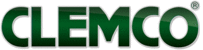
Group: Clemco
Catalog excerpts
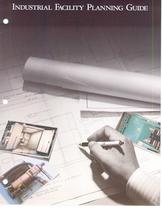
Industrial Facility Planning Guide
Open the catalog to page 1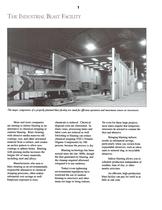
1 The major components of a properly planned blast facility are sized for efficient operation and maximum return on investment. chemicals is reduced. Chemical disposal costs are eliminated. In many cases, processing times and labor costs are reduced as well. Switching to blasting can reduce chemical stripping VOCs (Volatile Organic Compounds) by 100 percent, because the process is dry. Blasting technology has been around since the late 1800s, though the dust generated by blasting, and the cleanup required afterward relegated it to use outdoors. Today's ever-tightening environmental...
Open the catalog to page 2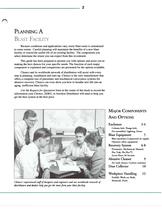
2 m Because conditions and applications vary, every blast room is customized to some extent. Careful planning will maximize the benefits of a new blast facility or extend the useful life of an existing facility. The components you select determine the return you can expect from this investment. This guide has been prepared to present you with options and assist you in making the best choices for your specific needs. The function of each major component is explained and comparisons are presented for the options available. Clemco and its worldwide network of distributors will assist with...
Open the catalog to page 3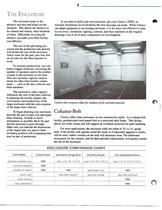
3 If you plan to build your own enclosure,g et your Clemco, ZERO, or 18 Aerolyte Distributor involved before the fIrst drawings are made. While Clemco can adapt equipment to an existing enclosure, it is far more cost effective to plan for recovery, ventilation, lighting, controls, and blast machines in the original drawings even if all of these components are not budgeted. The enclosure keeps in the abrasive and dust and keeps out the elements. This allows the abrasive to be cleaned and reused, often hundreds of times. Efficiently recycling the abrasive can make your blast facility cost...
Open the catalog to page 4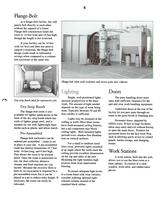
4 Flange-bolt room with reclaimer and reversep ulse dust collector: Doors The parts handling doors must open with sufficient clearance for the part and your work handling equipment. Additional doors at the rear of the facility let you pa.~sp arts through enroute to the paint booth or finishing area. Personnel doors, required by OSHA every 30 feet in large facilities, allow easy entry and exit without havin~~ to open the main doors. Position the personnel doors for the best work flow, such as allowing quick access to control panels, media storage, and changing rooms. 11\ Work Stations A work...
Open the catalog to page 5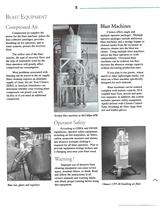
5 Blast Machines Clemco offers single and multiple operator packages. Multiple operator packages include additional blast machines and a storage hopper to channel media from the reclaimer or abrasive cleaner into the blast machines. Using multiple blast machines allows the blast operators to work independently. Oversized blast machines can be ordered. but they increase the abrasive storage capacity without increasing production rates. If you plan to use plastic, wheat starch or other lightweight media, you must use a blast machine specifically designed for such material. Blast machines can...
Open the catalog to page 6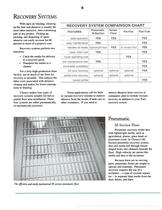
6 With open air blasting, cleaning up the dust and abrasive is usually the most labor-intensive, time-consuming part of any project. Picking up, packing, and disposing of spent abrasive can easily account for 60 percent or more of a project's cost. Recovery systems perform two functions: . Catch the media for delivery to a recovery point. . Transport the media to a cleaner. For a truly high-production blast facility, use as much of the floor for recovery as possible. This reduces the labor costs associated with abrasive cleanup and makes for fewer interruptions to blasting. Clemco makes...
Open the catalog to page 7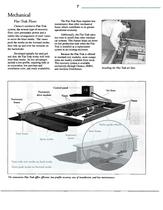
7 Mechanical Flat- Trak Floor Clemco's exclusive Flat- Trak system, the newest type of recovery floor, uses pneumatic power and a ladder-like arrangement of steel vanes to move the blast media. The vanes push the media on the forward stroke. then ride up and over the mounds on the backstroke. Developed initially for steel grit and shot. the Flat- Trak works well with most blast media. Its key advantages include a low profile. requiring little or no excavation.lo w purchasea nd installation costs, and ready availability. The Flat- Trak floor requires less maintenanced ian other mechanical...
