
Group: CITIZEN Group
Catalog excerpts
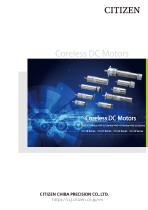
Series ● NC-15 Series ● NC-18 Series ● NC-25 Series
Open the catalog to page 1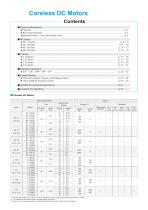
Coreless DC Motors Contents ■ General Information ● Features ● Basic Characteristics ● Model Number ・Unit Conversion Chart ■ NC Series ● NC-13 Series ● NC-15 Series ● NC-18 Series ● NC-25 Series ■ C Series ● C-18 Series ● C-21 Series ● C-23 Series ● C-32 Series ■ Control Drivers ● USE-2A for Speed, Torque, and Voltage Control ● TSD-04-060 for Position Control ■ Models for Special Environments ■ Coreless DC Motors Motor Specifications Size Series Specification (Rated) Voltage V Tachometer Generator *1 : The diameter of the motor alone is φ17mm and the one with encoder or tachometer...
Open the catalog to page 2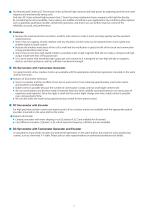
■ Our Miniaturized Coreless DC Servomotor Series achieved high response and high power by adapting powerful rare earth magnets and mechanically-strong coils. And also, NC-Series achived higher power than C-Series by using neodymium boron magnets with high flux density. By considering the actual usability, many options are availble according to your applications. By combining these options such as planetary gearhead, encoder, tachometer generator, and driver, you can further improve control of the reliability, accuracy, and performance. Because the mechanical time constant is small for rotor...
Open the catalog to page 3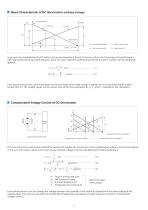
■ Basic Characteristic of DC Servomotor (at Rated Voltage) No Load Point Starting Point No:No Load Speed (rpm) In general, the characteristic of a DC motor can be represented by T-N and T-I Curves. In the case of moving coil type DC motors with high performance rare earth magnets, these two curves become perfectly linear for the armature reaction can be completely ignored. IS − IO I = IO + ・T(A) (1) TS NO N = N O − ・T(rpm) (2) TS From above formula, the current and speed can be calculated when rated voltage is applied to the motor and used by loaded torque...
Open the catalog to page 4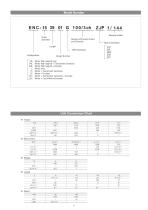
Model Number Outer Diameter Number of Encoder Pulses and Channels With Gearhead Design Number NC :Motor (Nd magnet) only TNC :Motor (Nd magnet) + Tachometer Generator ENC :Motor (Nd magnet) + Encoder C :Motor only TC :Motor + Tachometer Generator EC :Motor + Encoder ETC :Motor + Tachometer Generator + Encoder LEC :Motor + Cost-Effective Encoder Unit Conversion Chart ● Rotor Inertia
Open the catalog to page 5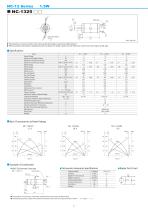
Motor Lead The positions of screw holes and motor lead (terminals) cannot be determined. ● When positive electrode is applied to the red lead, the shaft rotates to CW direction seen from the output shaft side. ● ■ Specifications Items Rated Voltage Maximum Allowable Output Maximum Continuous Current Maximum Continuous Torque Rated Output Rated Torque Rated Speed Rated Current No Load Speed No Load Current Starting Torque Starting Current Rotor Inertia Resistance Inductance Mechanical Time Constant EMF Constant Torque Constant Maximum Output at Rated Voltage Starting Acceleration Housing-to...
