
Catalog excerpts
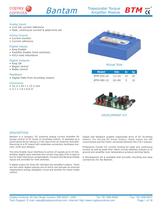
Bantam Trapezoidal Torque Amplifier Module BTM RoHS Analog Inputs • ±10 Vdc current reference • Peak, continuous current & peak-time set Analog Outputs • Current monitor • Current reference Digital Inputs • Amp Enable • Fwd/Rev Enable (limit switches) • Hi/Lo load inductance Digital Outputs • Amp OK • Regen control • Brake control Feedback • Digital Halls from brushless motors Dimensions • 53.3 x 45.7 x 15.2 mm • 2.1 x 1.8 x 0.6 in Actual Size Model Vdc Ic Ip BTM-055-20 12~55 10 20 BTM-090-10 20~90 5 10 DEVELOPMENT KIT DESCRIPTION Bantam is a compact, DC powered analog current amplifier for torque control of DC brush or brushless motors. It operates as a stand-alone driver taking a ±10V input from an external controller. Mounting to a PC board with solderless connectors facilitates lowcost, multi-axis designs. The Amp Enable input interfaces to active LO signals up to 24 Vdc. Another digital input switches the current-loop gain from a high to low for load inductance compensation. Forward and Reverse Enable inputs are provided for limit switches. Digital Hall feedback enables trapezoidal drive of DC brushless motors. For driving DC brush motors, these inputs are left unconnected and the motor connected between the U & V outputs. Protections include I2T current limiting for peak and continuous current as well as peak time. Short circuits between outputs or to ground and amplifier over-temperature produce latching faults. A Development Kit is available that provides mounting and easy connectivity for the Bantam. A digital output for Amp-OK indicates the amplifier’s status. There are two other digital outputs one of which can activate an external regenerative energy dissipator circuit and another for motor brake control. Copley Controls, 20 Dan Road, Canton, MA 02021, USA Tel: 781-828-8090 Tech Support: E-mail: sales@copleycontrols.com, Internet: http://www.copleycontrols.com Fax: 781-828-6547 Page 1 of 18
Open the catalog to page 1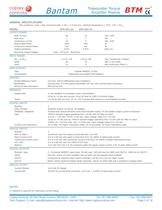
Bantam Trapezoidal Torque Amplifier Module BTM RoHS GENERAL SPECIFICATIONS Test conditions: Load = Wye connected load: 2 mH + 2 Ω line-line. Ambient temperature = 25°C, +HV = HVmax MODEL BTM-055-20 BTM-090-10 Peak Current Peak time Continuous current Peak Output Power Continuous Output Power Output resistance 20 1 10 1045 523 0.075 10 1 5 855 427 0.075 Maximum Output Voltage Vout = HV*0.97 - Rout*Iout OUTPUT POWER Adc, ±5% Sec Adc, ±5% W W Rout (Ω) INPUT POWER HVmin to HVmax Ipeak Icont +12 to +55 20 10 +20 to +90 10 5 Vdc, Transformer-isolated Adc (1 sec) peak Adc continuous (Note 1) PWM...
Open the catalog to page 2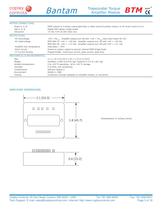
Bantam Trapezoidal Torque Amplifier Module BTM RoHS MOTOR CONNECTIONS Phase U, V, W Hall U, V, W Hall power PWM outputs to 3-phase ungrounded Wye or delta wound brushless motors, or DC brush motors (U-V) Digital Hall signals, single-ended +5 Vdc ±2% @ 250 mAdc max PROTECTIONS HV Overvoltage HV Undervoltage Amplifier over temperature Short circuits I2T Current limiting +HV > HVmax, Amplifier outputs turn off until +HV < HVmax (See Input Power for HV) BTM-090-10: +HV < +20 Vdc, Amplifier outputs turn off until +HV > +20 Vdc BTM-055-20: +HV < +12 Vdc, Amplifier outputs turn off until +HV > +12...
Open the catalog to page 3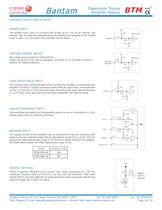
Bantam BTM Trapezoidal Torque Amplifier Module RoHS CONTROL INPUTS AND OUTPUTS ENABLE INPUT +5V The Enable input [IN1] is LO-active and pulled up to +5V by an internal 10k resistor. This provides fail-safe operation by disabling the amplifier if the Enable input is open, or a wire from the controller should break. 10k /Enable 74HC2G14 J1-18 10k 1nF FWD/REV ENABLE INPUTS +5V Two inputs are provided for limit switches. These should be LO for normal operation, and open or HI to inhibit current of positive or negative polarity. /PosEnab /NegEnab 10k J1-19 J1-20 74HC2G14 10k 1nF LOAD INDUCTANCE...
