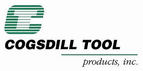
Catalog excerpts
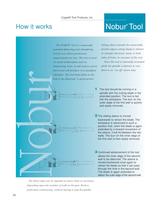
Cogsdill Tool Products, Inc. Nobur Tool How it works ® The NOBUR® Tool is a manually sliding sleeve extends the retractable, actuated deburring and chamfering double-edged cutting blade to deburr tool for use where production or chamfer the front, back, or both requirements are low. The tool is used sides of holes, in one pass of the tool. Since the tool is manually actuated on multi-walled parts and on while the spindle continues to run, burrs and will produce non-qualified there is no “on-off” down time. Nobur intersecting holes. It will remove severe chamfers. The tool body pilots in the hole to be deburred. A quick-action The above steps can be repeated as many times as necessary, depending upon the number of walls in the part. Work is performed continuously, without having to stop the spindle. 24 1. The tool should be running in a spindle with the cutting blade in the extended position. The tool is fed into the workpiece. The burr on the outer edge of the first wall is quickly and easily removed. 2.The sliding sleeve is moved backwards to retract the blade. The workpiece is advanced to such a position that, when the blade is again extended by a forward movement of the sleeve, it will lie between the two walls. The burr on the inner edge of the first wall is then easily removed. 3.Continued advancement of the tool allows the inner edge of the second wall to be deburred. The sleeve is moved backwards once again to retract the blade so that it can pass through the hole in the second wall. The blade is again extended to deburr the outer edge of the second wall.
Open the catalog to page 1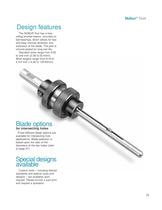
Nobur® Tool Design features The NOBUR Tool has a freerolling knurled sleeve, mounted on ball bearings, which allows for fast and easy manual retraction and extension of the blade. The pilot is chrome-plated for long tool life. Standard sizes range from 3/32 to one inch (2.38 to 25.4mm). Work lengths range from 9/16 to 4-3/4 inch (14.28 to 120.65mm). Blade options for intersecting holes Three different blade options are available for intersecting hole applications. Blade selection is based upon the ratio of the diameters of the two holes (refer to page 27). Special designs available Custom...
Open the catalog to page 2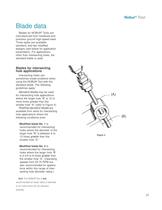
Nobur® Tool Blade data Blades for NOBUR® Tools are manufactured from hardened and precision ground high-speed steel. Three styles are available: standard, and two modified designs (see below for application parameters). For applications other than intersecting holes, the standard blade is used. Blades for intersecting hole applications Intersecting holes can sometimes create problems when using the NOBUR Tool with the standard blade. The following guidelines apply: Standard blades may be used for intersecting hole applications where the larger hole “B” is 12 or more times greater than the...
Open the catalog to page 4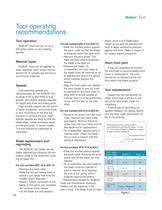
Nobur® Tool Tool operating recommendations Tool operation NOBUR® Tools can be run on a drill press, lathe, or any rotating spindle. Material types NOBUR Tools can be applied on steel, stainless steel, brass, bronze, aluminum, or virtually any ferrous or non-ferrous materials. Speeds Low operating speeds are recommended for the NOBUR Tool. A range of 50 to 650 RPM is suggested, with slower speeds required for larger tool sizes and heavy parts. High spindle speeds will not result in faster production, since only three or four revolutions of the tool are required to remove the burr. High...
Open the catalog to page 5All Cogsdill - Nuneaton catalogs and technical brochures
-
Generating Heads
8 Pages
-
Nobur JA Recessing Head
8 Pages
-
AEX Series
4 Pages
-
U Series
2 Pages
-
SR Series
6 Pages
-
CX Machine Selection Guide
8 Pages
-
Roll-a-Finish Bill of Materials
31 Pages
-
Burnishing
64 Pages
-
Smooth Edge Deburring Tool
12 Pages
-
ZX Systems Overview
4 Pages
-
ZX MBT-S brochure
5 Pages
-
ZX MBT-T brochure
5 Pages
-
Tools
8 Pages
-
Grooving
6 Pages
-
Flipcut
16 Pages
-
ZX Systems
36 Pages
-
Recessing
64 Pages
-
Reaming
48 Pages
-
Deburring
28 Pages