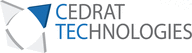

Catalog excerpts
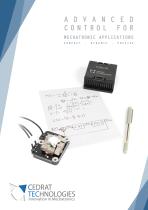
A D V A N C E D CONTROL FOR MECHATRONIC APPLICATIONS CEDRAT TECHNOLOGIES Innovation in Mechatronics
Open the catalog to page 1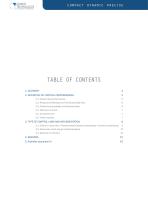
CEDRAT TECHNOLOGIES Innovation in Mechatronics compact dynamic precise TABLE OF CONTENTS 1. GLOSSARY 2. DEFINITION OF CONTROL PERFORMANCES 2.2. Rising time/Settling time/Overshoot/Delay time 2.3. Closed-loop bandwidth and flatness/delay 3. TYPE OF CONTROL LAWS AND IMPLEMENTATION 3.1. Control in open loop : Flatness-based trajectory preshaping + harmonic preshaping 3.3. Advanced control using full state feedback
Open the catalog to page 2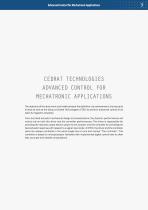
Advanced Control for Mechatronic Applications CEDRAT TECHNOLOGIES ADVANCED CONTROL FOR MECHATRONIC APPLICATIONS The objective of this document is to briefly present the definition, the achievement, the key parts & laws as well as the setup at Cedrat Technologies (CTEC) to perform advanced control of its piezo & magnetic actuators. From any fixed actuator mechanical design & characteristics, the dynamic performances will mainly rely on both the driver and the controller performances. The driver is responsible for providing the required output electric power to the actuator and the controller...
Open the catalog to page 3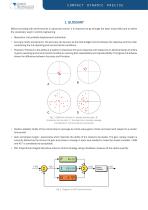
CEDRAT TECHNOLOGIES Innovation in Mechatronics compact dynamic precise 1. GLOSSARY Before providing with performances in advanced control, it is important to go through the basic lexical field and to define the vocabulary used in control engineering. • Resolution: the smallest displacement achievable • Accuracy: static and dynamic, the accuracy can be seen as the total budget of error between the response and the order considering the full operating and environmental conditions. • Precision: Precision is the ability of a system to reproduce the same response with respect to an identical...
Open the catalog to page 4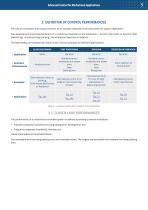
Advanced Control for Mechatronic Applications 2. DEFINITION OF CONTROL PERFORMANCES The role of a controller is to reduce the error of an actuator response vs an input order for a given application. The development and implementation of a control law depends on the application / function like static or dynamic (fast positioning), microscanning, tracking, microvibrations’rejection or isolation…. The table below summarises the needs in term of error analyses for different applications. SLOW POSITIONING FAST POSITIONING Analysed Performances Amplitude error Combined error: amplitude and phase...
Open the catalog to page 5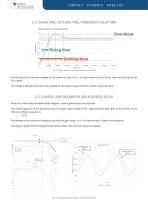
CEDRAT TECHNOLOGIES Innovation in Mechatronics compact dynamic precise 2.2. RISING TIME/SETTLING TIME/OVERSHOOT/DELAY TIME Fig. 3 : Step response and associated parameters The settling time is the time needed for the system to stay in a +/- x% band around its final value. Here the settling time at 5% is given. The rising (or falling) time is the time needed for the system to go from 10% to 90% of its final value. 2.3. CLOSED-LOOP BANDWIDTH AND FLATNESS/DELAY From the control loop bandwidth Bode diagram, several parameters are extracted. The cutoff frequency is the frequency where the gain...
Open the catalog to page 6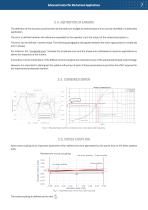
Advanced Control for Mechatronic Applications 2.4. DEFINITION OF ERRORS The definition of the accuracy could be seen as the total error budget as several types of error can be identified in a dedicated application. The error is defined between the reference requested by the operator r and the output of the closed-loop system y. The error can be defined in several ways. The following paragraphs distinguish between the main approaches (in amplitude and in phase). For instance, the “combined error” includes the amplitude error and the phase error addressed in dynamic applications to define the...
Open the catalog to page 7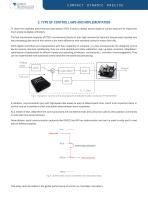
CEDRAT TECHNOLOGIES Innovation in Mechatronics compact dynamic precise 3. TYPE OF CONTROL LAWS AND IMPLEMENTATION To reach the expected performances cited above, CTEC is able to design several types of control laws and to implement them inside its digital controllers. The fast mechanical response of CTEC mechanisms (thanks to their high mechanical resonant frequencies) requires very fast processing (few tens of kHz) which is the main difference with standard control of motor (few kHz). CTEC digital controllers are characterised with their capability to compute in a few microseconds the...
