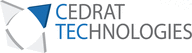

Catalog excerpts
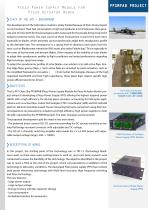
Piezo Power Supply Module for Piezo Actuator Bench PPSMPAB PROJECT STATE OF THE ART – BACKGROUND The development of the helicopters market is today limited because of their strong impact on environment: Their fuel consumption is high and produces a lot of emission; they generate a lot of noise both for the passengers (cabin noise) and for the people living close to the heliports (external noise). The main source of these inconvenient is due to the main rotor, especially its blades, which presently cannot dynamically adapt their aerodynamic profile to the desirable one. The consequence is a strong level of vibrations and noises from the rotor, such as Bladevortex interaction (BVI) noise, also called “blade slap”. This is especially in the cases of fast forward and descent flights. Other impacts of the inability of rotor blades to adapt their aerodynamic profiles to flight conditions are limited performance regarding flight envelope, speed and range. To adapt the aerodynamic profiles of rotor blades, one solution is to add active flaps (trailing edge flaps, gurney flaps...). Such active flaps are actuated by piezo actuators, such as the Amplified Piezoelectric Actuators (APA®) from Cedrat Technologies. Because of the high requested bandwidth and their high capacitance, these piezo flaps require specific high power efficient electronic drivers. OBJECTIVES The Eu FP7 Clean Sky PPSMPAB (Piezo Power Supply Module for Piezo Actuator Bench) project aimed at developing a Piezo Power Supply (PPS) offering the highest required power (9kVA) with a high efficiency, for driving piezo actuators, accounting for helicopter applications such as active flaps. Cedrat Technologies CTEC (coordinator, SME) and UJF-G2ELAB (partner, lab from Grenoble Joseph Fourier University) formed a consortium using their shared experience on piezoelectric actuators and high efficiency high power supplies to meet the GRC requested by the PPSMPAB project. The topic manager was Eurocopter. The proposed development split the need in two main items: - The preferred direct current (DC)-DC converter providing the DC sources would be an isolated full bridge resonant converter, with adjustable bus DC voltage. - The DC-AC 2-channels switching amplifier will provide the 2 x 4,5 kVA power with adjustable output voltage range (-200 / +1000V). Active flap of helicopter actuated by APA® (Collaboration between CTEC and Onera)era) CAD Overview of the Piezo Power Supply (PPS) Module DESCRIPTION OF WORKS In this project, the starting point of the technology was in TRL1-2 (Technology Readiness Level), as there were some existing bases to work on, and some basic research were conducted to assess the feasibility of the technology. The objective identified in the project was to reach a TRL4 at the end of the project, which corresponded to a validation of the technology in laboratory conditions. The developed Piezo power supply (PPS) has involved both power electronics technology with Multi level structure, High frequency switching and Piezo technology. The new features: - Large power output - Large output voltage - Energy recovery with Bus capacitor storage - Low consumption - Embedded solution for aeronautics Demonstrator of Piezo Power Supply
Open the catalog to page 1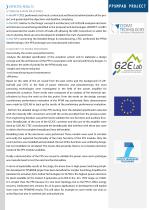
EXPECTED RESULTS a) TIMELINE & MAIN MILESTONES In the WP1 CTEC performed a technical, contractual and financial administration of the project and guaranteed the objectives and deadline complying. In the WP2 relative to the Design concept & architecture, UJF-G2ELAB analysed electronic architectures (several being identified in the proposal) and technologies (MOSFET vs IGBT) and presented the results in form of trade-off, allowing the GRC Consortium to select the one to develop. Mock up were developed to establish the main characteristics. In the WP3 concerning the Detailed design &...
Open the catalog to page 2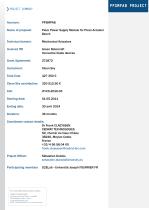
) PROJECT SUMMARY PPSMPAB PROJECT Acronym : Coordinator contact details: Dr Frank CLAEYSSEN For more information, please contact: CEDRAT TECHNOLOGIES 59 Chemin du Vieux Chene - Inovallee 38246 Meylan Cedex - France actuator@cedrat-tec.com Phone: +33 (0)4 56 58 04 00 - Fax: +33 (0)4 56 58 04 01
Open the catalog to page 3All CEDRAT TECHNOLOGIES catalogs and technical brochures
-
DTT35XS-SI-2
3 Pages
-
XY Piezo stages heritage
8 Pages
-
Fine and fast steering mirrors
10 Pages
-
Synchrotron Brochure
10 Pages
-
DTT35XS
3 Pages
-
TT60SM
3 Pages
-
APA600M
2 Pages
-
APA400M
2 Pages
-
APA200M
2 Pages
-
APA150M
2 Pages
-
APA100M
2 Pages
-
APA60SM
2 Pages
-
APA40SM
2 Pages
-
APA60S
2 Pages
-
APA50XS
2 Pages
-
APA35XS
2 Pages
-
APA150XXS
2 Pages
-
APA120S AND CAU10 AMPLIFIER
1 Pages
-
PPA20M
2 Pages
-
PPA40M
2 Pages
-
PPA40L
2 Pages
-
PPA60L
2 Pages
-
PPA80L
2 Pages
-
PPA120L
2 Pages
-
PPA40XL
2 Pages
-
PPA80XL
2 Pages
-
RK42F3U-LC75B
2 Pages
-
CA45
4 Pages
-
LA75A
4 Pages
-
LA75B
4 Pages
-
LA75C
3 Pages
-
SA75A
3 Pages
-
SA75B
3 Pages
-
SA75D
3 Pages
-
SP75A
3 Pages
-
UC65
3 Pages
-
UC55
3 Pages
-
UC45
2 Pages
-
RK42F3U-LC24
2 Pages
-
ECSU10
2 Pages
-
ECS75
3 Pages
-
ECP1000
2 Pages
-
ECP500
2 Pages
-
XY25XS
2 Pages
-
APA30uXS
2 Pages
-
PPA10M
2 Pages
-
FP7 SONO PROJECT
2 Pages
-
ASPIC PROJECT
1 Pages
-
viper cleansky project
2 Pages
-
MISAC PROJECT
2 Pages
-
AEROPZT PROJECT
2 Pages
-
DYNXPERTS PROJECT
1 Pages
-
E-LIFT3 PROJECT
1 Pages
-
FluMIn3 projecT
1 Pages
-
CONTACTLESS TORQUE SENSORS
2 Pages
-
MC-SUITE Project
3 Pages