Open the catalog to page 4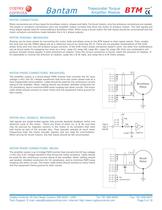
Bantam BTM Trapezoidal Torque Amplifier Module RoHS MOTOR CONNECTIONS Motor connections are of two types for brushless motors: phases and Halls. For brush motors, only the armature connections are needed. The phase or armature connections carry the amplifier output currents that drive the motor to produce motion. The Hall signals are three digital signals used for commutating a brushless motor. When using a brush motor the Hall inputs should be unconnected and the motor armature connections made between the U & V phase outputs. MOTOR PHASING: BRUSHLESS Phasing can be done simply by...
Open the catalog to page 5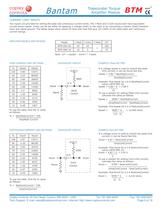
Bantam Trapezoidal Torque Amplifier Module BTM RoHS CURRENT LIMIT INPUTS Two inputs are provided for setting the peak and continuous current limits. The I-Peak and I-Cont inputs each have equivalent circuits shown below. Limits can be set either by applying a voltage (Vset) to the input or by connecting a resistor (Rset) between input and signal ground. The tables below show values for Rset and Vset that give 10~100% of the rated peak and continuous current ratings. AMPLIFIER MODELS AND RATINGS Model I-Peak I-Cont BTM-055-20 20 10 BTM-090-10 10 T-Peak 5 1 I2T 300 75 Note: I2T = (Ipeak2 -...
Open the catalog to page 6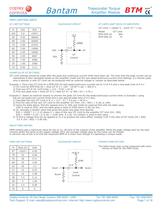
Bantam Trapezoidal Torque Amplifier Module BTM RoHS PWM LIMITING INPUT I2T LIMIT SETTINGS I2T LIMITS (AMP2·SECS) OF AMPLIFIERS EQUIVALENT CIRCUIT % Vi2t 100 5.0 90 4.50 90000 80 4.00 40000 70 3.50 23333 60 3.00 15000 50 2.50 10000 40 2.00 6667 30 1.50 4286 20 1.00 2500 10 0.50 I2T Limit = (Ipeak^2 - Icont^2) * 1 sec Ri2t 1111 Model I2T Limit BTM-055-20 300 BTM-090-10 75 +5 V 10000 J1-2 Vi2t I2T I2T Control Ri2t EXAMPLES OF I2T SETTINGS I2T Limit settings should be made after the peak and continuous current limits have been set. The time that the peak current can be maintained is then...
Open the catalog to page 7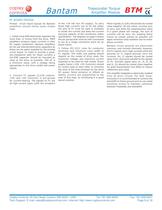
Bantam Trapezoidal Torque Amplifier Module BTM RoHS PC BOARD DESIGN Printed circuit board layouts for Bantam amplifiers should follow some simple rules: 1. Install a low-ESR electrolytic capacitor not more than 12 inches from the drive. PWM amplifiers produce ripple currents in their DC supply conductors. Bantam amplifiers do not use internal electrolytic capacitors as these can be easily supplied by the printed circuit board. In order to provide a good, low-impedance path for these currents a low-ESR capacitor should be mounted as close to the drive as possible. 330 µF is a minimum value,...
Open the catalog to page 8All Copley Controls catalogs and technical brochures
-
XenusPLUS Compact EtherCAT XEC
30 Pages
-
XenusPLUS Compact CANopen XPC
30 Pages
-
Control Networks
8 Pages
-
R-Series Guide
8 Pages
-
Selection Guide
24 Pages
-
Xenus R10
30 Pages
-
Accelnet R23
24 Pages
-
Accelnet R22
22 Pages
-
Accelnet R21
24 Pages
-
Accelnet R20
24 Pages
-
Accelus Card Development Kit
6 Pages
-
Accelus Card
8 Pages
-
ASP-X2 Accelus Panel Dual
10 Pages
-
Junus
10 Pages
-
CAN-PCI-02
2 Pages
-
CAN-IPM-01
8 Pages
-
Bantam R30
18 Pages
-
503
6 Pages
-
Power Supply Subsystem
8 Pages
-
Shunt Regulator
2 Pages
-
Xenus PLUS 2-Axis CANopen
34 Pages
-
Xenus RoHS PLUS CANopen
28 Pages
-
Xenus PLUS 2-Axis EtherCAT
34 Pages
-
Xenus PLUS EtherCAT
28 Pages
-
Xenus Edge Filter
16 Pages
-
Regen Resistors
24 Pages
-
Xenus Micro
24 Pages
-
Accelus Card Development Kit
6 Pages
-
Accelus Card
8 Pages
-
Accelus Panel
10 Pages
-
Xenus XTL
30 Pages
-
Accelnet Plus EtherCAT Panel
18 Pages
-
Accelnet Micro Module and Kit
24 Pages
-
Accelnet Micro Panel
24 Pages
-
Accelnet Module Development Kit
8 Pages
-
Accelnet Module
14 Pages
-
Accelnet Panel ADP
24 Pages