Open the catalog to page 8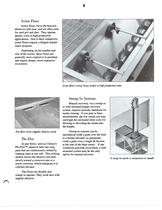
8 Screw Floor Screw floors move the heaviest abrasives with ease, and are often used for steel grit and shot. They operate quietly, even in high production applications. Due to their complexity, screw floors require a diligent maintenance program. Depending on the number and size of the screws, these floors are generally more expensive to purchase and require deeper, more expensive excavation. Screw floors convey heavy media at high production rates. Pan floors move angular abrasive easily. Sweep-In Systems Manual recovery, via a sweep-in or wall-mounted hopper recovery system, requires...
Open the catalog to page 9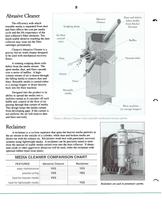
9 Abrasive Cleaner ,~ The efficiency with which reusable media is separated from dust and fines affects the cost per media cycle and the life expectancy of the dust collector's fIlter elements. Too much usable abrasive reaching the dust collector may wear out the filter cartridges prematurely. Clemco's Abrasive Cleaner is a gravity-fed air wash cleaner designed to be used with mechanical recovery floors. A rotating scalping drum culls debris from the media stream. The spent media. dust, and fines cascade over a series of baffles. A highvolume stream of air is drawn through the falling media...
Open the catalog to page 10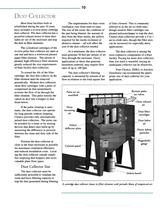
10 of filter element. This is commonly referred to as the air-to-cloth ratio, though modern filter cartridges use pleated polyester/paper to trap the dust. Clemco dust collectors provide a 2-to-l air-to-cloth ratio, though the filter area can be increased for especially dusty applications. The dust collector is among the most expensive components of a blast facility. Paying for more dust collection than you need is wasteful; buying an inadequate collector can be disastrous. Your Clemco, ZERO, or Aerolytf: Distributor can recommend the appropriate size of dust collector for your application....
Open the catalog to page 11All CLEMCO INDUSTRIES catalogs and technical brochures
-
Apollo 600
4 Pages
-
Wetblast FLEX
2 Pages
-
Apollo 20 HP
2 Pages
-
CLASSIC SERIES
12 Pages
-
Tumble Cabinets
8 Pages
-
Automated Air Blast Systems
8 Pages
-
BNP A200 Series
4 Pages
-
Debris Screen Basket
1 Pages
-
Options Plus
4 Pages
-
Cabinet Dust Collectors
8 Pages
-
Climate Control Tube (CCT)
2 Pages
-
Apollo 60 and 600
4 Pages
-
ZERO Automation
8 Pages
-
Pulsar III, VI & VI-P
6 Pages
-
Pulsar VI-PE
2 Pages
-
Pulsar IX Pressure PS
2 Pages
-
Pulsar III-PE
2 Pages
-
Pulsar III-P
2 Pages
-
Operator Safety Equipment
8 Pages
-
Clemco Mule
1 Pages
-
COMFORT VEST
7 Pages
-
FLAT-TRAK ®
29 Pages
-
RPH
11 Pages
-
RPC-2
12 Pages
-
Blast Suit & Gloves (Rev. I)
2 Pages
-
Internal Pipe Tools (Rev. A)
8 Pages
-
Big Clem Bulk Blast Machines
2 Pages
-
CAP-4 Ambient Air Pump
2 Pages
-
Tumble Cabinets
2 Pages
-
BNP Suction Blast Guns
2 Pages
-
MB series
2 Pages
-
CDF Dust Collectors (Rev. C)
4 Pages
-
CALIPSO Ambient Air Pump
2 Pages
-
Cool Air Tube (Rev. B)
2 Pages
-
INEX Blast Cabinet (Rev. E)
2 Pages
-
2-Braid Blast Hose (Rev. G)
1 Pages
-
Clem-Cool Air Conditioner
1 Pages
-
Super Comet
4 Pages
-
Pre-assembled blast-room
4 Pages
-
Blast Suit & Gloves (Rev. E)
2 Pages
-
Bulk Abrasive Blast Machines
2 Pages
Archived catalogs
-
Automated Air Blast Systems
6 Pages