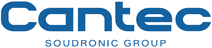
Catalog excerpts
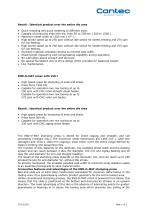
Result : Identical product over the entire die area Quick retooling and quick resetting to different sizes. Capable of producing ends with dia. from 50 to 250mm ( 200 to 1000 ). Maximum sheet width of 1200 mm ( 47” ). High stroke speed up to 250 spm without idle stroke for sheets feeding and 275 spm for coil feeding. High stroke speed up to 250 spm without idle stroke for sheets feeding and 275 spm for coil feeding. Excellent material utilization thanks to minimal web width. Sheet length measuring and compensating capability during operation. No lubrication above product and die level. No special foundation due to drive design which provides for balanced weight. Low maintenance. END-O-MAT press with 150 t High speed press for stamping of ends and shells. Press force 1500 kN. Capable for operation two row tooling at up to 250 spm with CNC roller straight sheet feeder. Capable for operation two row tooling at up to 275 spm with CNC roller coil feeder. Result : Identical product over the entire die area High speed press for stamping of ends and shells. Press force 500 kN. Capable for operation one row tooling at up to 230 spm with CNC zigzag sheet feeder. The END-O-MAT stamping press is dened for sheet (zigzag and straight) and coil processing (straight only). The maximum sheet dimensions are 1200 mm x 1200 mm (straight) and 1100 x 1200 mm (zigzag); sizes which cover the entire range defined by today's printing and lacquering lines. The number of dies depends on the diameter, the available sheet width and the feeding system and can reach between 2 dies (for diameter 153 mm and zigzag feeding and 16 dies (for end diameter 52 mm and straight feeding). The speed of the stamping press depends on the diameter, too, and can reach up to 250 strokes/minute for end diameter 52, without idle stroke. As already mentioned, the smallest possible web width to minimize scrap skeleton waste is an essential prerequisite to save material costs. Innovative features and advantages of the END-O-MAT stamping press Bed and slide are of solid steel construction calculated for minimum deformation in the tooling area, thus guaranteeing uniform product geometry for the entire tooling area. Unlike conventional stamping presses, the END-O-MAT press is powered from below, this means that the slide is positioned at the bottom and executes its strokes in an upward direction. The main advantage of this den is the absence of lubricating points for guides, gearwheels or bearings in or above the tooling area which prevents any soiling of the
Open the catalog to page 1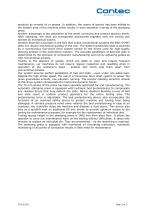
products by mineral oil or grease. In addition, the centre of gravity has been shifted to the bottom area of the machine which results in even smoother running of the stamping press. Another advantage is the separation of the sheet conveying and product ejection levels. After stamping, the ends are transported downwards together with the tooling and ejected by mechanical kickers. Another essential innovation is the fact that unlike conventional systems the END-O-MAT does not require mechanical guiding of the ram. The bottom-positioned slide is powered by a synchronous four-point drive...
Open the catalog to page 2All Cantec catalogs and technical brochures
-
Capmaking systems CAP-O-MAT
8 Pages
-
Multi-die systems END-O-MAT
8 Pages
-
UNIPRESS
2 Pages
-
Soudronic Company
32 Pages
-
Testing systems
2 Pages
-
ECONOMIC CURING SYSTEMS
6 Pages
-
Seam protection systems
8 Pages
-
SQUAREPACK ® line to produce
2 Pages
-
BODYSHAPER
2 Pages
-
INLINE TACTILE MARKING UNIT
2 Pages
-
Sheet Feeder
6 Pages
-
END-O-MAT
3 Pages
-
liner
1 Pages
-
Cap making systems
8 Pages
-
CAN-O-MAT Aerosol
2 Pages
-
Powder Monitor SPM-2
2 Pages
-
Belt Conveyor Transfer TX2
1 Pages
-
Cepak Slitter Equipment
4 Pages
-
Cepak Slitters
6 Pages
-
HEAt SEALING SYSTEM
2 Pages
-
Cepak Hybrid Slitters
2 Pages
-
Automatic canbody welders
6 Pages
-
BODYPACK
2 Pages
-
END-O-MAT Multi-die systems
8 Pages