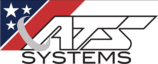
Catalog excerpts
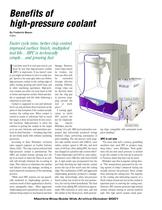
By Frederick Mason Editor f you have used it or even just seen it, youknow by now that high-pressure coolant(HPC) is impressive. If you havent seenit, you might not believe it, but it is really sim-ple. Speed is the main gain when you deliverhigh-pressure coolant to the cutting edge ofdrills, turning, grooving and cutoff tools, andin other machining operations. High-pres-sure coolant can often cut cycle times in halfor better and improve surface finish and dou-ble or quadruple tool life while delivering areduction in cycle time . Coolant is supposed to cool and lubricatebut it can only perform these functions at thepoint of chip formation if the coolant actuallyreaches the cutting zone. When coolant isturned to steam or otherwise fails to reachthe target, it does not perform its two essen-tial functions. High-pressure is often thesolution to getting the coolant to the targetso it can cool, lubricate, and sometimes per-form its third function җ breaking chips thatdo not break neatly with ordinary machiningprocesses.According to Dave Whittaker, technicalsales support engineer at CoolJet Systems(Brea, Calif), The chip control achieved withhigh-pressure coolant is phenomenal. The1000+ psi coolant stream, ejecting over thetip of an insert or down the flutes of an end-mill, will virtually eliminate the re-cutting ofchips. This reduces or eliminates the randomtool failures from chip damage, resulting inmuch improved consistency of the machiningprocess.ӓWhile most HPC systems are not specifi-cally marketed as chipbreaking systems, acommon result of their application is shorter,more manageable chips.More aggressivechipbreaking insert geometries may be used,without being subject to mechanical and heat damage. However,some chips cannotbe broken, butthey can often stillbe controlledthrough effectivenozzling. Difficult,stringy chips canbe directed downinto the chip panto prevent wrap-ping around thetool or work-piece.ŔA turning appli-cation in whichHPC proved thekey for chipbreak-ing, reportsWhittaker, was theturning of a soft, 1008 steel automotive com-ponent that historically produced stringybirdnest chips, preventing automation ofparts handling. The old process used nega-tive rake carbide inserts with 0.060-in. noseradius, surface speed to 500 sfm, and feedrates of 0.015 ipr. After adding HPC, the insertwas changed to a positive rake cermet with F-F style chipbreaker and 0.015-in. nose radius.Parameters were 1500 sfm, with feed of 0.010ipr. A rigid nozzle was incorporated into thetool body directing the high velocity coolantacross the top of the insert onto the cuttingedge. The combination of HPC and aggressivechipbreaking geometry produced a manage-able chip. Interestingly, when low-pressureflood coolant was tested at the new parame-ters, the tool tip failed immediately. The finalresults from adding HPC achieved an approx-imate 50% reduction in cycle time, and toollife similar to the old process, while generat- ing chips compatible with automated work-piece handling.Ӕ HPC is not new For more than half a century, gundrillingmachines have used HPC to produce long,deep holes,Ӕ notes Whittaker. Their guide-lines tell you how much pressure is neededto get the coolant to the tool tip to preserveit. Pressure above that does not do much.Whittaker says that in popular cutting theo-ry, The temperatures generated by the cut-ting speeds of todayӒs advanced tooling canactually prevent low-pressure flood coolantfrom entering the cutting zone. The majorityof the cooling and lubricating aspects of aflood coolant stream are lost as the coolant isvaporized prior to entering the cutting zone.However, HPC systems generate high velocitycoolant streams moving at several hundred mph. This high speed coolant easily pene- > Machine Shop Guide Web Archive-October 2001 size="-1">
Open the catalog to page 1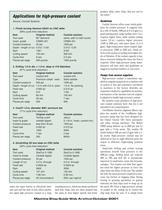
Source: CoolJet Systems > 1. Finish turning titanium 6Al4V on CNC lathe (68% cycle time reduction) ItemOriginal methodCoolJet solution Tool used80 diamondsame, add CJ ball nozzleInsert, gradeCNMG 431CNMG 431Coolant pressure45 psi1000 psiDepth / length of cut 0.012 / 0.500.012 / 0.50Rpm13612722Cutting speed 150 sfm300 sfmCycle time8 sec2.5 secPieces per edge500 pcs/tip1000 pcs/tip 2. Drilling 1/2-in dia. x 1.5-in. deep in 416 Stainless (81% cycle time reduction) ItemOriginal methodCoolJet solution Tool usedcoolant drillcoolant drillTypePremium cobalt - twistSolid carbideCoolant pressure200...
Open the catalog to page 2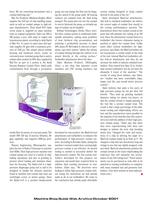
force. We are converting horsepower into acoolant battering ram.Mar-Tec Products (Madison Heights, Mich)supplies the full line of chip handling equip-ment as well as coolant pumps to high-vol-ume manufacturers. Their Knoll KTS triplescrew pump is supplied on many machinetools as original equipment. Sales are 300 to500 pumps a year, with many to engine andtransmission plants, according to Andy Hatchof Mar-Tec. It comes in many sizes and typi-cally supplies 92 gpm with a maximum pres-sure of 1438 psi. The unique silicon carbidehousing and hardened rotors create anextremely wear-resistant pump...
Open the catalog to page 3All ATS Systems catalogs and technical brochures
-
70-36
1 Pages
-
70-30
1 Pages
-
L8-1000
1 Pages
-
UltraFlex
4 Pages
-
Mist Collection
1 Pages
-
CoolMag Machine Tool Filter
2 Pages
-
CoolMag Pre-Filter
2 Pages
-
CoolMag
2 Pages
-
Coolant Chillers
2 Pages
-
L8-1000 high pressure unit
1 Pages
-
The Skinny on Microdrilling
4 Pages