Open the catalog to page 6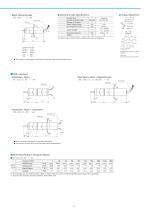
■ Optical Encoder Specifications Optical Encoder Encoder Type Number of Output Pulses Number of Channels Power Source Voltage Consumption Current Encoder Cable Motor Lead Response Frequency Weight Output Timing ( CW dorectoion seen from the output shaft side ) The positions of screw holes, motor lead, and encoder cable cannot be determined. Gearhead + Motor + Optical Encoder Encoder Cable Motor Lead Motor Lead Gearhead + Motor + Tachometer Tachometer Lead Motor Lead Blue Please see page 23 for details on gearhead dimensions. The positions of screw holes and motor lead cannot be determined. ■...
Open the catalog to page 7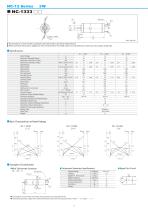
Motor Lead The positions of screw holes and lead wires (terminals) cannot be determined. ● When positive electrode is applied to the red lead wire, the shaft rotates to CW direction seen from the output shaft side. ● ■ Specifications Rated Voltage V W mA mN・m gf・cm oz・in W mN・m gf・cm oz・in rpm mA rpm mA mN・m gf・cm oz・in A g ・cm 2 Ω mH m-sec V / 10 3 rpm mN ・m/A gf・cm/A oz・in/A W rad / sec 2 ℃/ W − ℃ ℃ − − − g Maximum Allowable Output Maximum Continuous Current Maximum Continuous Torque Rated Output Rated Torque Rated Speed Rated Current No Load Speed No Load Current Starting Torque Starting...
Open the catalog to page 8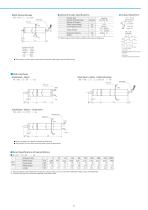
Optical Encoder ■ Optical Encoder Specifications Encoder Type Number of Output Pulses Number of Channels Power Source Voltage Consumption Current Encoder cable Motor Lead Response Frequency Weight Output Timing ( CW direction seen from the output shaft side ) The positions of screw holes, motor lead, and encoder cable cable cannot be determined. Gearhead + Motor NC −1333 □□G ZCP 1 / xxx ● Gearhead + Motor + Optical Encoder Encoder cable Motor Lead Motor Lead Gearhead + Motor + Tachometer Tachometer Lead Motor Lead Blue Please see page 23 for details on gearhead dimensions. The positions of...
Open the catalog to page 9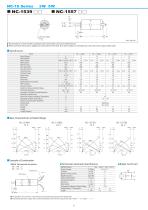
The positions of screw holes and lead wires (terminals) cannot be determined. ● When positive electrode is applied to the positive terminal, the shaft rotates to CW direction seen from the output shaft side. ● Items Rated Voltage Rated Output Rated Torque Rated Speed Rated Current No Load Speed No Load Current Starting Torque Starting Current Rotor Inertia Resistance Inductance Mechanical Time Constant EMF Constant Torque Constant Maximum Output at Rated Voltage Starting Acceleration Housing-to Ambient Thermal Resistance Winding Insulation Class Maximum Armature Winding Temperature...
Open the catalog to page 10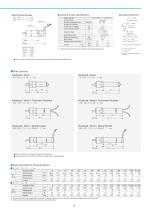
■ Optical Encoder Specifications Optical Encoder ENC −1539 □□ △△△ /3ch ENC −1557 □□ △△△ /3ch Encoder Cable Motor Lead Encoder Lead Color Phase A …… Green Phase B …… Yellow Phase Z …… White + 5V ……… Red GND ……… Black ● Rectangular Wave ( CW direction seen from the output shaft side ) t 1 +t 2 ,t 3 +t 4 =T/2±T/8 t 1 ,t 2 ,t 3 ,t 4 ≧T/8 T 0 =T±T/2 The position of Phase A, B and Z cannot be determined. The positions of screw holes, motor lead, and encoder cable cannot be determined. Gearhead + Motor + Optical Encoder Gearhead + Motor + Optical Encoder Gearhead + Motor + Tachometer Generator...
Open the catalog to page 11All CITIZEN CHIBA PRECISION CO. catalogs and technical brochures
-
Planetary Gearheads
5 Pages
-
Tachometer Generator
1 Pages
-
Linear Actuator
20 Pages
-
Brushless Motor
36 Pages
-
Galvanometer Optical Scanner
24 Pages
-
Miniaturized AC Servomotors
16 Pages