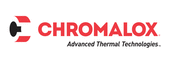
Catalog excerpts
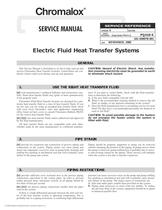
This Service Manual is furnished as an aid to help start-up andservice Chromalox Heat Transfer Systems. Listed below are con-ditions which could occur during start-up and operation. CAUTION: Hazard of Electric Shock. Any installa-tion involving electricity must be grounded to earthto eliminate shock hazard. > DO read manufacturers technical bulletins and instructions care-fully. Some heat transfer fluids may ignite or burn spontaneouslyif not properly used.Chromalox Fluid Heat Transfer Systems are designed for a par-ticular heat transfer fluid or a class of heat transfer fluids. If you are not sure you are using an accepted heat transfer fluid, checkwith your local Chromalox sales and application engineering office listed on back cover or consult Chromalox Bulletin PQ301for the correct heat transfer fluid. A. Is the new fluid compatible with the old? B. What is the recommended cleaning method to remove the oldfluid, its sludge, or any deposits remaining in the system? C. Does the fluid manufacturer have a reclaiming service for usedfluid? Do they have a recommended procedure for disposal of used or old fluid? CAUTION: To avoid possible damage to the heatersdo not energize the heater unless the system isfilled with fluid. DO NOT mix heat transfer fluids unless authorized and approvedby the fluid manufacturer.All heat transfer fluids are not compatible with each other,whether made by the same manufacturer or a different manufac- turer. If you plan to switch fluids, check with the fluid manufac-turer to determine the following. DO > provide for expansion and contraction of process piping andconnections to the system. Piping strains can cause pump andmotor mis-alignment, excessive wear on pump body, bearings and stuffing box packing or mechanical seal and will eventually causefailure of the pump and system.Piping should be properly supported so pump can be removedwithout changing the position of the piping. If piping moves whenthe pump is removed, pump malfunction is probably due to stress-es and twisting caused by the piping. These stresses will multiply when the system is hot due to thermal expansion. DO > provide sufficient cross sectional area in the process pipingconnections equivalent to the system pipes. In order to preventundue pressure drop, maximum velocity in all piping should beless than 10 feet per second. A. Inlet and outlet pipes smaller than provided on the system. B. Piping many processes in series with one another. To reducethe pressure drop of the system, equipment should be re-piped in balanced parallel flow. DO NOT use process piping connections smaller than the pipesused in the system.If there is a high differential pressure between the inlet and out-let of the heat transfer system at operating temperature, this isprobably due to a piping restriction. A continuing high differentialpressure can cause excessive wear on the pump and pump stuffingbox packing or mechanical seal and will eventually cause prema- ture failure of the pump. The major causes of restrictions are: > ҩ 1985 Wiegand Industrial Division, Emerson Electric Co. size="-2">
Open the catalog to page 1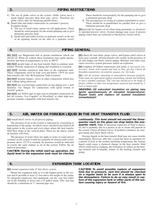
3. The passageways or coring of a platen manifolded in series.These should be re-manifolded for parallel flow to give a minimum pressure drop. C. The use of globe valves in the system. Globe valves have amuch higher pressure drop than gate valves. Therefore use globe valves only for balancing parallel flows. DO D. Small inlet and outlet connections on customers process.Examples being: 1. The use of small rotary unions on roll applications. Theseshould be sized properly for the actual pumping rate to giveminimum pressure drop. 2. Small inlet and outlet nozzles on jacketed vessels or the...
Open the catalog to page 2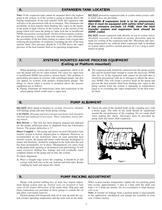
Note: If the expansion tank cannot be mounted above the highestpoint in the system, or if the system is going to operate above the boiling temperature of the heat transfer fluid, the expansion tank will have to be pressurized with air or nitrogen. This eliminates the possibility of heat transfer fluid flashing into vapor in the heater, at the point of high velocity in the system or at the suction of the pump which will cause the pump to vapor lock due to insufficient NPSH (net positive suction head). On hot oil heat transfer systems, this pressurizing is usually done with nitrogen as this...
Open the catalog to page 3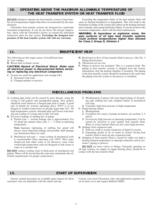
WARNING: Exceeding the temperature limits of the heat transfer fluid willcause its thermal breakdown or degradation. This will result in the formation of sludge in the system and carbon on the heating elements and eventually cause pump and heater failure. If you do not know this maximum temperature, check with the fluid manufacturer. In hazardous or explosive areas, thepipe surfaces of oil type heat transfer systemscould achieve temperatures higher than allowed for Class I, Group D, Division I. > The following are the major causes of insufficient heat: DO NOT attempt to operate any heat...
Open the catalog to page 4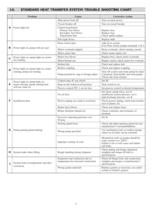
ProblemCauseCorrective Action A Power light offControl transformerPrimary fuse blownReplace fuse Secondary fuse blownReplace fuse Transformer badCheck and/or replacePilot light blownReplace bulb Float switch openAdd oil to system Main power feed offTurn on main power Circuit breaker offTurn on circuit breaker B Power light on, pump will not startIf no float switch, jumper terminals 4 & 5Motor overloads trippedReset overloads, check running currentMotor starter badCheck motor starter coil C Power light on, pump light on, motorMotor fuse blownReplace fuse, check motor overloadsnot...
Open the catalog to page 5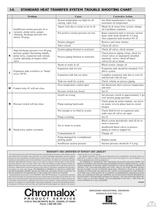
ProblemCauseCorrective Action System temperature too high for oilSee fluid manufacturers data forcausing vapor lockmaximum oil temperatureVapors lock due to steam or air in oilBleed air &steam from system, changeInsufficient suction pressure (0 oroil if problem continues J vacuum), pump noisy, gaugesNet positive suction pressure too lowRaise expansion tank to increase suctionvibrating, discharge pressure lowhead, static head should be 4-5 psig.(below 20 psig)(See expansion tank location No. 6)Strainer pluggedRemove and clean strainer Valve closedCheck all valvesHigh discharge pressure over...
Open the catalog to page 6All Chromalox catalogs and technical brochures
-
Thick Film Heater Technology
4 Pages
-
Tubular V-Seal
2 Pages