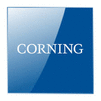
Gravure printing of conductive inks on glass substrates for applications in printed electronics
1 /
1Pages
Catalog excerpts
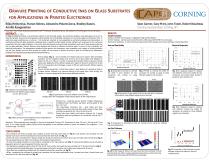
Printing design (Fig. 1) - set of meander line resistors that were used for both printability evaluation and DC resistance testing. Test structure line (trace) widths were designed to range from 50 m to 500 m. In order to evaluate directionality effects of gravure printing, traces were designed at three different angles with respect to the print direction (0, 45 and 90°). For the evaluation of printed gaps, a group of 500 µm wide lines with different spacing was included. Gravure cylinder preparation - indirect laser method - laser ablation of a protective mask on a copper surface, followed by a chemical etching of the copper layer. After etching, the cylinder is chromium plated and finished using traditional methods. Sample evaluation: Quality of printed lines and gaps - ImageXpert Image Analysis System. Ink film thickness - vertical scanning interferometry (VSI) using a WYKO RST-Plus microscope. Electrical DC resistance - 2 point probe local measurement with standard ohm-meter settings on the Keithley 2602. Electrical Properties Silver Nanoparticle Ink Silver Nanoparticle Ink Silver Flake Ink Silver Flake Ink 0.1 0.2 0.3 0.4 0.1 0.2 0.3 0.4 Nominal Line Width [mm] Nominal Line Width [mm] Fig. 4 Comparison of printed vs. nominal line width in print direction for two conductive inks printed on glass substrate. Printed Line Width [mm] Printed Line Width [mm] sheet fed presses. Gravure printing typically employs flexible and compressible substrates such as various papers and polymer films. In electronics, glass substrates are a common, if not preferred, substrate in many applications, particularly displays and photovoltaics. In combining printing with glass substrates, challenges exist in adapting contact-based printing methods such as gravure to the mechanical properties of the more rigid substrates. In this work, sheet-fed gravure printing has been successfully used to print silver-based conductive inks on glass substrates. Various features were designed and printed to evaluate conductive layers in terms of their printability and electrical performance. The independent variables include gravure cell dimensions, trace orientation with respect to printing direction and ink type. Results from this work provide an insight into the science of gravure printing on glass by correlating the independent variables to printed feature quality and electrical performance. Sean Garner, Gary Merz, John Tosch, Robert Boudreau Corning Incorporated, Corning, NY Printed Line Width [mm] Printed Line Width [mm] Erika Hrehorova, Marian Rebros, Alexandra Pekarovicova, Bradley Bazuin, Amrith Ranganathan Center for the Advancement of Printed Electronics, Western Michigan University, ABSTRACT Kalamazoo, MI In graphics, gravure printing is the preferred method for printing high quality, fine dimension graphics using high-speed roll-to-roll or 0.2 0.3 0.4 0.5 0.2 0.3 0.4 0.5 Nominal Line Width [mm] Nominal Line Width [mm] Fig. 5 Printed vs. nominal line width for nanosilver ink printed on glass at three different angles to print direction. Nanosilver Ink Nanosilver Ink Silver Flake Ink Silver Flake Ink 0.1 0.15 0.2 0.1 0.15 0.2 Nominal Line Width [mm] Nominal Line Width [mm] Fig. 8 DC resistance values for resistors with different nominal line widths for two conductive inks printed (lines printed in parallel to print direction, 0°). Fig. 1 Section of printing design (meander lines and lines with different spacing (gaps) at 0, 45, 90° to print). Fig. 6 Comparison of gap quality of 50 µm nominal gap for nanosilver ink printed at three different angles to print direction. Fig. 2 Engraving for traces with different nominal width. (Images taken with ImageXpert Image Analysis System at 40x magnification) Fig. 3 Basic principle and arrangement of the components for gravure printing. Printing trial - sheet-fed gravure proofer, Prüfbau Rotogravure Printability Tester (by Prüfbau, Germany); printing speed of 250 fpm (1.27 m/s). Two silver-based conductive inks - silver flakes and silver nanoparticles as the conductive filler (solids content of silver flake and silver nanoparticle inks - 80 wt.% and 40 wt.%). Printed inks were initially cured using a heat-gun for 1 minute followed by post-curing treatment in a convection oven at 120 °C for 10 min. Substrate - Glass substrates were supplied by Corning Incorporated (Corning, NY). Dimensions of were 110 mm x 310 mm and 0.7 mm thick. A UV curable acrylate coating (<10 m thick) was applied to the substrate surface to ensure ink adhesion (Ra roughness 1 nm, Surface energy 50 mN/m). Nominal Line Width [mm] Nominal Line Width [mm] moat cell Fig. 9 DC resistance values for resistors with different nominal line widths for nanosilver ink printed at three different angles to print direction. Fig. 7 Comparison of printability of 200 µm nominal line by using two different engraving approaches. CONCLUSIONS qThe nanosilver ink tends to spread more resulting in wider lines than silver flake ink (Fig. 4). Lines printed with nanosilver ink also showed much lower ink film thicknesses than those printed with silver flake ink (Fig. 11). qThere was more ink transferred for 100 µm (single row of gravure cells) than for 150 µm (two rows of smaller cells) nominal lines (Fig. 2). This was supported by line width, line thickness, and resistance measurements. qIf moat surrounding the pattern to be printed is connected to the main gravure cells (Fig. 7), improved printability can be achieved as opposed to when the moat is separated from the main cells. qThe highest line spreading was found for 90° then for 45° lines, and the narrowest lines were printed at 0° to the print direction (Fig. 5). qAmong printed and measurable gaps, the narrowest gaps printed with nanosilver ink on glass were measured as 36 ± 8 µm. qSilver flake ink consistently provided lower DC resistance values than nanosilver ink (Fig. 8). qWhen considering the thickness of printed lines, nanosilver ink has better applicability since it printed more than 4 times thinner and smoother ink film than silver flake ink (Fig. 10). Fig. 10 The 3D images of 100 µm nominal line printed with nanosilver ink (left) and silver flake ink (right) on glass substrate (measured by a vertical scanning interferometry (VSI) using a WYKO RST-Plus microscope). Fig. 11 Comparison of line thickness range for different nominal line widths for the two conductive inks.
Open the catalog to page 1All CORNING Display Technologies catalogs and technical brochures
-
Gorilla® Glass 5
2 Pages
-
Corning Iris®
2 Pages
-
Aspheres by Corning
2 Pages
-
UltraFlat™
2 Pages
-
Tropel® FlatMaster® MSP
2 Pages
-
Optical Solutions
4 Pages
-
EAGLE XG® Slim
2 Pages
-
Scoring of AMLCD Glass
4 Pages
Archived catalogs
-
Jade® Product Information Sheet
3 Pages
-
Jade® Material Information Sheet
2 Pages