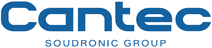
Catalog excerpts

MACHINES FOR STAMPING, FORMING AND LINING OF LUG CAPS Technology that k eeps you ahead
Open the catalog to page 1
END-O-MAT CAP LINER Rotary cap liner for plastisol with maximized sector for lining • Capacity between 300 epm and 1200 cpm with 4-, 6-, 8-, or 12-fold tooling, diameter range between 32 mm and 89 mm • Operator-friendly menus with size-dependent parameter memory (accessed when changing to a different size) reproducible lined ends • Fine setting of lining guns (nozzle position) separately in radial and axial direction: In radial direction (diameter setting) by means of a threaded spindle, in axial direction (gun height) by means of a threaded spindle better compound placement position
Open the catalog to page 2
TWIST-OFF™ CAP AND PT CAP PRODUCTION WITH END-O-MAT MULTI-DIE CAP SYSTEM High-speed production line consisting of: • Sheet feed stamping press to produce cap shells, type END-O-MAT • Rotary cap former with pre-curling, curling and lugging, type CAP-O-MAT • Lacquer hair aspiration with antistatic unit • Liner for plastisol compound, type END-O-MAT • Drying and curing unit • Video inspection • Packaging • Conveying END-O-MAT Multi-die cap system STAMPING PRESS FORMING system lining SYSTEM END-O-MAT machines Tooling system for cap stamping END-O-MAT rotary cap liner Cap press, 150 t for double...
Open the catalog to page 3
Combined strength and precision: the END-O-MAT multi-die stamping presses. Advanced 4-point drive system dispenses with need for slide guiding system. SHEET FEED END-O-MAT - THE INNOVATIVE CAPMAKING SYSTEM SYSTEMS • Quick retooling and quick resetting to different sizes • Capable of producing caps with dia. from 32 to 89 mm • Maximum sheet width of 1200 mm (47") • Excellent material utilisation thanks to minimal web width • No lubrication above product and die level • No special foundation due to drive design which provides for balanced weight • Low maintenance END-O-MAT cap pRESS wiTH 150...
Open the catalog to page 4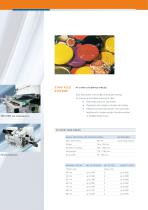
STRIP FEED SYSTEMS P4 STRIP FEED PRESS P4 STRIP STAMPING PRESS Strip feed press with single and double tooling for stamping and deep drawing of caps • Strip feed press for cap shells • Operated with single or double die tooling • Mechanical strip feed system for automatic feeding with single-scrolled, double-scrolled or straight-sided strips single or double-die stamping press accessoires Max. press force 400 kN Lubricating system nominal cap dia. no. of strokes no. of dies capacity caps strokes / MIN. shells / MIN.
Open the catalog to page 5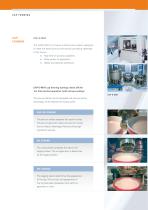
The CAP-O-MAT is a mature multi-function system designed to meet the technical and commercial canmaking challenge of the future. l High level of process capability Wide variety of application Safety and operator protection CAP-O-MAT cap forming toolings (twist off) for 1st, 2nd and 3rd operation (with rail pre-curling) CAP-O-MAT The pre-curl station can be equipped with rail pre-curling technology, which reduces the tooling costs Rail pre-curling The pre-curl station prepares the cap for curling. The pre-curl geometry takes into account nosing and curl radius. Adventage: Rail pre-curling...
Open the catalog to page 6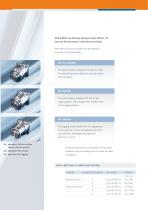
CAP-O-MAT cap forming toolings (twist off) for 1st, 2nd and 3rd operation (with die pre-curling) Alternativly the pre-curl station can be achieved in die pre-curling technology DIE PRE-CURLING The pre-curl station prepares the cap for curling. The pre-curl geometry takes into account nosing and curl radius. The curling station prepares the cap for the lugging station. The curl geometry is determiner by the lugging station. The lugging station determines the appearance of the cap. The function and appearance of the lug have been developed with optimum geometry in mind. 1st operation: Rail...
Open the catalog to page 7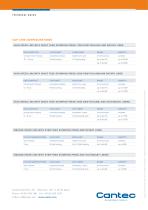
Cantec GmbH & Co. KG Helenenstr. 149 D - 45143 Essen Phone + 49 201 633 1461 Fax + 49 201 633 1239 E-Mail info@cantec.com www.cantec.com TECHNICAL DATAS STRAIGHT SHEET FEEDING HIGH-SPEED VERSION ROTARY CAP LINER OF APPLICATION CAPS/MIN. high-speed line with SHEET Feed STAMpING pRESS (ONE-ROw TOOLING)AND rotary liner zig zag sheet feeding high-speed version rotary cap liner of application CAPS/MIN. END-O-MAT 50 T CAP-O-MAT CAP LINERS RANGE CAPACITY ZIG zag SHEET FEEDING HIGH-SPEED VERSION STATIONARY, 3 UNITS OF APPLICATION CAPS/MIN....
Open the catalog to page 8All Cantec catalogs and technical brochures
-
Multi-die systems END-O-MAT
8 Pages
-
UNIPRESS
2 Pages
-
Soudronic Company
32 Pages
-
Testing systems
2 Pages
-
ECONOMIC CURING SYSTEMS
6 Pages
-
Seam protection systems
8 Pages
-
SQUAREPACK ® line to produce
2 Pages
-
BODYSHAPER
2 Pages
-
INLINE TACTILE MARKING UNIT
2 Pages
-
Sheet Feeder
6 Pages
-
END-O-MAT
3 Pages
-
END-O-MAT press
2 Pages
-
liner
1 Pages
-
Cap making systems
8 Pages
-
CAN-O-MAT Aerosol
2 Pages
-
Powder Monitor SPM-2
2 Pages
-
Belt Conveyor Transfer TX2
1 Pages
-
Cepak Slitter Equipment
4 Pages
-
Cepak Slitters
6 Pages
-
HEAt SEALING SYSTEM
2 Pages
-
Cepak Hybrid Slitters
2 Pages
-
Automatic canbody welders
6 Pages
-
BODYPACK
2 Pages
-
END-O-MAT Multi-die systems
8 Pages