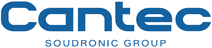
Catalog excerpts
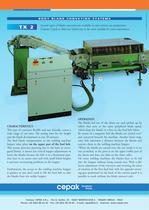
BODY BLANK CONVEYING SYSTEMS Several types of blank conveyors are available to suit various can production. Contact Cepak to find out which one is the most suitable for your requiremets. CHARACTERISTICS This type of conveyor, flexible and user friendly, covers a wide range of can sizes. The setting time for the height and the blank development is just 20 minutes. The final blank transportation to the welding machine hopper takes place on the upper part of the feed belt. This system prevents jamming due to the bent or corrugated blanks, it assures less critical hopper adjustments to lower the blanks because the belt is in a horizontal position (not in an ascent one) and with small blank heights it prevents overturning problems in the hopper Furthermore, the access to the welding machine hopper is quicker as you don’t need to lift the feed belt to take the blanks from the welder hopper. OPERATION The blanks fed out of the slitter are each picked up by rollers that turn at the same peripheral blade speed, which drop the blanks in a line on the feed belt below. By means of a magnetic belt the blanks are turned over* and conveyed beneath the machine. Another faster magnetic belt maintains a distance between the blanks and conveys them to the welding machine hopper. *When the blanks are turned over, the can inside is in no way scratched, as the print is on the upper visible part of the sheets and does not slide on the slitter table. On some welding machines the blanks have to be fed into the hopper without being turned over. With a different adjustment of the conveyor and reversing the sense of rotation of the first feed belt with the apposite reversing gear positioned on the back of the control panel it is possible to work without the blank turnover unit. Factory: CEPAK S.R.L. - Via G. Galilei, 23 - 42027 MONTECCHIO E. - REGGIO EMILIA - ITALY Phone +39 0522 86 62 03 - Fax +39 0522 86 50 64 - E-mail: cepak@tin.it - Internet: www:cepak.com
Open the catalog to page 1All Cantec catalogs and technical brochures
-
Capmaking systems CAP-O-MAT
8 Pages
-
Multi-die systems END-O-MAT
8 Pages
-
UNIPRESS
2 Pages
-
Soudronic Company
32 Pages
-
Testing systems
2 Pages
-
ECONOMIC CURING SYSTEMS
6 Pages
-
Seam protection systems
8 Pages
-
SQUAREPACK ® line to produce
2 Pages
-
BODYSHAPER
2 Pages
-
INLINE TACTILE MARKING UNIT
2 Pages
-
Sheet Feeder
6 Pages
-
END-O-MAT
3 Pages
-
END-O-MAT press
2 Pages
-
liner
1 Pages
-
Cap making systems
8 Pages
-
CAN-O-MAT Aerosol
2 Pages
-
Powder Monitor SPM-2
2 Pages
-
Cepak Slitter Equipment
4 Pages
-
Cepak Slitters
6 Pages
-
HEAt SEALING SYSTEM
2 Pages
-
Cepak Hybrid Slitters
2 Pages
-
Automatic canbody welders
6 Pages
-
BODYPACK
2 Pages
-
END-O-MAT Multi-die systems
8 Pages