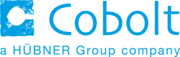

Catalog excerpts
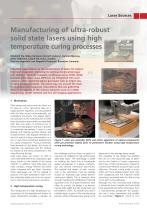
Laser Sources Manufacturing of ultra-robust solid state lasers using high temperature curing processes Elizabeth Illy, Håkan Karlsson, Kenneth Joelsson, Gunnar Elgcrona, Jonas Hellström, Cobolt AB, Solna, Sweden Dag von Gegerfelt, von Gegerfelt Photonics, Bensheim, Germany Industrial expectations on the performance of lasers for today’s high-tech diagnostic instruments continue to grow stronger and stronger. Typically compact, continuous wave (CW), diode pumped solid state lasers (DPSSLs) are integrated into such systems, often replacing legacy gas lasers such as Argon ion, or lamp pumped systems. The lasers may run around the clock in analytical and diagnostic instruments that are gathering data in all aspects of life science research, such as in DNA sequencing, cancer research and live cell imaging applications. 1 Motivation DNA sequencing instruments are often run for days at a time, generating data on a single genome sequence, and any problem with the laser source could potentially risk invalidating the results. This applies significant pressure on the manufacturers of DPSS lasers to produce lasers which are essentially fault free over years of continual use. In theory, this may appear trivial but in practice it is extremely demanding. A laser is a very delicate and typically sensitive device, and its performance may degrade severely as a result of optical surface contamination or a µm or sub-mrad mechanical displacement of a cavity component. This puts extremely high demands on the design, the choice of materials, the cleanliness and the method for fixation of the cavity components in the manufacturing process. Solid state lasers are known to offer a much extended lifetime as compared to gas lasers, thanks to the stability of the lasing medium. In addition, solid state lasers are more compact, energy efficient and silent when compared with gas lasers. However, these advantages can not be realised in practice if the laser assembly in itself is neither extremely stable over time nor insensitive to thermal and mechanical variations. 2 High temperature curing The introduction of a high temperature curing process for the assembly and fixation of cavity components provides a solution to Originally published in German in Photonik 1/2010 Figure 1: Laser pre-assembly (left) and active alignment of optical components with µm precision (right), prior to permanent fixation using high temperature curing technology this challenge and has shown to result in a new level of reliability for high performance solid state lasers. The technology is based on building the lasers into a hermetically sealed sub-package in a planar configuration and without mechanical sub-mounts. The material and design of each component in the architecture must be carefully chosen for extremely high overall thermomechanical stability. This is foremost done through matching the coefficients of thermal expansion (CTE) of all parts involved to each other. As a result, the design is so thermomechanically stable that the whole laser can be heated to 150°C, for several hours and in multiple steps, as part of the manufacturing process, without the laser cavity going out of alignment or any damage being caused. This capability of the design has enabled the use of a new advanced type of adhesive for the fixation of cavity components that cures at high temperatures, instead of conventional methods using UV light curing adhesives. Thermal curing yields a much stiffer and more reliable fixation joint, free from outgassing and the long-term drifts sometimes associated with the after-curing of UV light curing adhesives. Although this new manufacturing method is inherently more complex and technically more advanced than other techniques, from a manufacturing perspective the production line is more streamlined and suitable for automation (figure 1), which in turn
Open the catalog to page 1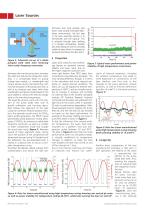
Laser Sources formance over long periods, also when used outside controlled laboratory environments, the last step in the laser assembly process is to hermetically seal the capsule. This is achieved through laser welding in a nitrogen atmosphere, thereby also eliminating the risk for humidity inside the laser, when it is exposed to temperatures below the dew point. Figure 2: Schematic set-up of a diode pumped solid state laser featuring intra-cavity frequency conversion Lasers built using this new technol- Figure 3: Typical noise performance and power ogy feature an improved intensity...
Open the catalog to page 2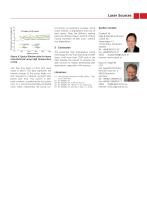
Laser Sources rent shows no systematic increase, which could indicate a degradation and loss of laser power. Note the different starting points for different lasers, the first of them having exceeded 25 000 hours without any degradation. Figure 6: Typical lifetime data for lasers manufactured using high temperature curing new (the first lasers of that kind were made in 2007). This data represents the relative change of the pump diode current required to maintain constant laser power over time. This current is relatively constant, considering the test conditions in a...
Open the catalog to page 3All COBOLT catalogs and technical brochures
-
Cobolt FIC-06
1 Pages
-
Cobolt FIC-05
1 Pages
-
Cobolt FIC-04
1 Pages
-
Cobolt FIC-03
1 Pages
-
Cobolt FIC-01
1 Pages
-
Cobolt Tor™ Series
2 Pages
-
Cobolt Odin™ Series
2 Pages
-
Cobolt 08-01 Series lasers
3 Pages
-
Cobolt 06-01 Series lasers
3 Pages
-
Cobolt 05-01 Series lasers
3 Pages
-
Cobolt Modulated DPSS lasers
2 Pages
-
Cobolt 04-01 Series Lasers
3 Pages
-
LIBS application note
4 Pages
-
Cobolt Dual Combiner
2 Pages