Open the catalog to page 8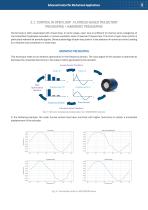
Advanced Control for Mechatronic Applications 3.1. CONTROL IN OPEN LOOP : FLATNESS-BASED TRAJECTORY PRESHAPING + HARMONIC PRESHAPING Control loop is often associated with closed loop. In some cases, open loop is sufficient to improve some categories of non-linearities (hysteresis excluded) or reduce excitation level of resonant frequencies. This kind of open loop control is particularly relevant for periodic signals. Obvious advantage of open loop control is the absence of numerical control, leading to a reduced cost compared to a close loop. HARMONIC PRESHAPING This technique relies on an...
Open the catalog to page 9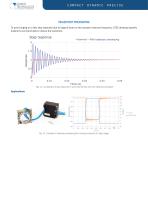
CEDRAT TECHNOLOGIES Innovation in Mechatronics compact dynamic precise TRAJECTORY PRESHAPING To avoid ringing on a fast step response due to large Q factor at the actuator resonant frequency, CTEC develops specific trajectory command able to reduce the overshoot. Fig. 11 : Comparison of step response in open loop without and with trajectory preshaper Fig. 12 : Example of trajectory preshaping for microscanning with XY piezo stage
Open the catalog to page 10
Advanced Control for Mechatronic Applications 3.2. PID CONTROL In most of the cases, the previous open loop preshaping solutions do not have sufficient robustness & efficiency to reach the ultimate & required accuracy. In those cases, a closed loop control shall then be implemented. At first, CTEC provides control laws based on PID regulator& filters (such as low pass or Notch filters) with the following advantages: • Versality of the control law built around the standard industrial PID controller • Easy adjustment by the customer of different parameters depending on its application. This...
Open the catalog to page 11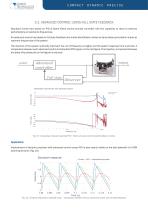
CEDRAT TECHNOLOGIES Innovation in Mechatronics compact dynamic precise 3.3. ADVANCED CONTROL USING FULL STATE FEEDBACK Standard Control law based on PID & Notch filters cannot provide controller with the capability to react to external perturbations at resonance frequencies. An advanced control law based on full state feedback and model identification allows to damp these perturbation inputs at resonant frequencies of the system. The dynamic of the system is directly improved: the cut off frequency is higher and the system response time is shorter. A comparison between such advanced control...
Open the catalog to page 12All CEDRAT TECHNOLOGIES catalogs and technical brochures
-
DTT35XS-SI-2
3 Pages
-
XY Piezo stages heritage
8 Pages
-
Fine and fast steering mirrors
10 Pages
-
Synchrotron Brochure
10 Pages
-
DTT35XS
3 Pages
-
TT60SM
3 Pages
-
APA600M
2 Pages
-
APA400M
2 Pages
-
APA200M
2 Pages
-
APA150M
2 Pages
-
APA100M
2 Pages
-
APA60SM
2 Pages
-
APA40SM
2 Pages
-
APA60S
2 Pages
-
APA50XS
2 Pages
-
APA35XS
2 Pages
-
APA150XXS
2 Pages
-
APA120S AND CAU10 AMPLIFIER
1 Pages
-
PPA20M
2 Pages
-
PPA40M
2 Pages
-
PPA40L
2 Pages
-
PPA60L
2 Pages
-
PPA80L
2 Pages
-
PPA120L
2 Pages
-
PPA40XL
2 Pages
-
PPA80XL
2 Pages
-
RK42F3U-LC75B
2 Pages
-
CA45
4 Pages
-
LA75A
4 Pages
-
LA75B
4 Pages
-
LA75C
3 Pages
-
SA75A
3 Pages
-
SA75B
3 Pages
-
SA75D
3 Pages
-
SP75A
3 Pages
-
UC65
3 Pages
-
UC55
3 Pages
-
UC45
2 Pages
-
RK42F3U-LC24
2 Pages
-
ECSU10
2 Pages
-
ECS75
3 Pages
-
ECP1000
2 Pages
-
ECP500
2 Pages
-
XY25XS
2 Pages
-
APA30uXS
2 Pages
-
PPA10M
2 Pages
-
FP7 SONO PROJECT
2 Pages
-
ASPIC PROJECT
1 Pages
-
viper cleansky project
2 Pages
-
MISAC PROJECT
2 Pages
-
PPSMPAB PROJECT
3 Pages
-
AEROPZT PROJECT
2 Pages
-
DYNXPERTS PROJECT
1 Pages
-
E-LIFT3 PROJECT
1 Pages
-
FluMIn3 projecT
1 Pages
-
CONTACTLESS TORQUE SENSORS
2 Pages
-
MC-SUITE Project
3 Pages