefier Cooler Module Heat Exchanger Module Process diagram for S,M,L,XL liquefier
Open the catalog to page 9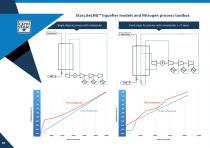
StarLiteLNG™ liquefier models and Nitrogen process toolbox Single stage N2 process with compander Dual stage N2 process with compander + JT valve Cold composite Cold composite 3000 HEAT FLOW KW TEMPERATURE °C
Open the catalog to page 10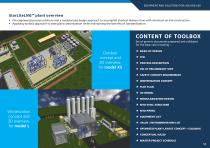
StarLiteLNG™ plant overview • Pre-engineered process solutions and a modularized design approach to accomplish shortest delivery time with minimum on-site construction. • Applying toolbox approach to ease plant customization while maintaining the benefits of standardization. Outdoor concept and 3D overview, for model XS Winterization concept and 3D overview, for model L CONTENT OF TOOLBOX Set of generic documents prepared and validated for the base case including : ★ BASIS OF DESIGN ★ PFD ★ PROCESS DESCRIPTION ★ PID AT PRELIMINARY STEP ★ SAFETY CONCEPT REQUIREMENT ★ WINTERIZATION CONCEPT ★...
Open the catalog to page 11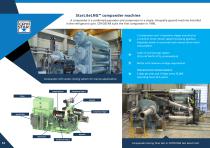
StarLiteLNG™ compander machine A compander is a combined expander and compressor in a single, integrally-geared machine installed in the refrigerant cycle. CRYOSTAR built the first compander in 1996. Motor with medium voltage requirement « Coupling Guard Lube oil and seal gas system (25 to 45 Nm3/h of N2 consumption) « Compander with water cooling system for marine applications 3 compression and 1 expansion stages mounted on a common motor driven speed increasing gearbox. Expander power is recovered and reduces drive motor consumption. PREVENTATIVE MAINTENANCE 2 days per year and 14 days...
Open the catalog to page 12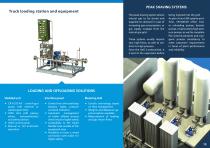
PEAK SHAVING SYSTEMS Truck loading station and equipment The peak shaving system allows natural gas to be stored and supplied on demand in case of increasing gas consumption, or gas supply outages from the natural gas grid. These systems usually require very high flows, as well as medium to high pressure. Once the LNG is pressurized, it is sent to the vaporizers before being injected into the grid. As part of our LNG systems portfolio, CRYOSTAR offers trailer unloading pumps, booster pumps, reciprocating high pressure pumps, as well as complete PLC controls solutions and cryogenic process...
Open the catalog to page 13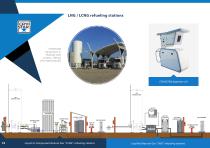
LNG / LCNG refueling stations CRYOSTAR equipment in Rolande LNG station, Tilburg (The Netherlands) Boil off gas managment system HIGH PRESSURE VAPORIZER BUFFER PANEL RECIPROCATING PUMP Ve nt HEATER gdidgyitgdqigdsIGyi gsIHCQKGCKGQC CONTROL PANEL (safe area) Liquid to Compressed Natural Gas ‘’LCNG’’ refueling stations ELECTRICAL CONTROL PANEL Liquid Natural Gas « LNG » refueling stations stations Liquified Natural Gas “LNG” refueling
Open the catalog to page 14All Cryo Star catalogs and technical brochures
-
Vertical Sealess VS
2 Pages
-
HYDROCARBON-TURBO_EXPANDERS
20 Pages
-
CRYOGENIC RECIPROCATING PUMPS
16 Pages
-
CRYOGENIC TRANSFER PUMPS
13 Pages
-
CO 120
2 Pages
-
Transfer Pump CBS
2 Pages
-
Transfer Pump CS
2 Pages
-
Automatic Line System
2 Pages
-
CVI PD 3000
2 Pages
-
CCI GSV
2 Pages
-
CCI LXR 1000
2 Pages
-
Reciprocating Pump PPC
2 Pages
-
Transfer Pump GBS
2 Pages
-
SUBTRAN
2 Pages