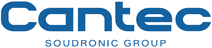
Catalog excerpts
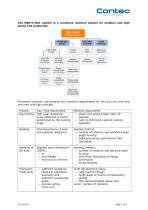
The END-O-MAT system is a combined machine system for medium and high speed end production. Processes, can/end requirements and machine requirements for thin and low cost cans and ends with high strength: Process Die-necking Can / End requirement high axial resistance: axial resistance is mainly determined by the necking angle Machine requirement steep neck angle smaller than 30 degrees neck re-forming by second necking operation interdependence of axial and paneling resistance adapted seam dimensions (SEFEL) m mini-flange mini-curl on the end sufficient resistance thanks to optimized geometry and sufficient countersink depth precise curling (mini-curl) beading method number of rotations and advanced bead depth forming bead geometries optimized by FEA calculation seaming method: number of rotations and advance seam forming only minor fluctuation of flange dimensions swing-flanging multi-die stamping press: rigid machine design multi-stage or thermo compensating tooling FEA optimized panel design disc curler: number of rotations
Open the catalog to page 1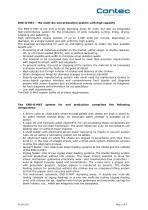
END-O-MAT – the multi-die end production system with high capacity The END-O-MAT is not only a single stamping press for ends, but also an integrated high-performance system for the production of ends including curling, lining, drying, wrapping and palletizing. High performance means outputs of up to 4,000 ends per minute, depending on diameter, on a single system and with uniformly high quality. The essential prerequisites for such an endmaking system to obtain the best possible benefit are: Processing of all materials available on the market, either single- or double-reduced, tin- or...
Open the catalog to page 2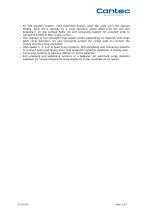
An end ejection system. Cam-controlled kickers eject the ends from the opened tooling. Each die is reached by a cross conveyor which takes over the end and deposits it on the outfeed belts. An end conveying system for uncurled ends to connect the END-O-MAT to the curlers. One (zigzag) or two (straight) high-speed curlers (depending on capacity) with large pitch circle diameter. An end conveying system for curled ends to connect the curlers and the lining machines. High-speed 3, 4, 6 or 8-head lining systems. End uprighting and conveying systems to connect liners and drying oven. End...
Open the catalog to page 3All Cantec catalogs and technical brochures
-
Capmaking systems CAP-O-MAT
8 Pages
-
Multi-die systems END-O-MAT
8 Pages
-
UNIPRESS
2 Pages
-
Soudronic Company
32 Pages
-
Testing systems
2 Pages
-
ECONOMIC CURING SYSTEMS
6 Pages
-
Seam protection systems
8 Pages
-
SQUAREPACK ® line to produce
2 Pages
-
BODYSHAPER
2 Pages
-
INLINE TACTILE MARKING UNIT
2 Pages
-
Sheet Feeder
6 Pages
-
END-O-MAT press
2 Pages
-
liner
1 Pages
-
Cap making systems
8 Pages
-
CAN-O-MAT Aerosol
2 Pages
-
Powder Monitor SPM-2
2 Pages
-
Belt Conveyor Transfer TX2
1 Pages
-
Cepak Slitter Equipment
4 Pages
-
Cepak Slitters
6 Pages
-
HEAt SEALING SYSTEM
2 Pages
-
Cepak Hybrid Slitters
2 Pages
-
Automatic canbody welders
6 Pages
-
BODYPACK
2 Pages
-
END-O-MAT Multi-die systems
8 Pages